A Digital Spin on Traditional Dentures
The advancements in crown and bridge fabrication resulting from digital technology are well known. Dental laboratories across the country have proven that fixed restorations made through digital workflows are more consistent and more accurate, and enable the use of stronger materials. Until recently, however, these technologies had not been applied to removable prosthetics, and it seemed as though the digital wave and those added benefits might just pass by the world of dentures.
The inroads thus far made into digitizing denture workflows have gained little more than fringe acceptance by clinicians, most likely due to the associated components required, such as technique-sensitive impression trays and tracing devices. From the perspective of the laboratory, it’s never been easy to ask a doctor to dramatically change his or her chairside methods to accommodate the lab, especially when a clinician’s current practices produce results that are more than clinically acceptable.
Though traditionally removable prostheses have served brilliantly over the years, reviewing the case statistics suggests that the traditional workflow is anything but ideal. A significant percentage of traditional-denture cases at Glidewell Laboratories require at least one return to the lab to accommodate a reset, which means at least one more appointment for the clinician and patient. While that has been tolerated by clinicians as a necessary component of the workflow, the Research & Development team at Glidewell knew something more efficient would be possible through the implementation of 3D printers.
With the aid of 3D printing technology, Glidewell Laboratories now offers a service that delivers a more accurate denture in far fewer appointments without requiring the clinician to change his or her methodology. What follows is a step-by-step overview of how we’ve employed digital tools to enhance denture workflow, benefiting clinicians and patients alike.
Adding Digital Technologies to Denture Workflows
Upon receiving an impression and bite registration from the clinician, stone models are poured by hand and then digitized through a laser scanning device. Once digitized, the new denture is designed completely in dental design software (Figs. 1, 2). From these data sets, clear try-ins are printed on a 3D printer in a biocompatible material (Fig. 3). These printed appliances are freed from the support 3D-printer material and cleaned so that they’re safe for seating. The six anterior teeth on each of the printed arches are replaced with actual denture teeth, and then tissue-colored wax is applied to secure those in place as well as to cover the facial aspect of each arch’s gingiva. This test-ready appliance is then returned to the dentist.
If the clinician did not include bite rims or a bite registration with the original case, Glidewell Laboratories is still able to offer a printed try-in device that can gather the missing anatomical data. The upper appliance is designed exactly like the one mentioned above, except its structure is based on anatomical averages and landmarks such as the incisive papilla. The lower portion is a traditional bite rim. With these two components seated in the mouth, the clinician can acquire a new bite registration thanks to the rigidity of the printed denture (Fig. 4).
The 3D-printed appliance offers a very accurate fit during try-in (Fig. 5). Further, the doctor and patient can envision the esthetics and function of the final appliance more easily through the aid of the denture teeth and tissue-colored wax. If the esthetics do not meet approval, the clinician can adjust the placement of the six anterior teeth chairside to secure the desired look, physically informing the lab of the necessary changes. Once approved, the adjusted appliance is returned to the laboratory for processing of the final appliance. If the entire fit or function of the appliance is inaccurate, the printed dentures can act as a custom impression tray for a brand-new impression. The clinician can simply do a wash impression in the 3D-printed appliance and then return that to the laboratory (Fig. 6).
With this workflow now in place for all denture cases at Glidewell Laboratories, a far lower percentage of cases require a return to the lab for reset (Fig. 7). This digital workflow has resulted in a more accurate workflow and aided in reducing the number of steps in denture fabrication.
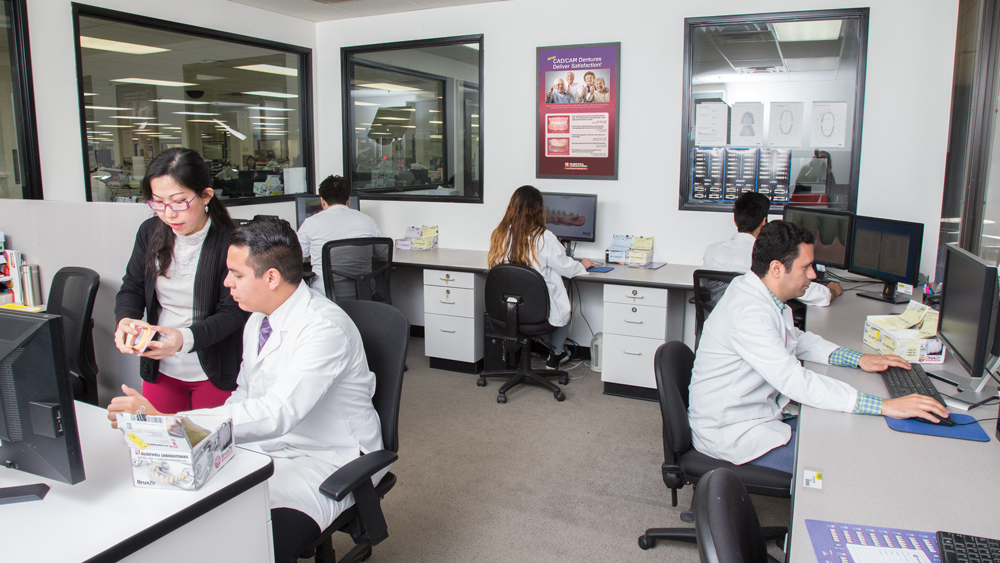
Figure 1: Specially trained CAD technicians scan stone casts and design dentures with computer software.
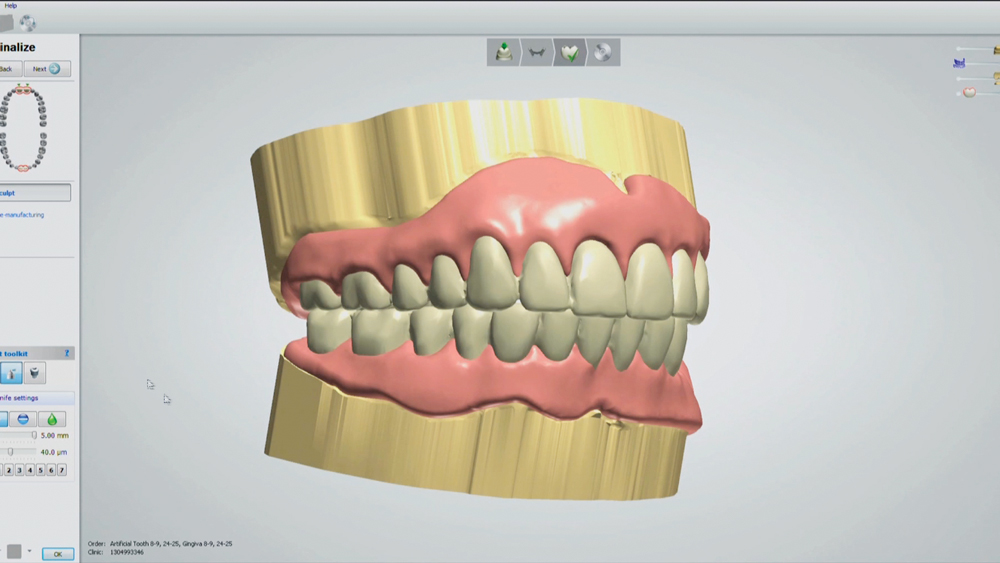
Figure 2: All digital dentures are designed with the incisive papilla as a point of reference, ensuring that the anatomic features are located correctly in relation to the rest of the mouth.
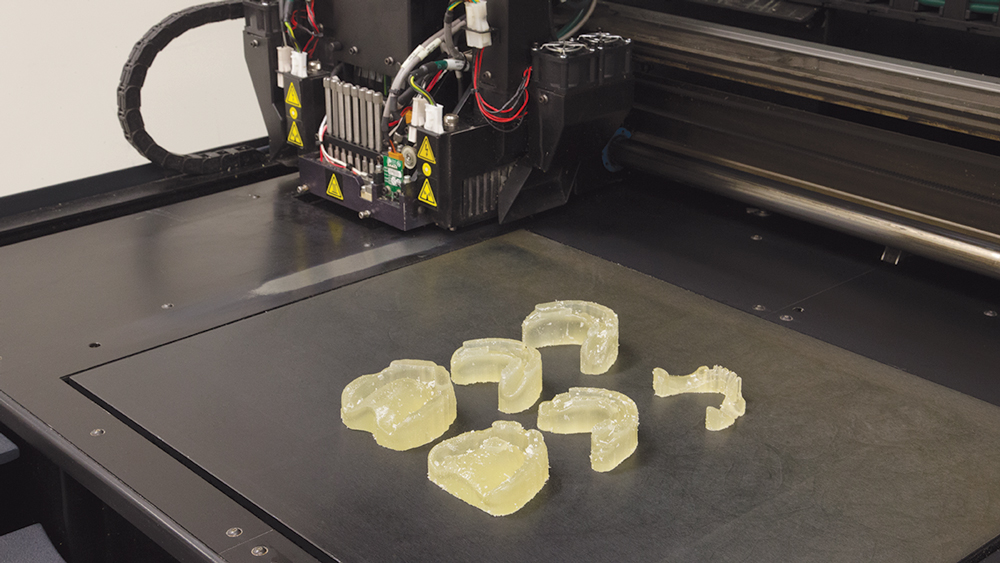
Figure 3: The digital designs are printed on a 3D printer, which cures layer upon layer until the final shape is achieved.
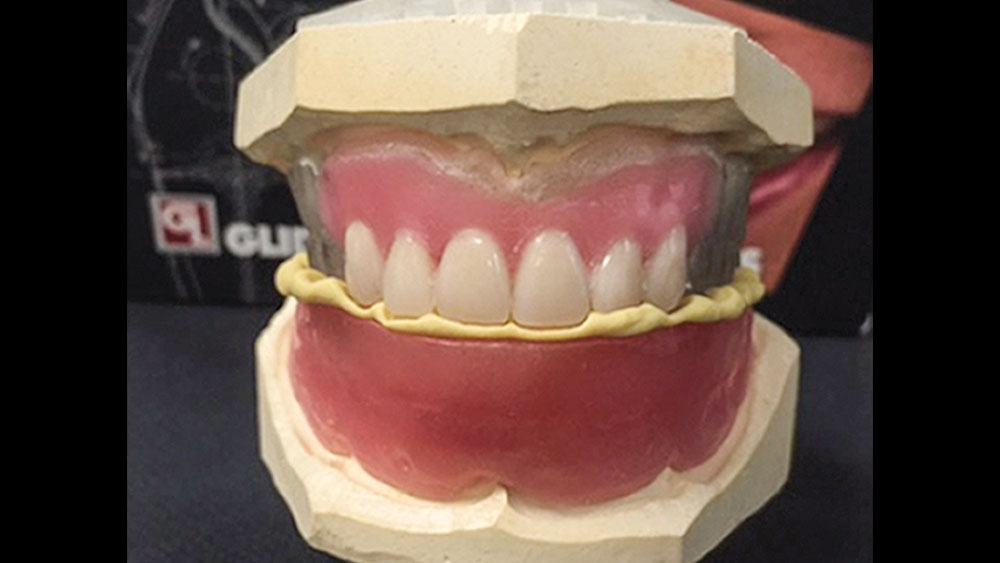
Figure 4: A printed try-in appliance with lower bite block is delivered to the clinician when no bite registration accompanies the initial case.
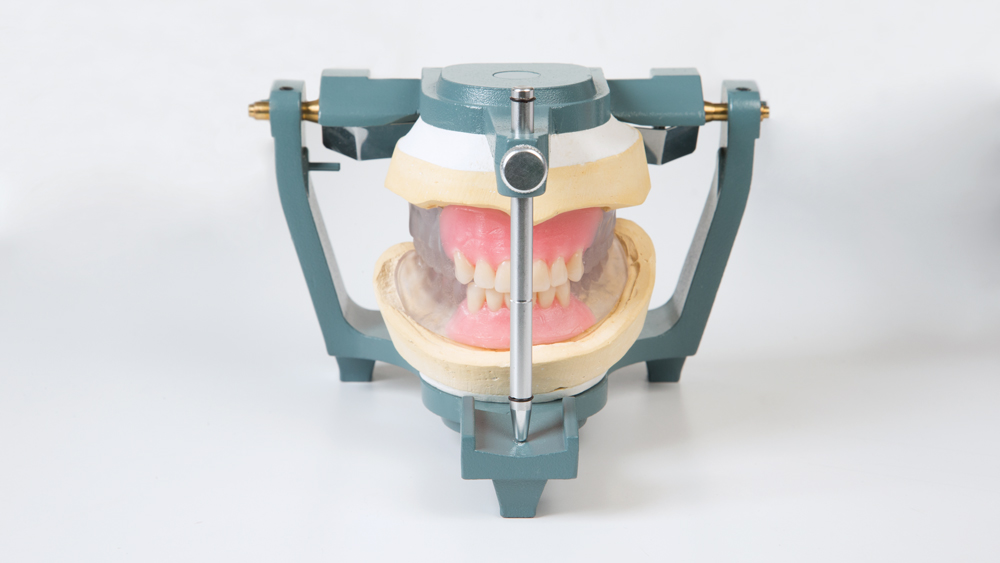
Figure 5: The printed try-ins with wax and denture teeth applied to the anterior.
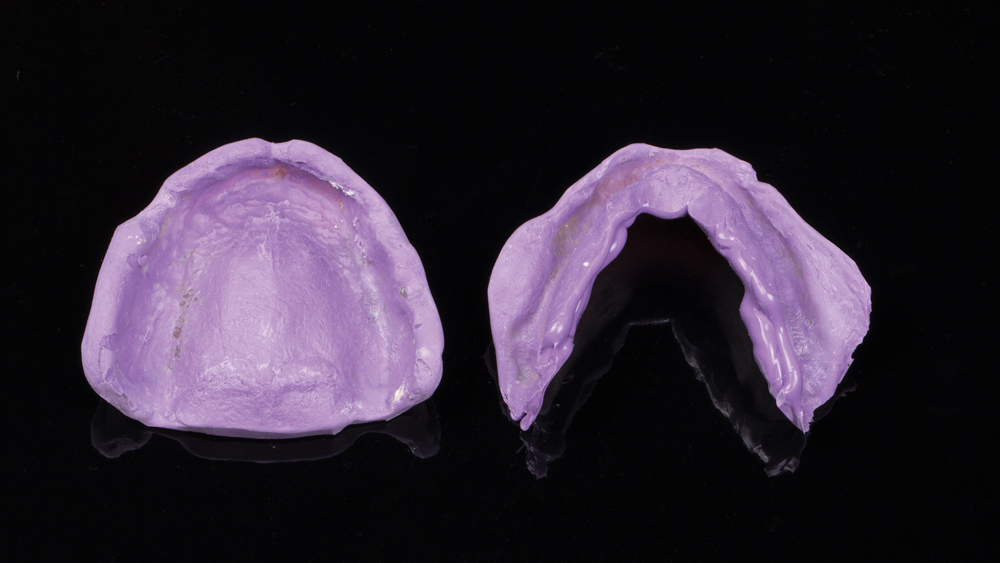
Figure 6: If the printed base does not meet the dentist’s fit requirements, it can be used as a custom impression tray for reimpression of the edentulous area.
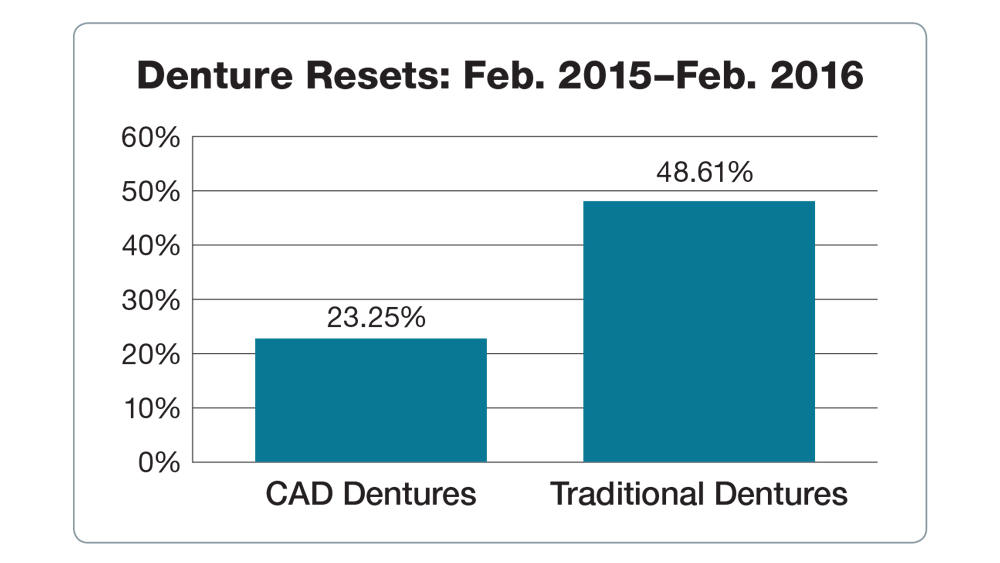
Figure 7: With this workflow in place, a far lower percentage of cases require a return to the lab for reset.
Using this technology, the final design of the appliance can be created after a single impression appointment. In the past, a design would not be proposed prior to the completion of a series of appointments, including the initial impressions of the edentulous space and a bite-block seating. The elimination of these steps is all possible thanks to the ever-present anatomical landmarks. Each digital denture proposal is created based on the position of the posterior border of the incisive papilla. Computer-controlled precision coupled with this significant landmark create a design that will most likely gain approval without any resets.
Each digital denture proposal is created based on the position of the posterior border of the incisive papilla. Computer-controlled precision coupled with this significant landmark create a design that will most likely gain approval without any resets.
After Try-In
The digital design of the baseplate and the hybrid technique of printing and traditional setting of denture teeth allows for a combination of computer-assured accuracy and the honed clinical accuracy of the doctor, who can check and adjust the teeth by hand if necessary.
Final processing begins immediately upon the return of the approved denture try-in. The accepted 3D-printed appliance is invested within a mold-creating material. Once this mold has firmed and the printed appliance is removed, denture teeth are seated in position across both arches. The mold is sealed and heated acrylic is pressed in at a consistent flow pressure. This establishes uniformity of both fill and porosity across the entire device. The device is removed from the mold, allowed to cool, and cleaned. The final result has outstanding esthetics and a computer-assured fit (Fig. 8).
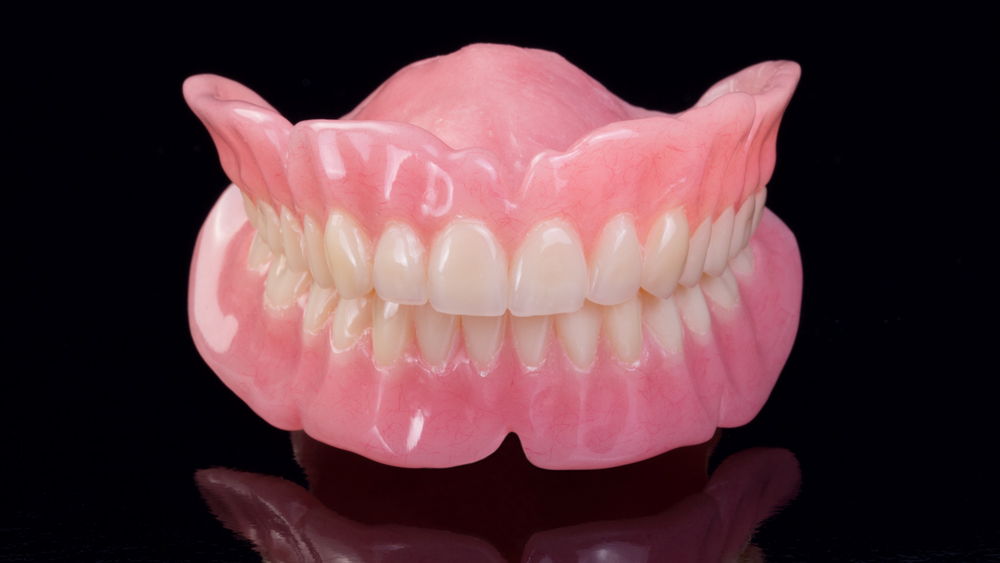
Figure 8: The finished CAD denture exhibits outstanding esthetics and fit.
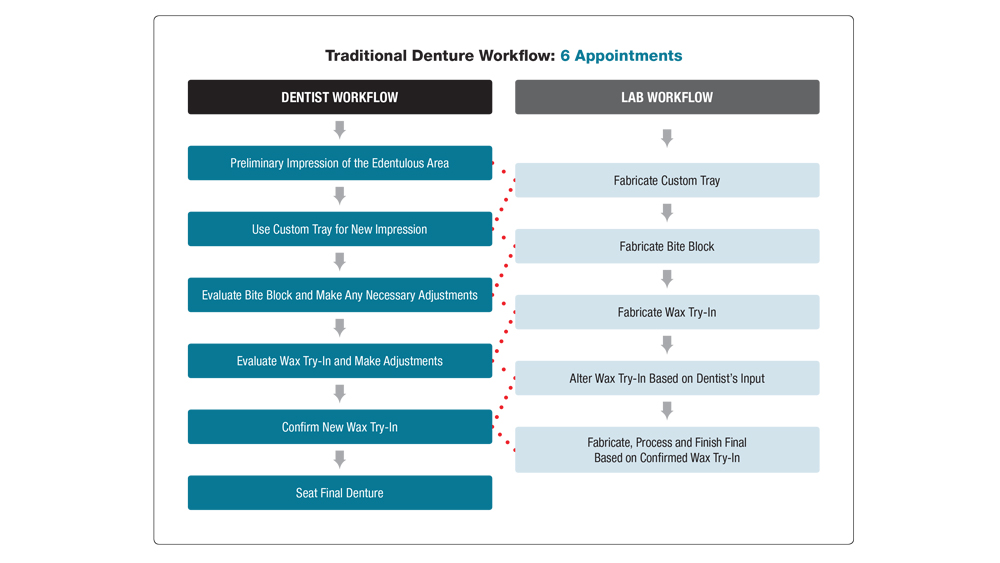
Figure 9: A typical workflow for traditional dentures requires six or more appointments due to the necessary try-in and reset appointments. Nearly 50 percent of these cases require a reset appointment.
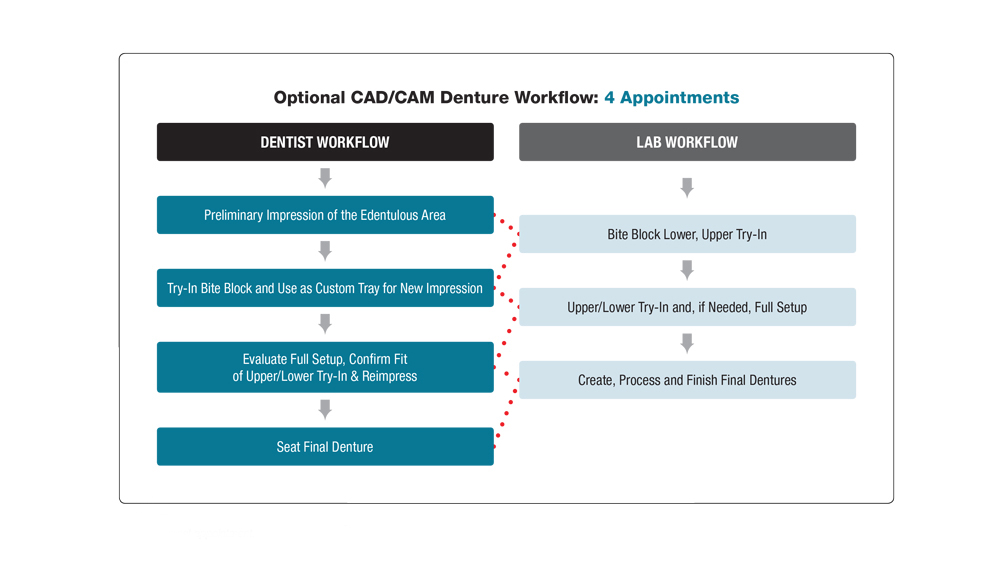
Figure 10: If a clinician does not deliver a bite registration and requires an extended workflow, it can take as many as five appointments. Less than 25 percent of cases require a reset appointment.
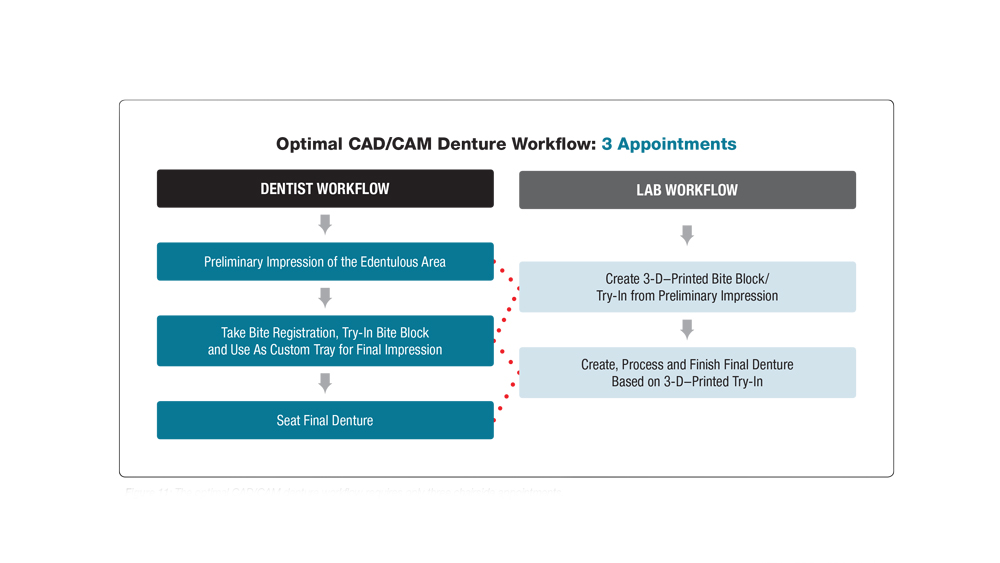
Figure 11: The optimal CAD/CAM denture workflow requires only three chairside appointments.
Advantages of CAD/CAM Dentures
The primary benefit of this workflow is the reduction of necessary appointments. Currently, more than 75 percent of cases are going straight from the try-in phase to the finished appliance, without a single reset appointment required. For the clinician, patient and laboratory, this equates to less time spent on the case. Whereas a traditional denture program might have the patient scheduled for six or more appointments, the optimized Simply Natural Digital Dentures™ workflow can accomplish a better result in as little as three appointments (Figs. 9–11). Beyond the reduced schedule, all denture designs are stored digitally by the lab. Broken or misplaced dentures can be replaced with just a phone call or an email, rather than a new series of impressions. With the help of Glidewell Laboratories, dentists across the United States can deliver a superior quality denture in far less time — a great selling point for dental practices.
Conclusion
We’re very proud to be able to deliver a service that offers reduced appointments, predictable costs, and a better definitive prosthesis. Digital technology has dramatically shifted the future of the Removables department at Glidewell Laboratories, and we hope that more clinicians will take advantage of the benefits this workflow provides.