Laboratory Portrait: Mervyn Rudgley – Vice President, Digital Manufacturing, Glidewell Laboratories
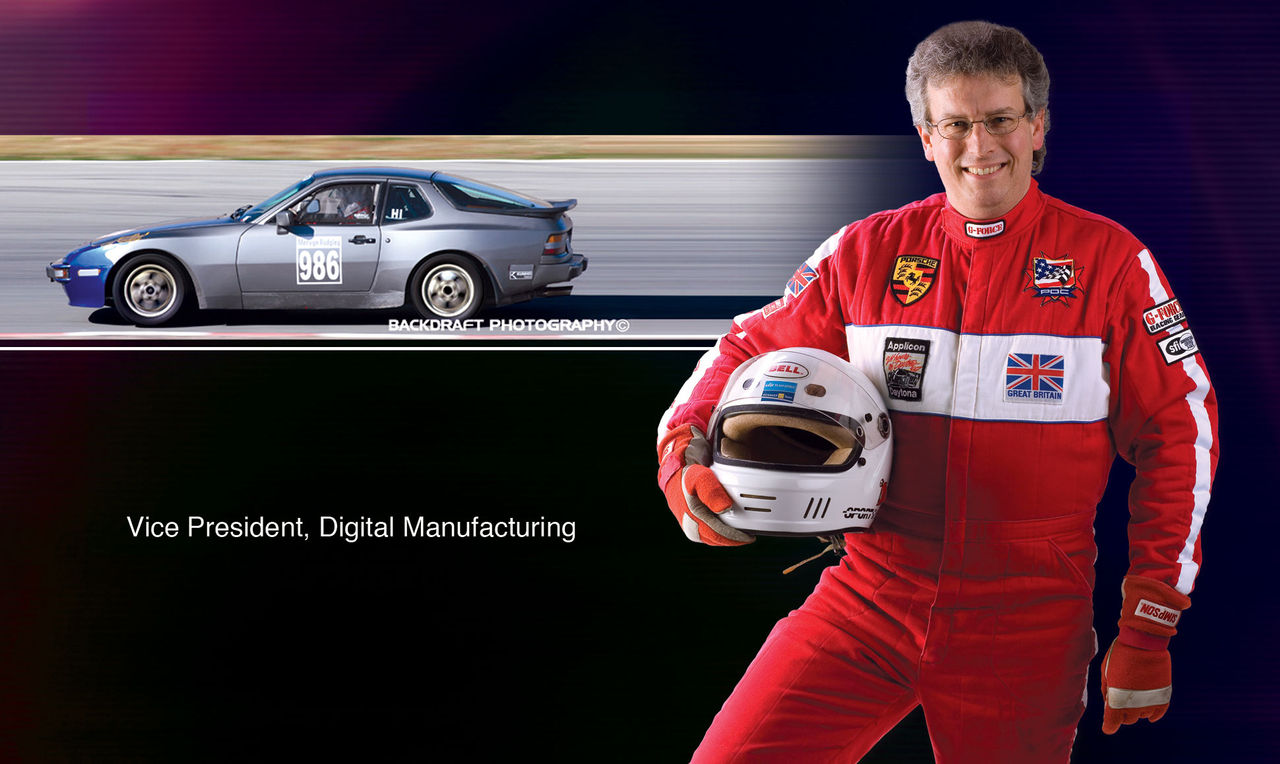
article by Kim Watkins
photos by Kevin Keithley
racing photo courtesy of Richard Hurtado/Backdraft Photography
What Mervyn Rudgley does not look like is a guy who carts around his Porsche to racetracks across California via RV in his spare time. What he does look like is a proper English gentleman — complete with well-tailored, conservative suits. With his curly, somewhat wild hair, he does resemble a bit of a mad scientist — a forward-thinker misunderstood by many. In reality, he is all of these things.
Rudgley, Glidewell Laboratories’ vice president of digital manufacturing, didn’t set out to revolutionize the dental technology industry. In fact, he has been with Glidewell a mere 12 months. But in that time, he has accomplished much, implementing a new form of manufacturing using CAD/CAM systems to add speed and consistency to crown production.
Rudgley, born in Southampton, U.K., graduated from the University of Salford, Manchester, with a BSc in mechanical engineering in 1978. Rudgley made the move to the United States with his wife Susie and her two children in 1991 to take a position at Applicon Inc.
Before he found his way to Glidewell Labs, Rudgley worked for a company involved in rapid prototyping, including work with 3D printers. He spent 10 years developing a market for this technology, in which data is input and a “printer” spits out a 3D object that you can hold in your hand. Products that were made with this technology included hearing aids and Invisalign® (Align Technology, Inc.; Santa Clara, Calif.), the custom-molded, clear teeth aligners. Essentially, Rudgley was a vendor for a company that sold these technology systems.
Then, Rudgley’s direction changed when Glidewell Laboratories owner and president Jim Glidewell purchased a 3D printer. Mr. Glidewell asked Rudgley to be his guest at the 2005 Chicago Dental Society Midwinter Meeting. He felt an alternate view was needed on the production processes of his lab — the view of an engineer. At the same time, Rudgley had been contemplating getting a different view himself. The view of a user of the technology.
Shortly after the lab show, Rudgley signed on with Glidewell. His goal: increase productivity and consistency on the lab floor through technology. From his office, tucked away in an attic-like area of Glidewell’s BioTemps® Dental Laboratory in Irvine, California, Rudgley and his crew of five staff members test out applications of the technology and train technicians to make the switch from benchwork to computer work.
The precision of 3D printing is seen in this replication of Mervyn Rudgley’s head, made using the technology Rudgley uses to make crowns.
For many, the idea of computer-aided design is foreign. Here’s the basic idea of how it works: A patient model is scanned. From there, the computer program generates suggested anatomy for the crown to be fabricated (this information appears on a computer screen). Next, a laboratory technician examines the on-screen suggestion. The technician can make changes on-screen based on his/her expertise. Once approved, the final anatomy is electronically transmitted to the 3D printer. A plate in the printer moves back and forth, while thousands of layers of ink are dispersed to form the correct shape. Once the process is finished, out comes a wax crown. Rudgley says CAD/CAM technology will help eliminate what he calls a “Friday crown,” referring to a difference in quality that can sometimes be seen in a crown produced Monday morning and one fabricated Friday afternoon.
Does it work? “It’s a dream come true,” says Jennifer Brunst, RDA, who runs Glidewell’s in-house operatory. “The full-gold crowns we’ve placed fit absolutely perfect!” There were no adjustments necessary for contacts or occlusion, Brunst says.
The full-gold department was the first to start implementing the technology. The feedback has been very positive, Rudgley says. He does admit that, at first, there were critics. In the beginning, people said this just didn’t work. That’s to be expected, Rudgley says. “It’s always going to feel like you’re going backwards before you take a big step forward.”
There was also fear of change. “This isn’t technology people should be afraid of. It’s technology people should be excited about,” Rudgley explains. There may be a shift in duties, he says, moving some technicians from workbenches to computer screens, but the technology opens up many opportunities. This technology, he says, will improve productivity and turn out an even higher quality product.
Today, the use of Rudgley’s digital manufacturing systems is accelerating. More departments in the lab, such as PFM and Wol-Ceram® (Wolz Dental-Technik GmbH; Ludwigshafen, Germany), are getting involved in digital manufacturing applications. Lab technicians receive two days of training on operating the scanner and three days of design training.
Acceleration is something Rudgley is familiar with. A car enthusiast since age 16, he spends much of his free time at racetracks. He is not a spectator of the sport, but a participant. His love of the sport began at age 21, when he began racing minis in his native U.K. After a few years of that, he decided to take a break from the track and began to build race engines for others as a hobby. In 1991, he was residing in Ann Arbor, Michigan, and by 1995 he called California his home. Rudgley’s passion was rekindled in 1999, when he was driving his Porsche Boxster and happened to drive by a track where Porsches were racing. He was hooked.
“This isn’t technology people should be afraid of. It’s technology people should be excited about.”
For the next three years, he and his wife trekked to racetracks on weekends in their motor home, which towed Rudgley’s Porsche. He competed in these “car vs. clock” competitions, earning second- and third-place honors, as well as winning a championship. After conquering that particular arena, Rudgley sold his original Porsche (“which hurt”) and got an older one that he outfitted with a roll cage appropriate for the next level of competition. That level comprises bigger tracks like California Speedway and Laguna Seca raceway.
Not only does Rudgley race, but he also finds time to teach entry-level drivers. “I’m the lunatic who shows them how to drive,” he says. Much like he is the one who teaches lab staff about this digital manufacturing stuff.
Just one year into his new job, Rudgley seems like a seasoned pro. His R&D team at Glidewell has launched a new digital process for the production of zirconia copings and frameworks under the brand name Prismatik Clinical Zirconia™.
As for the future of the technology now in use at Glidewell and in the medical field, Rudgley, a resident of Mission Viejo, California, sees much bigger things. On the dental front, it’s possible that one day dental assistants will be scanning the mouth rather than taking traditional impressions. That time is quite a ways off, however. Rudgley does believe that in as little as five years’ time, consumers will begin seeing more customized manufacturing. We will be able to go to a store, input data, and out of a 3D printer will come products like children’s toys. One day, he says, the technology will be in our homes. If we need to replace a doorknob or any number of other home items, we will simply go online, purchase a program for that item, download it, and print it out on our own 3D printers. The main obstacle to that now is expense. But one day, Rudgley says, it will happen.