How It’s Made: Exploring the Production Behind PlaySafe® Mouthguards
PlaySafe® sports mouthguards are highly effective protective appliances custom-built to your patient’s impressions. By providing this service to athletic patients of all ages, you can help prevent significant dental trauma during sporting activities. At Glidewell Laboratories, we use the Erkoform-3dmotion (ERKODENT® Erich Kopp; Germany) thermoforming machine, a countertop unit designed to expedite the manufacturing process through partial automation. Here is a peek inside the laboratory process.
How It’s Made
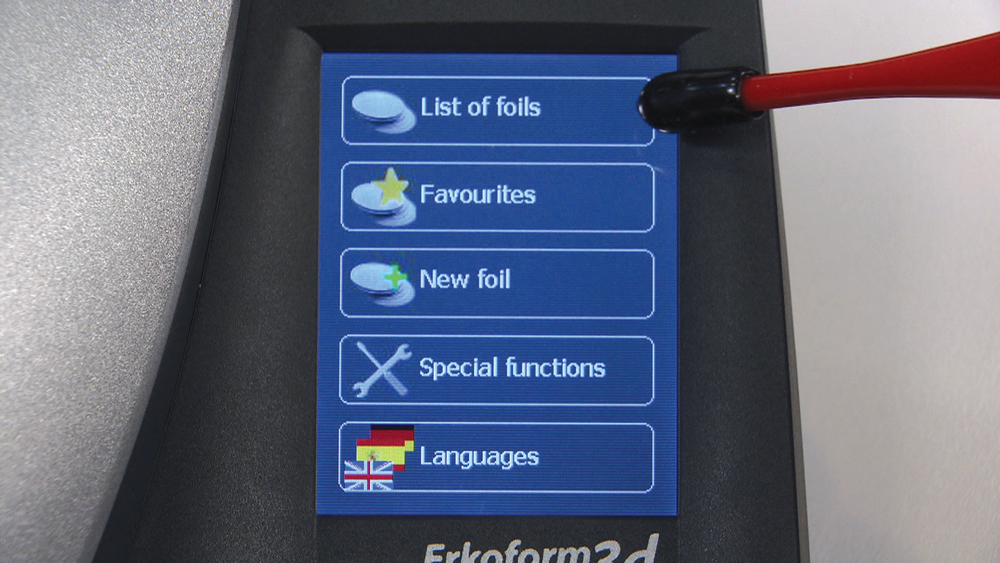
Figure 1: The technician programs the thermoforming unit specifically for the level of protection prescribed by the clinician. This case will demonstrate the process with the PlaySafe® Triple, which is a three-layered mouthguard that offers up to 5.5 mm of force-dispersing protection.
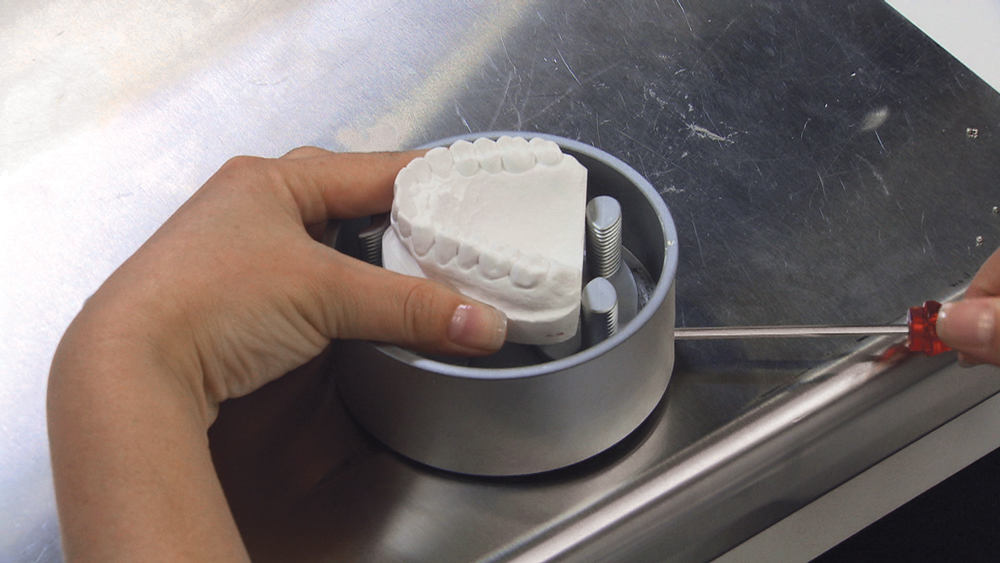
Figure 2: Upper and lower stone models are made and routed to the Thermoforming department. Next, the working model is secured into the thermoforming pot, and metal granules are added around the model. These granules allow the vacuum suction to mold the PlaySafe material to the working model while also ensuring the extra material is not pulled into the inner workings of the machine.
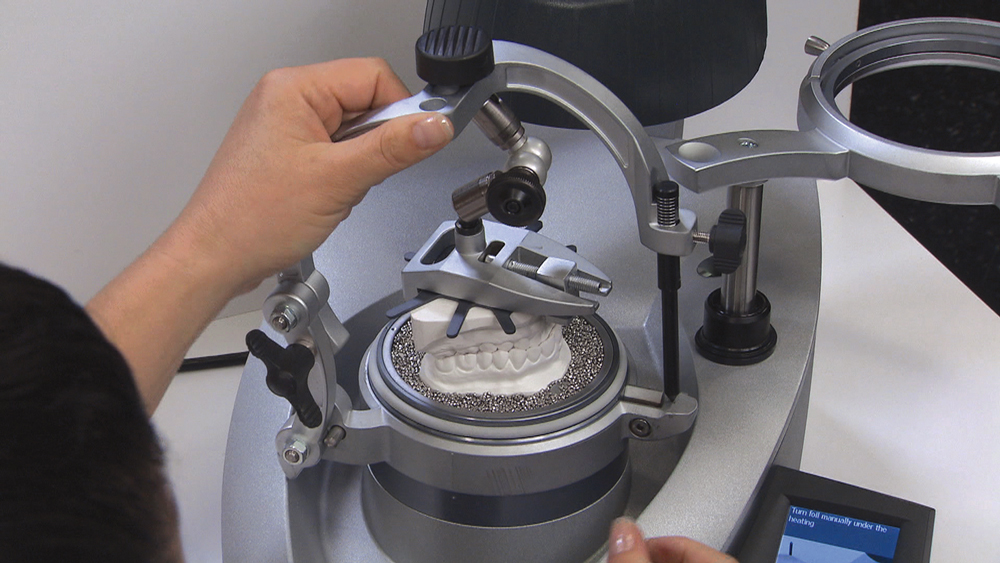
Figure 3: The opposing model is secured to a portion of the thermoforming unit called the Occluform-3 attachment (ERKODENT Erich Kopp). The Occluform is a mechanical arm that ensures the models maintain correct articulation despite being separated and occluded multiple times.
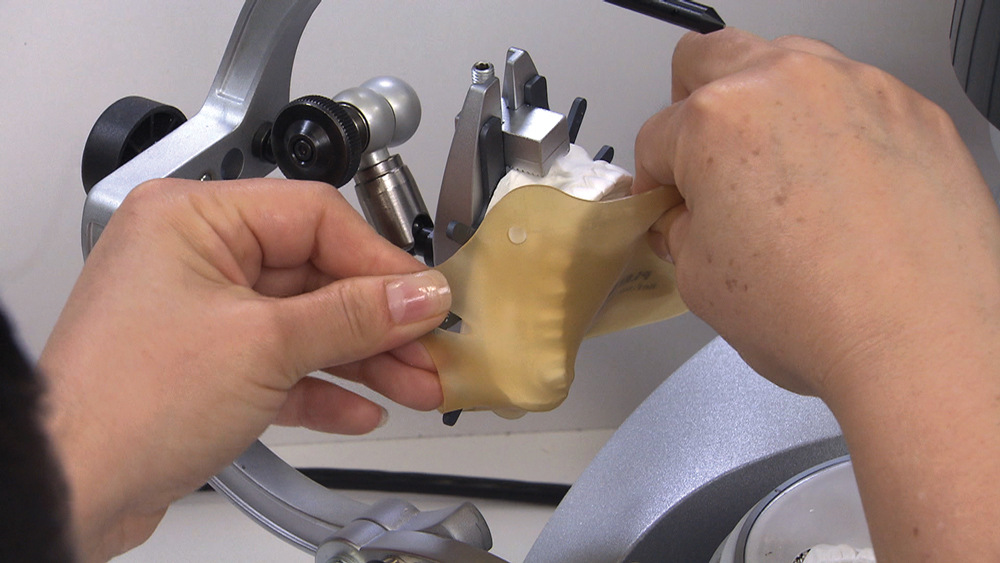
Figure 4: A membrane-like covering is placed over the opposing model on the Occluform-3. This acts as a bite spacer while also reducing the sharpness of any occluding edges on the opposing model.
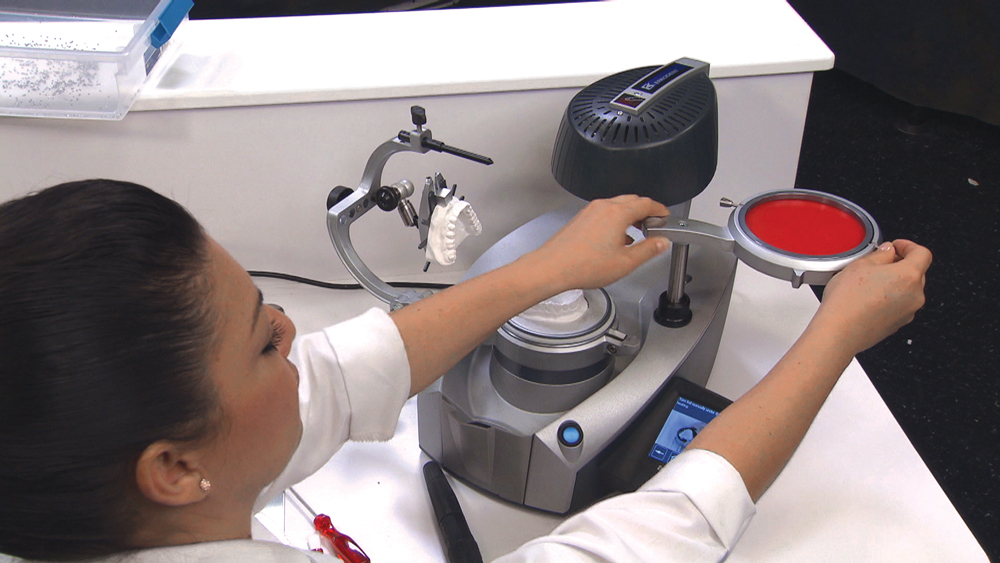
Figure 5: The foil is swung into position directly underneath the heating element. The machine will automatically start increasing the temperature to the optimum level for the PlaySafe Triple disc. Once the optimum temperature is reached, the foil will independently rotate and swing down onto the model. Then, the machine’s vacuum will automatically remove any air from the pot, sucking the foil down and forming it to the contours of the working model.
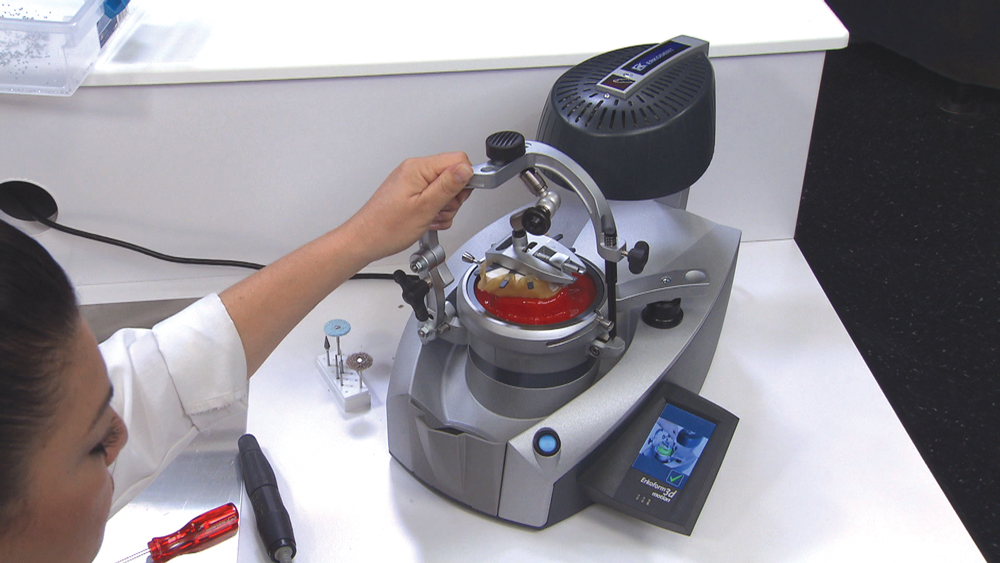
Figure 6: The Occluform, which holds the opposing model, is then closed onto the heated foil. This serves to leave an impression of the opposing bite on the mouthguard, significantly increasing patient comfort.
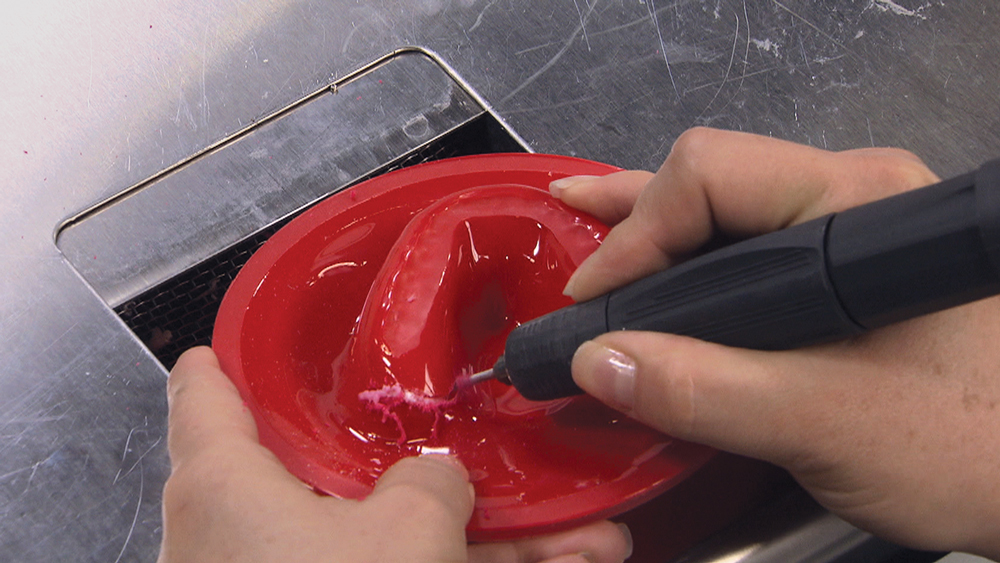
Figure 7: A low-speed handpiece is used to cut the excess foil material away from the appliance.
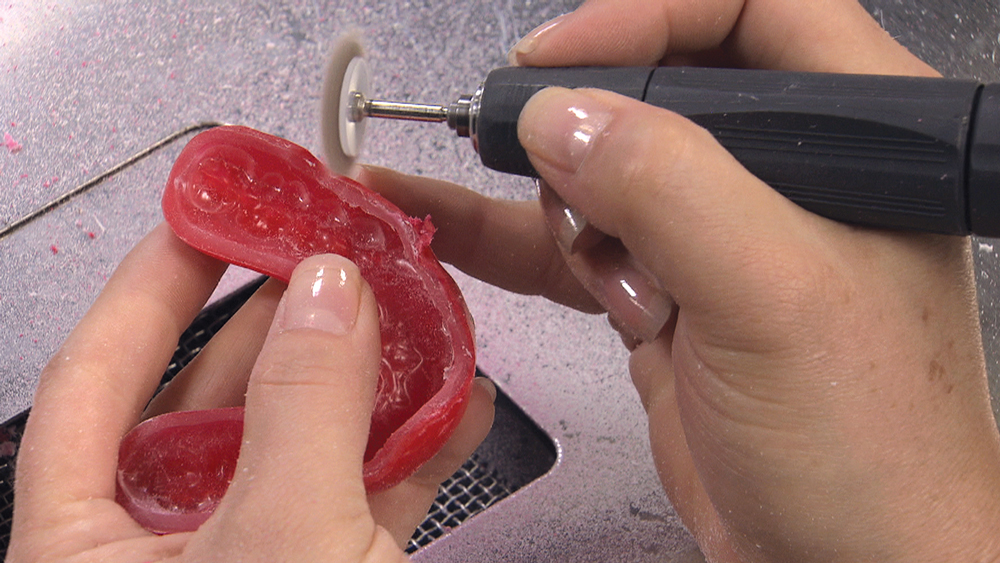
Figure 8: A series of burs is used to smooth and shape the edges of the entire appliance. Due to the appliance’s thickness, multiple passes are often needed. The technician ensures adequate cutouts around the maxillary or mandibular frenula to create a comfortable fit for the patient.
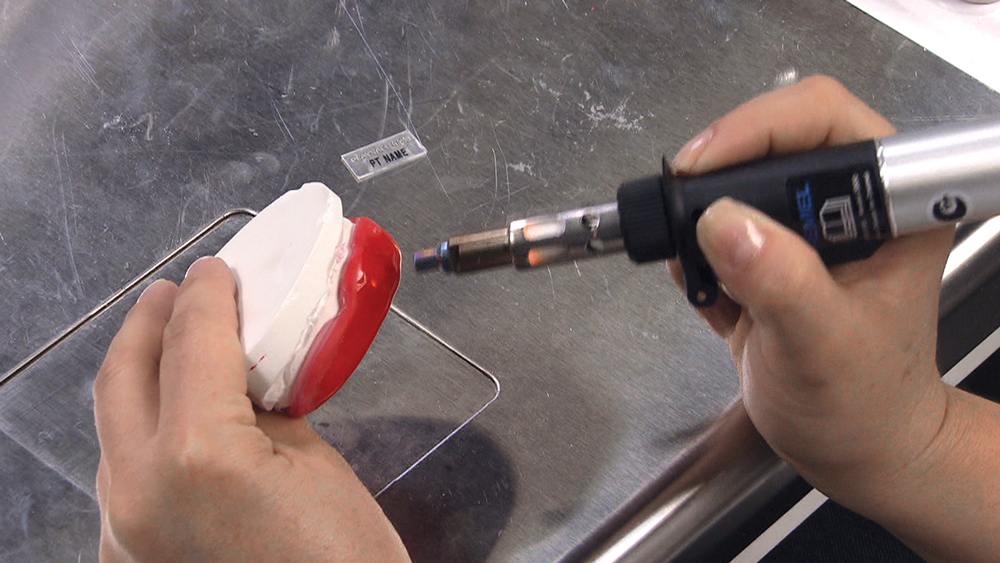
Figure 9: As an added benefit, PlaySafe sports mouthguards can be labeled with the patient’s name if desired. A hot air burner readies the area of the mouthguard where the label will be applied.
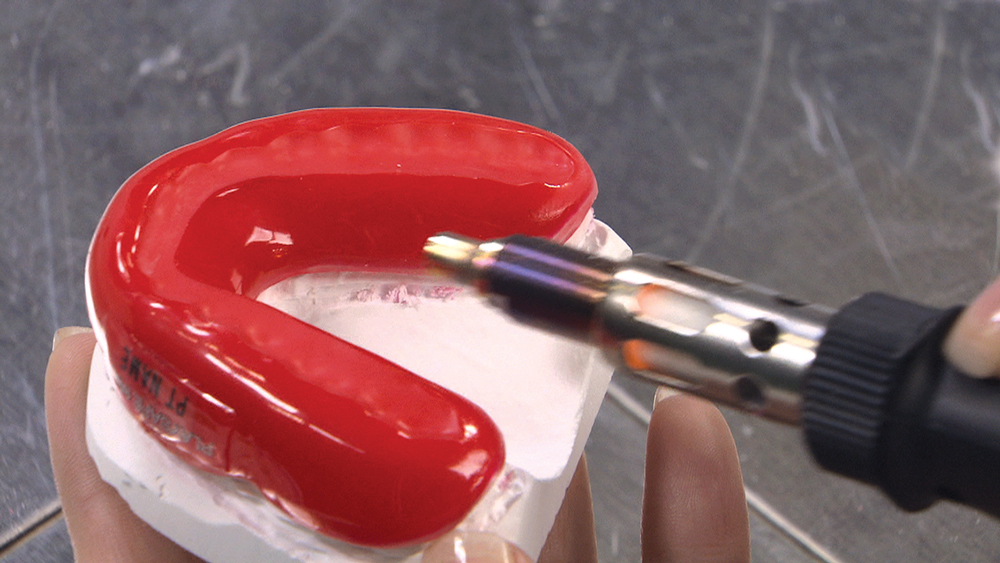
Figure 10: To polish the mouthguard to a high shine, the technician uses a hot air pen, slowly working around the entire edge of the appliance.
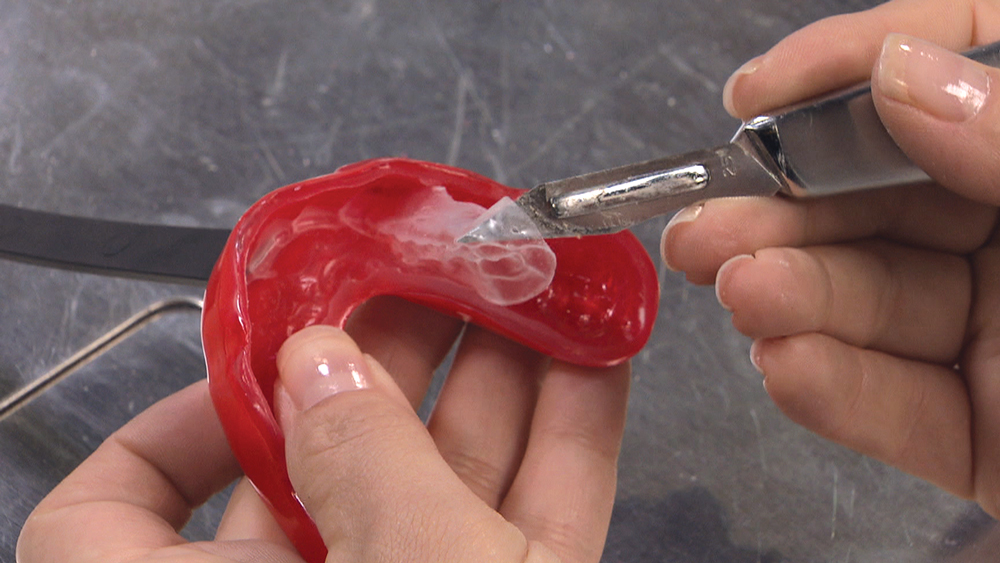
Figure 11: The technician then inspects the appliance to ensure it’s free of errors. Finally, the isolating foil, which has protected the intaglio surface during the manufacturing process, is peeled from the inner portion of the appliance. With all of these steps completed, the device is now comfortable for the patient and ready to provide a much-needed layer of protection.
Conclusion
Our technicians are proud to help dentists deliver preventive appliances that make a major difference for athletic patients across the nation. This straightforward service has been a beneficial addition to many practices, and we hope this behind-the-scenes look helps show the level of care that goes into each and every appliance.
WE'D LOVE TO HEAR FROM YOU
If you enjoyed this article and would like to see more behind-the-scenes lab features, please let us know by emailing chairside@glidewelldental.com.