Computed Tomography: Providing Consistency and Precision in Dental Restorations
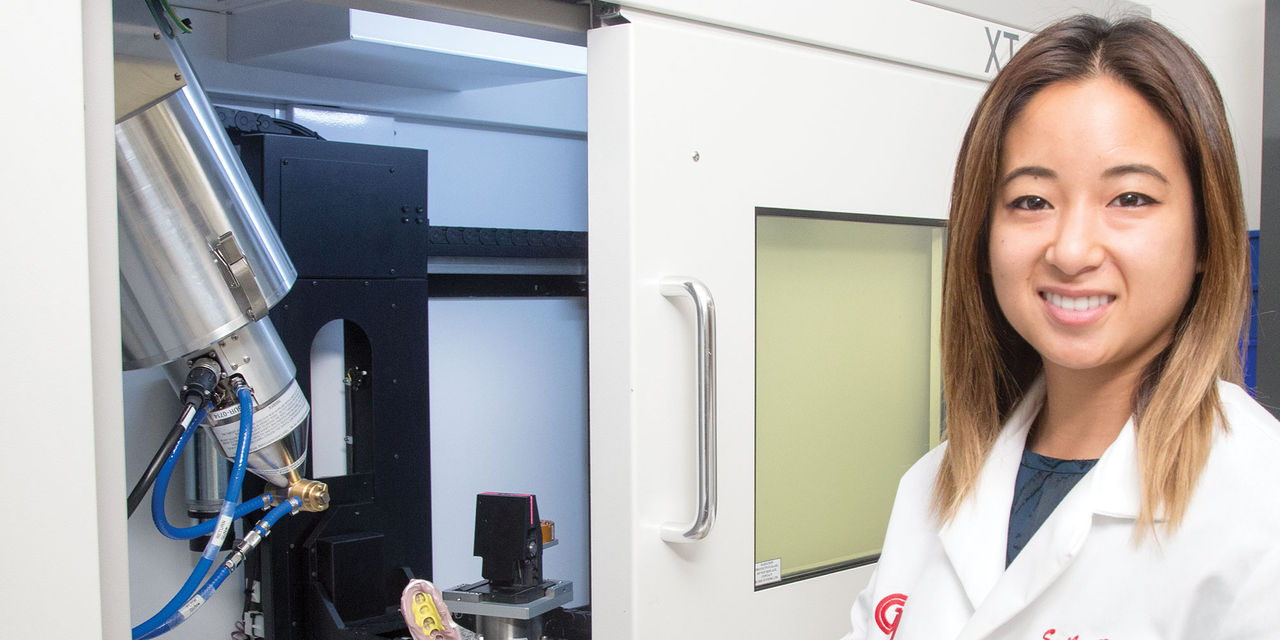
Dentists today are familiar with the advantages of utilizing 3D imaging to provide critical diagnostic information. Many, however, may be unacquainted with the numerous industrial uses of computed tomography (CT). Combining the penetrating power of X-rays with the data-processing power of the computer, CT scanning is an asset for high-tech industries that require absolute precision in their final products. Considering that this technology is used by organizations like NASA in the development of rockets and high-end aircraft, it is not surprising that it has found its way into Glidewell Laboratories for the fabrication of dental restorations. For the first time, Glidewell has begun micro-CT scanning dental impressions to produce crowns. This has the potential to improve patient treatment by providing better-fitting, more consistent restorations, while reducing the patient’s time between appointments.
When doctors send an impression to the modern lab, the impression must be digitized to begin the CAD/CAM fabrication process. The usual method of digitizing is for the lab to produce a stone model. The model is then optically scanned to generate an STL file, which the technician uses to digitally design the restoration (Figs. 1a–1d).
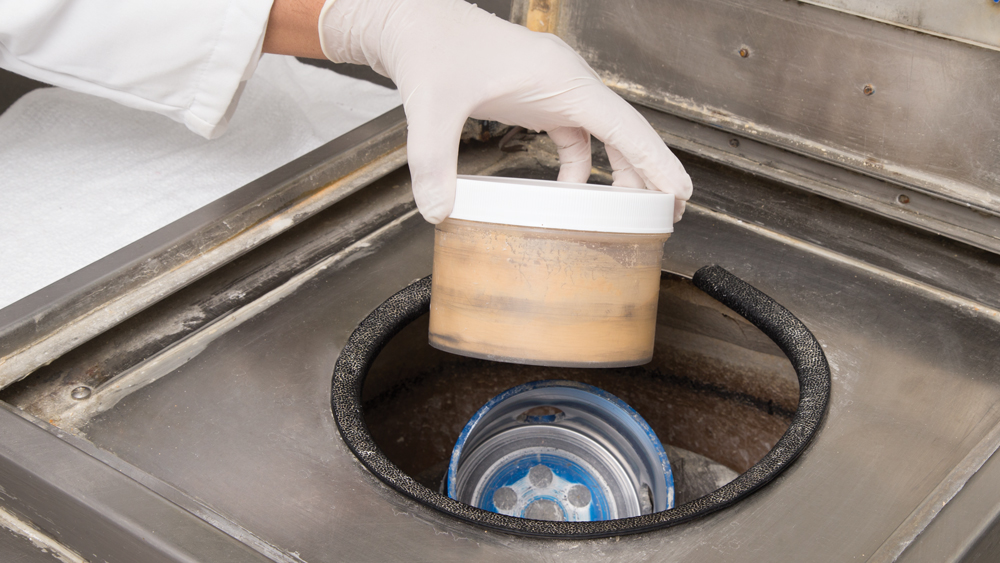
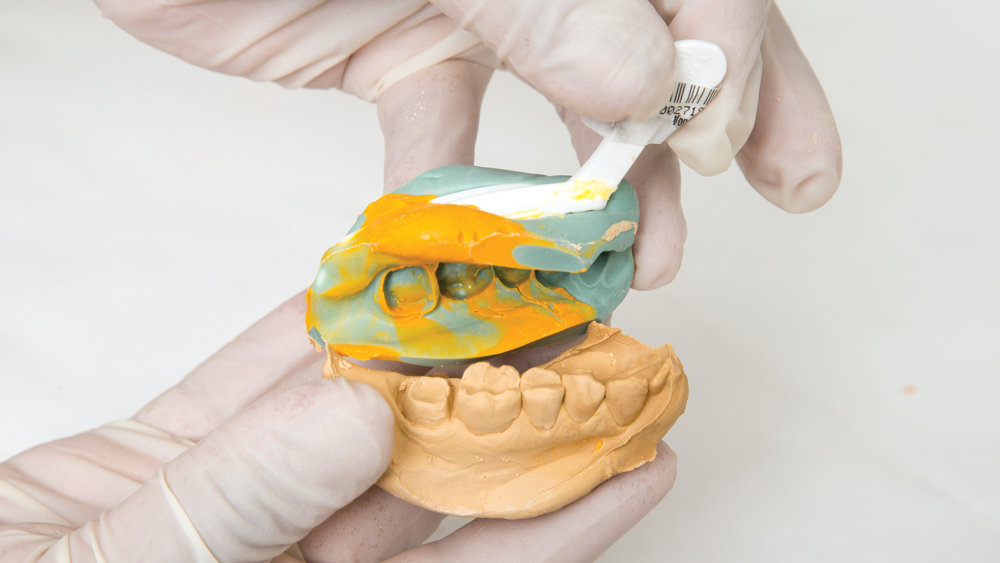
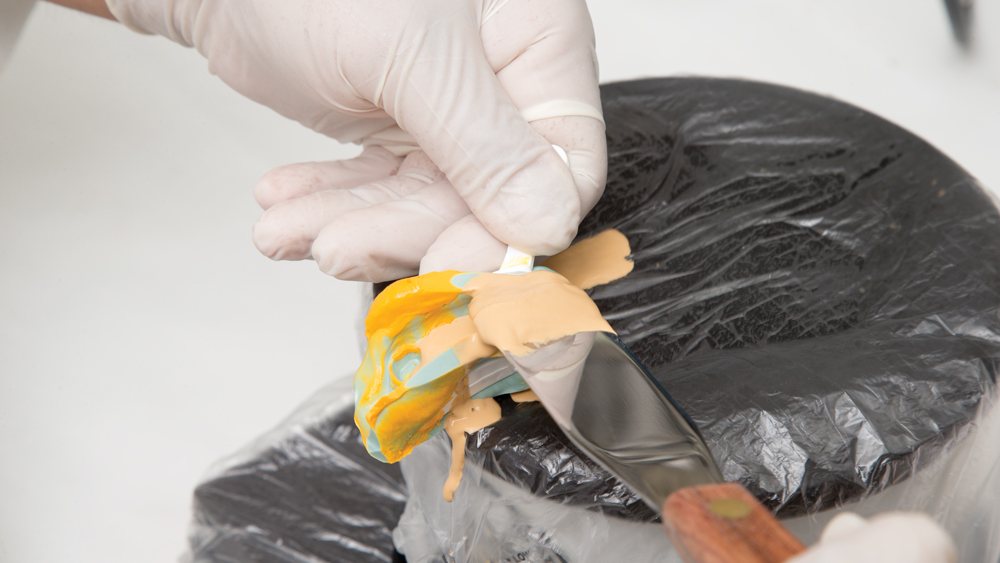
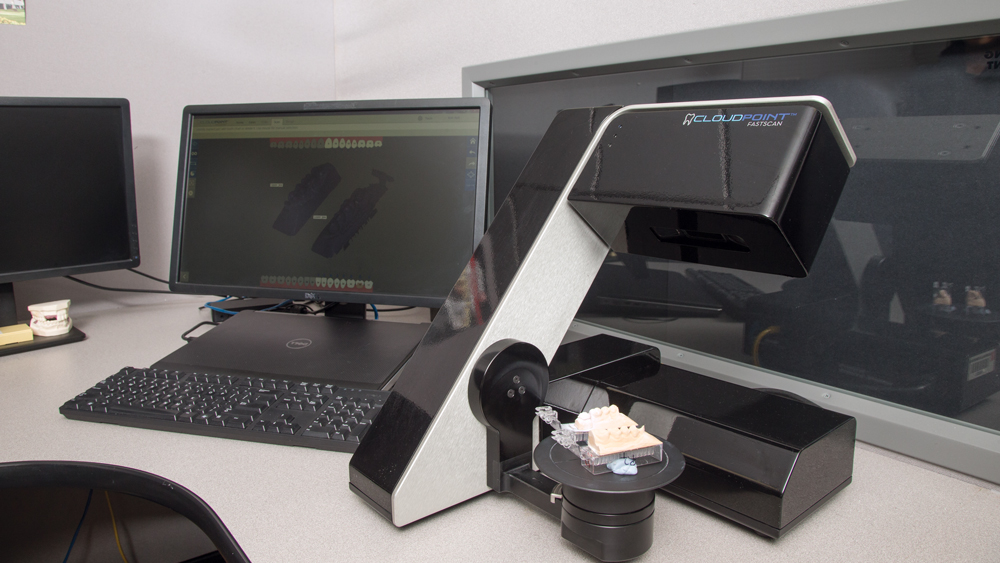
Figures 1a–1d: Traditionally, when the dental impression is submitted, the lab produces a stone model (1a–1c), which is scanned by an optical scanner to generate the digital STL file used to digitally design the restoration (1d).
Under perfect conditions, this can be a reliable method for producing the restoration. However, this technique has many variables that can result in errors, including expansion of stone during production, the possibility of an uneven stone mixture, and the potential presence of air bubbles in the mixture. Further, mistakes can occur in die-cutting and there is also the potential for breakage with stone models.
On the other hand, when the impression is scanned directly — without a model — using a micro-CT scanner, these environmental variables are avoided entirely. This leads to the highest level of accuracy and consistency every time. When the micro-CT is used to directly scan the impression, a digital STL file is created that can be manipulated on the computer, where the crown is designed on a virtual model and sent for milling (Figs. 2a–2d).
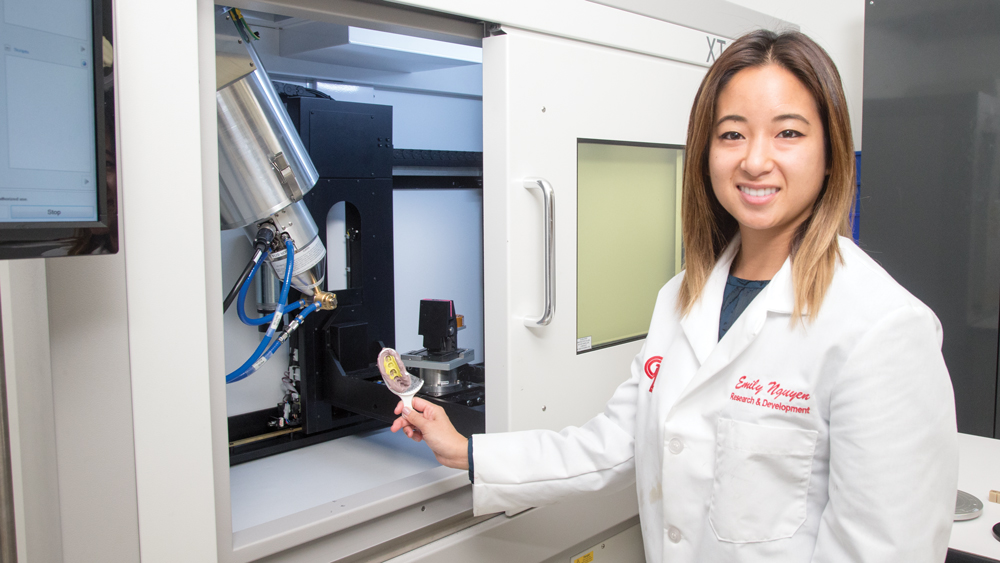
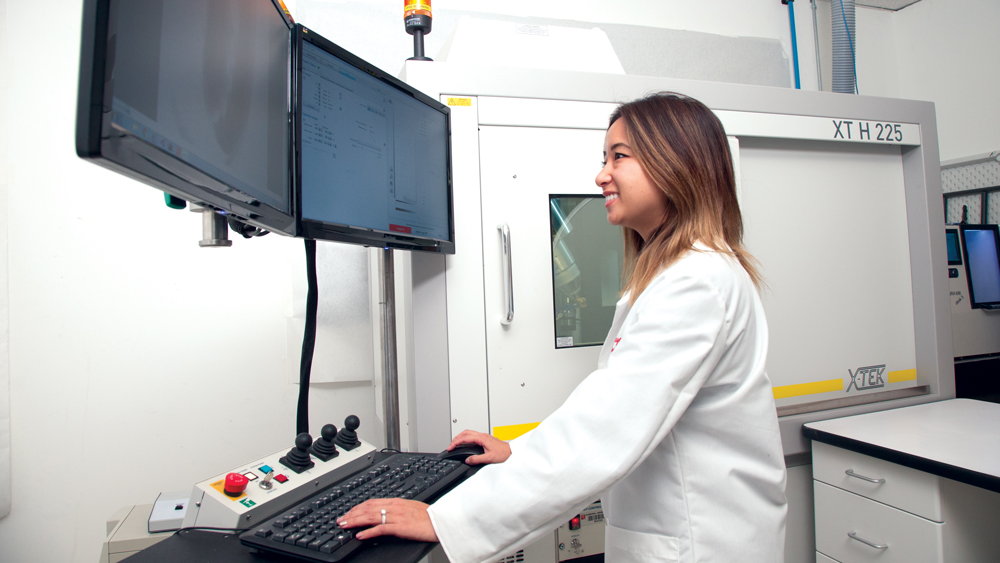
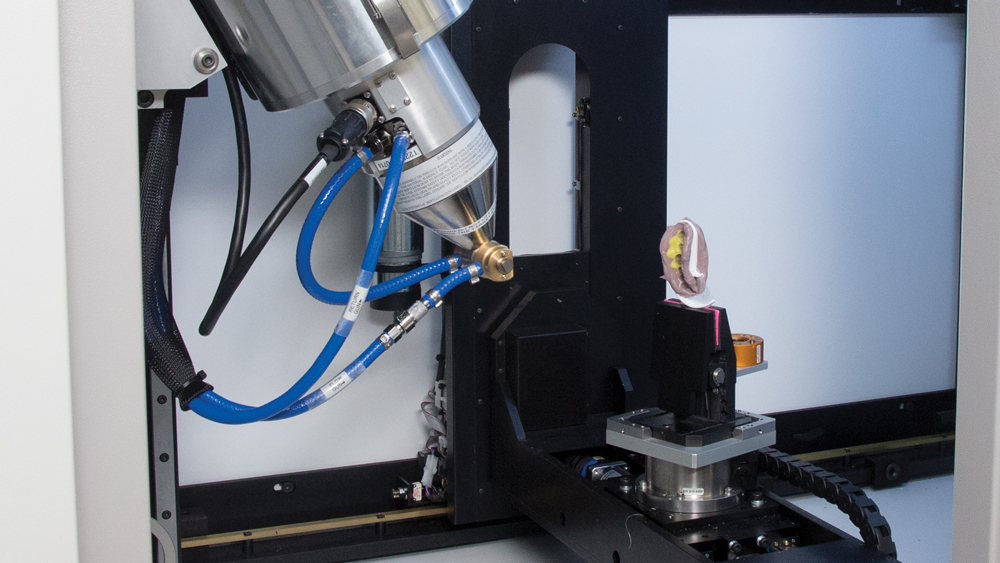
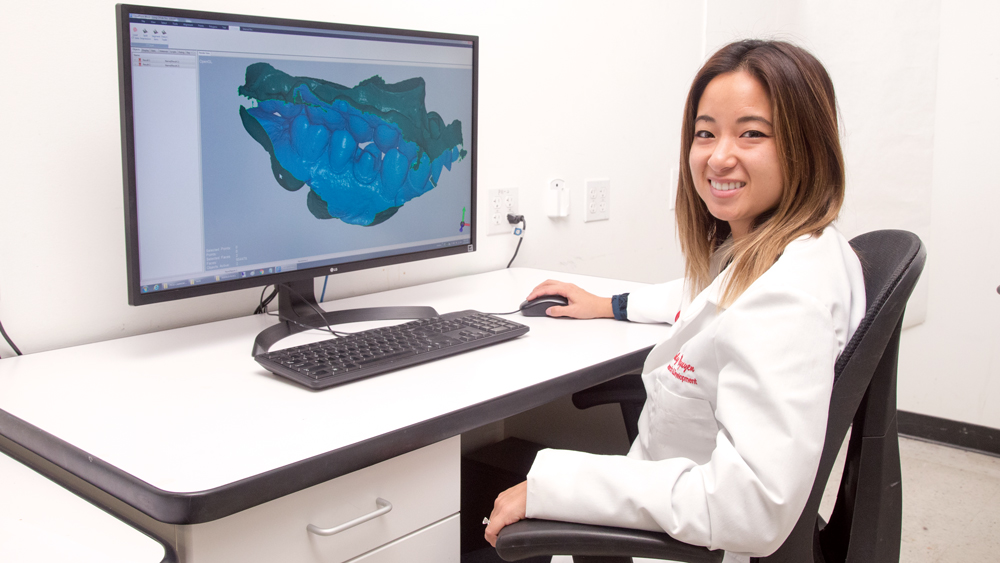
Figures 1a–1d: Traditionally, when the dental impression is submitted, the lab produces a stone model (1a–1c), which is scanned by an optical scanner to generate the digital STL file used to digitally design the restoration (1d).
COMPUTED TOMOGRAPHY: AT A GLANCE
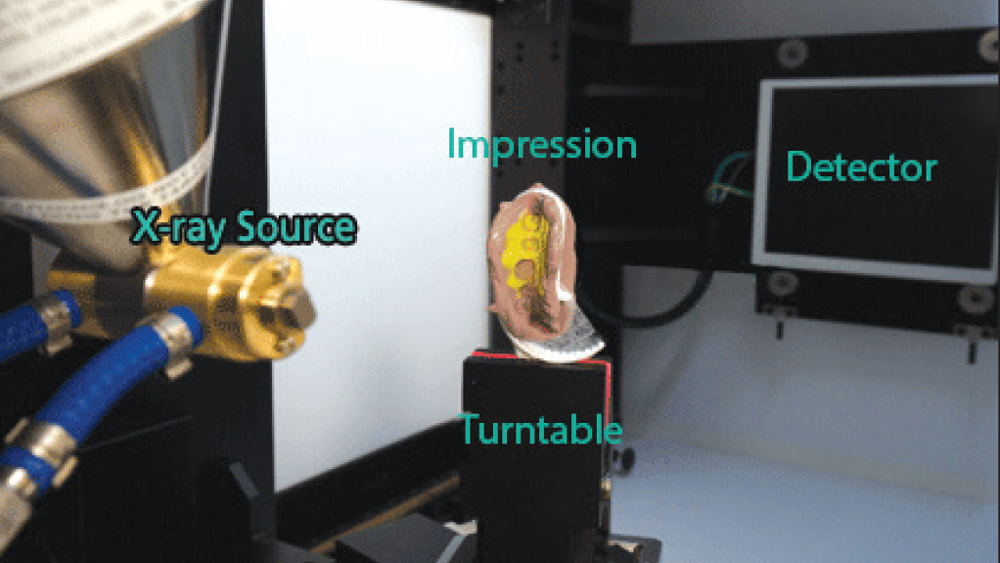
Computed tomography (CT) involves imaging an object from all directions using both X-rays and a computer to reconstruct the internal and external 3D structure of the object from the intensity values in the projected images.
The CT scan results in several advantages, including highly accurate dimensional measurements, stunning 3D imagery, and production precision far superior to conventional scanning methods. This is because optical scanning — the conventional method of digitizing models in dentistry — poses multiple challenges. For example, with long or angled preparations, problems arise in the optical scanner’s ability to capture data for undercuts present in the impression (Figs. 3a–3e). The optical scanner also has difficulty interpreting data for variations in color (Figs. 4a–4c).
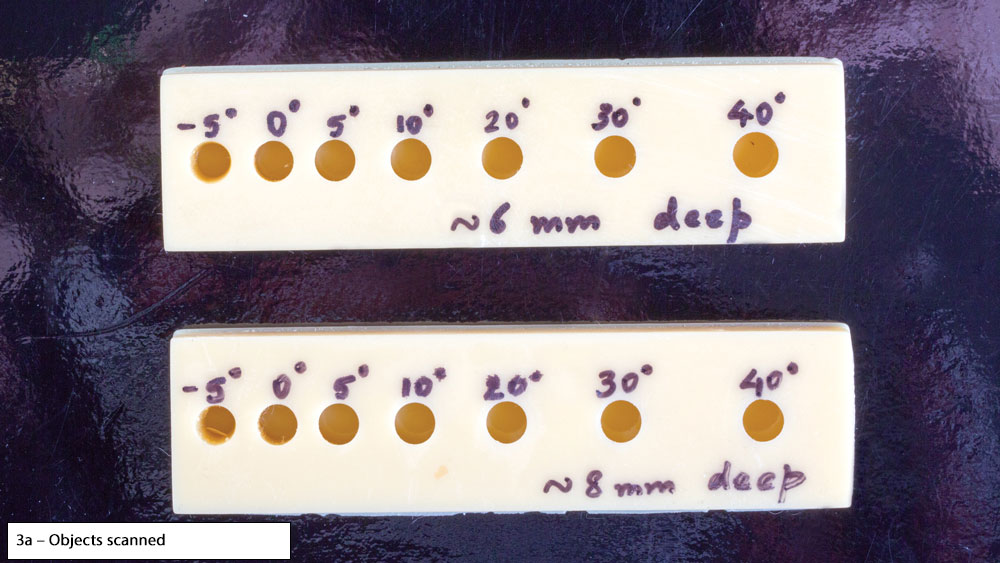
Figures 3a–3e: Shown, objects with varying degrees of taper (-5 to 40 degrees) (3a) were scanned using two methods. The micro-CT scan captures all structures and surface areas for the digital STL file, regardless of undercut angles and depth, resulting in a precise 3D digital model (3b, 3d). The optical scan results in missing and flawed data, and with increasing depth (6 mm to 8 mm) the image becomes more inaccurate (3c, 3e).
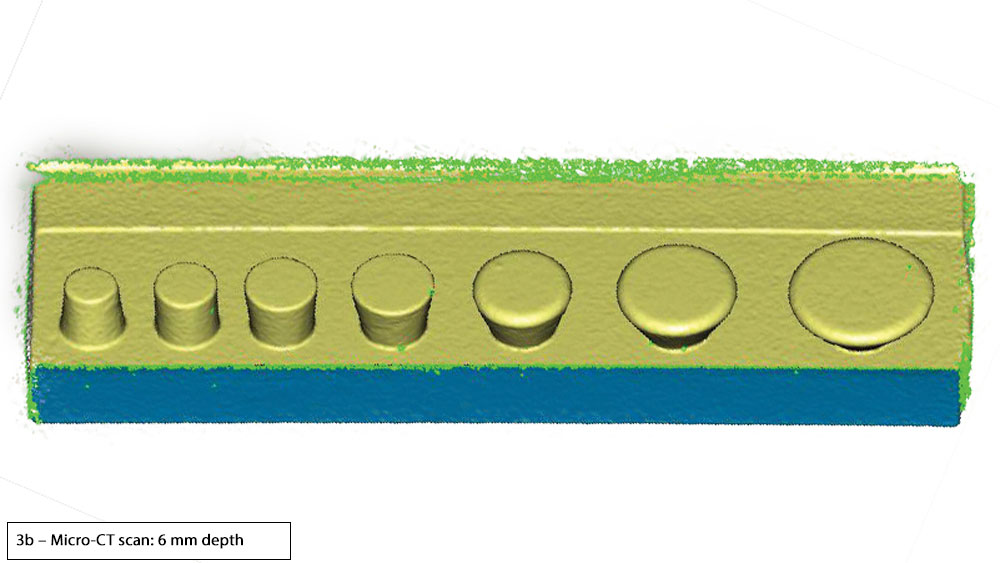
Figures 3a–3e: Shown, objects with varying degrees of taper (-5 to 40 degrees) (3a) were scanned using two methods. The micro-CT scan captures all structures and surface areas for the digital STL file, regardless of undercut angles and depth, resulting in a precise 3D digital model (3b, 3d). The optical scan results in missing and flawed data, and with increasing depth (6 mm to 8 mm) the image becomes more inaccurate (3c, 3e).
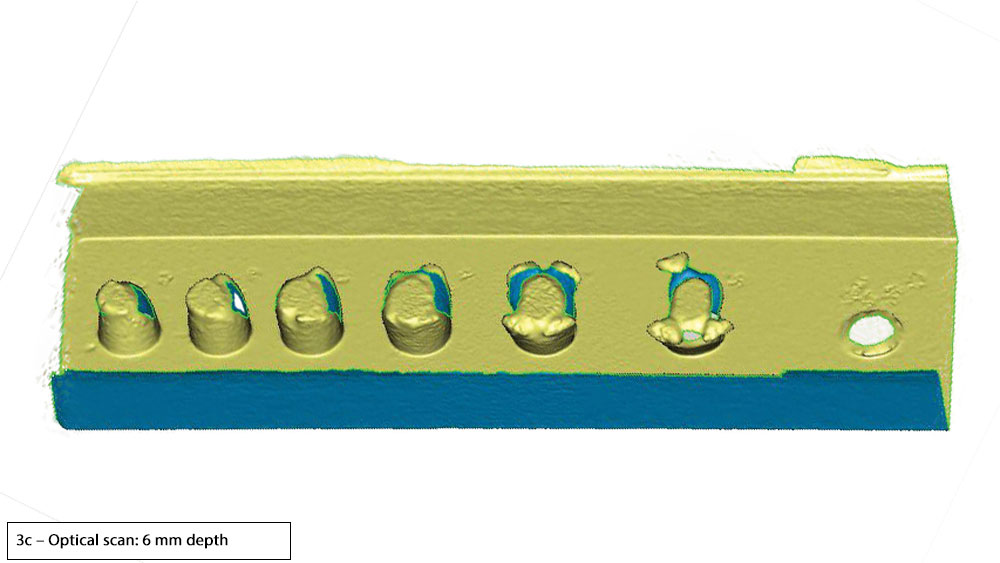
Figures 3a–3e: Shown, objects with varying degrees of taper (-5 to 40 degrees) (3a) were scanned using two methods. The micro-CT scan captures all structures and surface areas for the digital STL file, regardless of undercut angles and depth, resulting in a precise 3D digital model (3b, 3d). The optical scan results in missing and flawed data, and with increasing depth (6 mm to 8 mm) the image becomes more inaccurate (3c, 3e).
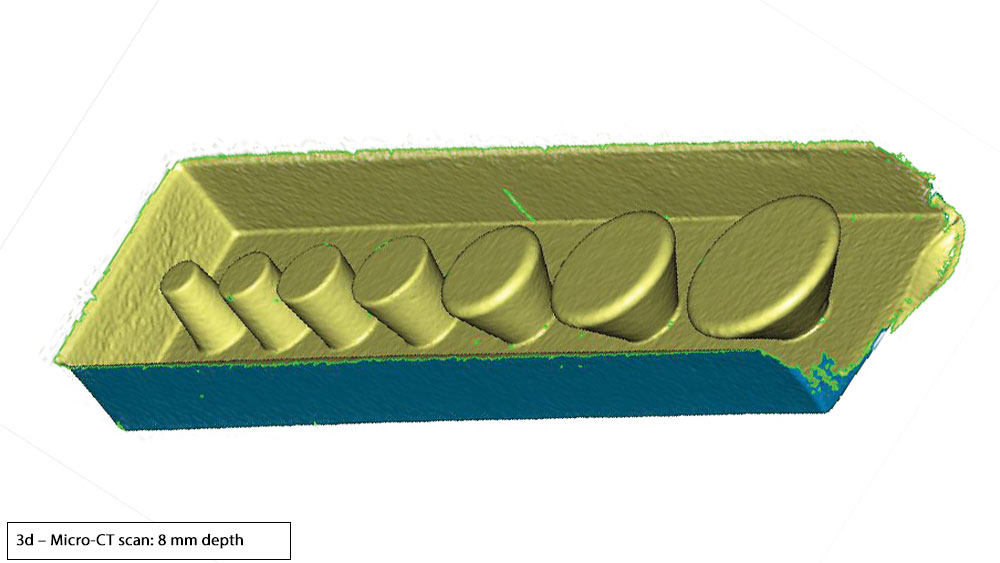
Figures 3a–3e: Shown, objects with varying degrees of taper (-5 to 40 degrees) (3a) were scanned using two methods. The micro-CT scan captures all structures and surface areas for the digital STL file, regardless of undercut angles and depth, resulting in a precise 3D digital model (3b, 3d). The optical scan results in missing and flawed data, and with increasing depth (6 mm to 8 mm) the image becomes more inaccurate (3c, 3e).
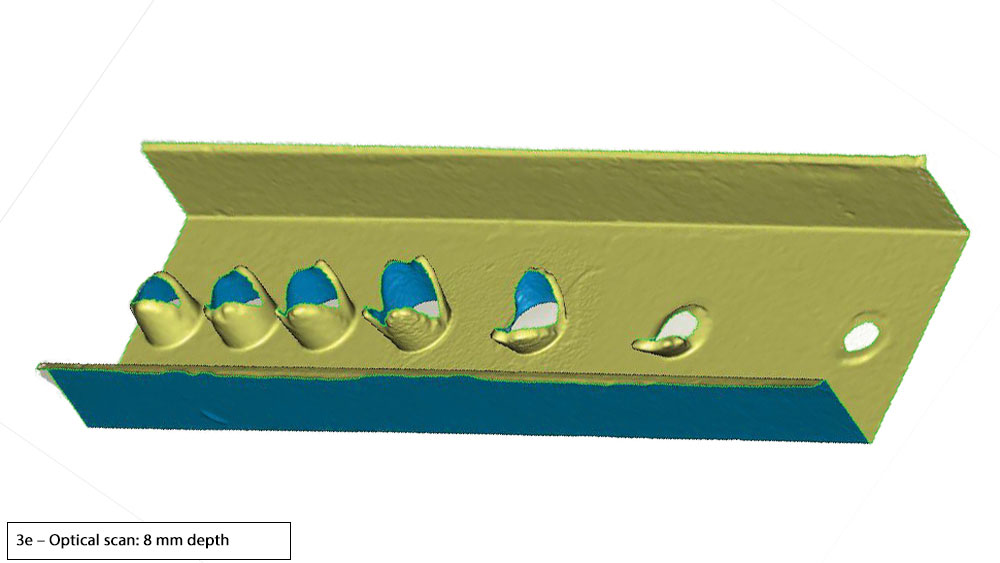
Figures 3a–3e: Shown, objects with varying degrees of taper (-5 to 40 degrees) (3a) were scanned using two methods. The micro-CT scan captures all structures and surface areas for the digital STL file, regardless of undercut angles and depth, resulting in a precise 3D digital model (3b, 3d). The optical scan results in missing and flawed data, and with increasing depth (6 mm to 8 mm) the image becomes more inaccurate (3c, 3e).
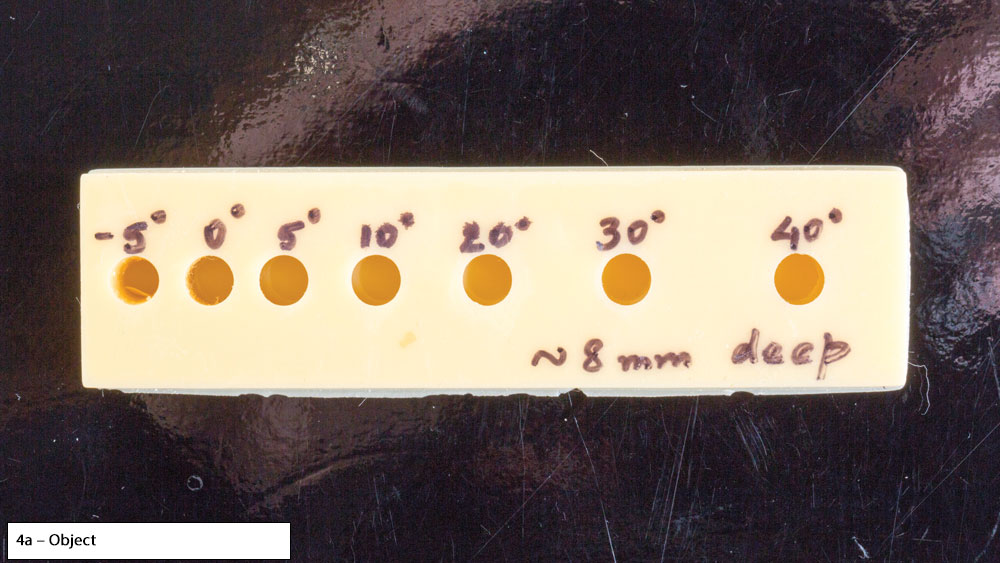
Figures 4a–4c: A micro-CT scan is not confused by changes in color (4b), whereas an optical scan is prone to being confused by changes in color and will often interpret such differences as a change in texture (4c), as shown here.
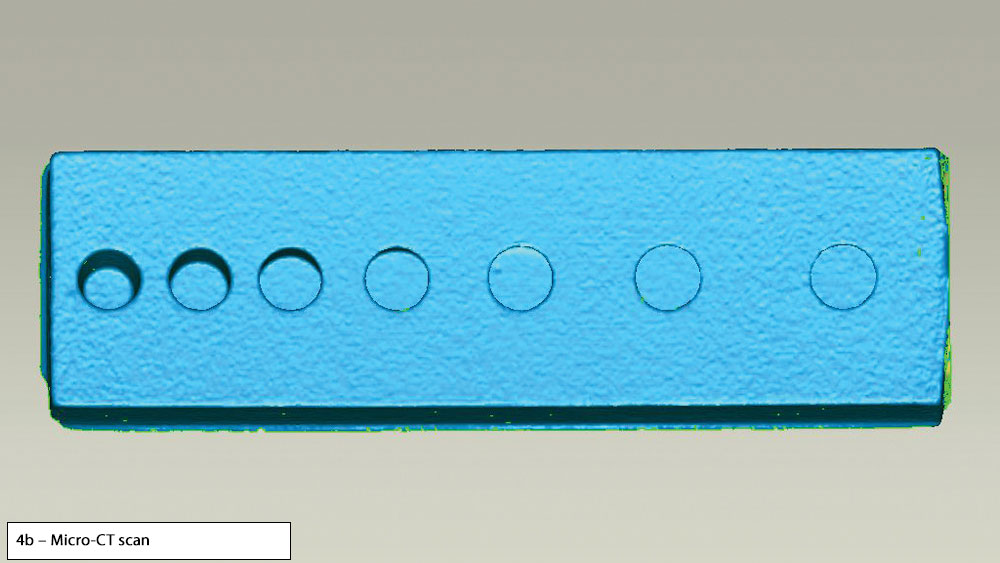
Figures 4a–4c: A micro-CT scan is not confused by changes in color (4b), whereas an optical scan is prone to being confused by changes in color and will often interpret such differences as a change in texture (4c), as shown here.
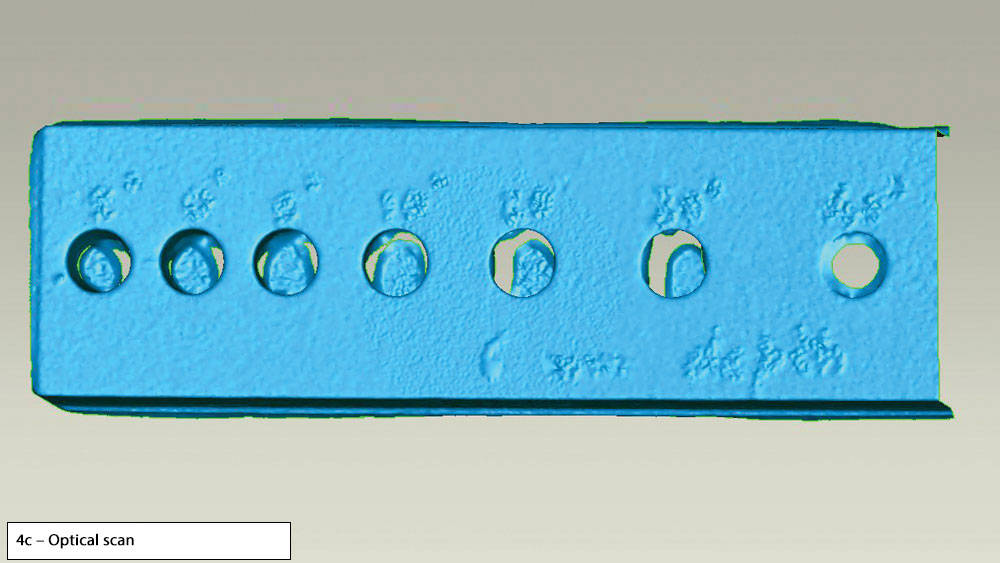
Figures 4a–4c: A micro-CT scan is not confused by changes in color (4b), whereas an optical scan is prone to being confused by changes in color and will often interpret such differences as a change in texture (4c), as shown here.
Another significant benefit of CT scanning of dental impressions is the speed of the scanning process. Most single-unit impressions can be scanned in about 30 seconds, and long-span impressions are scanned in 90 seconds. Conventional methods involving stone mixing, pouring, setting and die-trimming processes take an average of 40 minutes. Thus, immediate micro-CT scanning at the lab will result in faster turnaround times for restorations. Ultimately, the patient will benefit from the clinical advantages of CT scanning by receiving a precisely milled restoration that exhibits excellent margins, fit, contacts, contours and occlusion — while also completing treatment more quickly.
CONCLUSION
For the first time, at Glidewell Laboratories, the same technology used to make rockets and high-end aircraft is also being used in the fabrication of dental restorations. Recognizing the limitations of optical scanning of stone models and the benefits of a 100 percent digital process, Glidewell Laboratories is applying the advanced imaging and scanning capabilities of micro-CT technology for a faster, more accurate means of crown fabrication — a goal that allows doctors to provide their patients with leading-edge restorative treatment.
Adopting equipment that was once available only to high-tech industries, the advanced laboratory is pushing the boundaries of dental innovation and producing the highest level of accuracy and consistency available for restorative treatment. Micro-CT scanning avoids the challenges of environmental variables that can lead to errors, and because of this groundbreaking new workflow, doctors can gain all the benefits of going fully digital without the investment or learning curve that might otherwise be required when implementing digital technology in the dental office.