CAD/CAM Technology
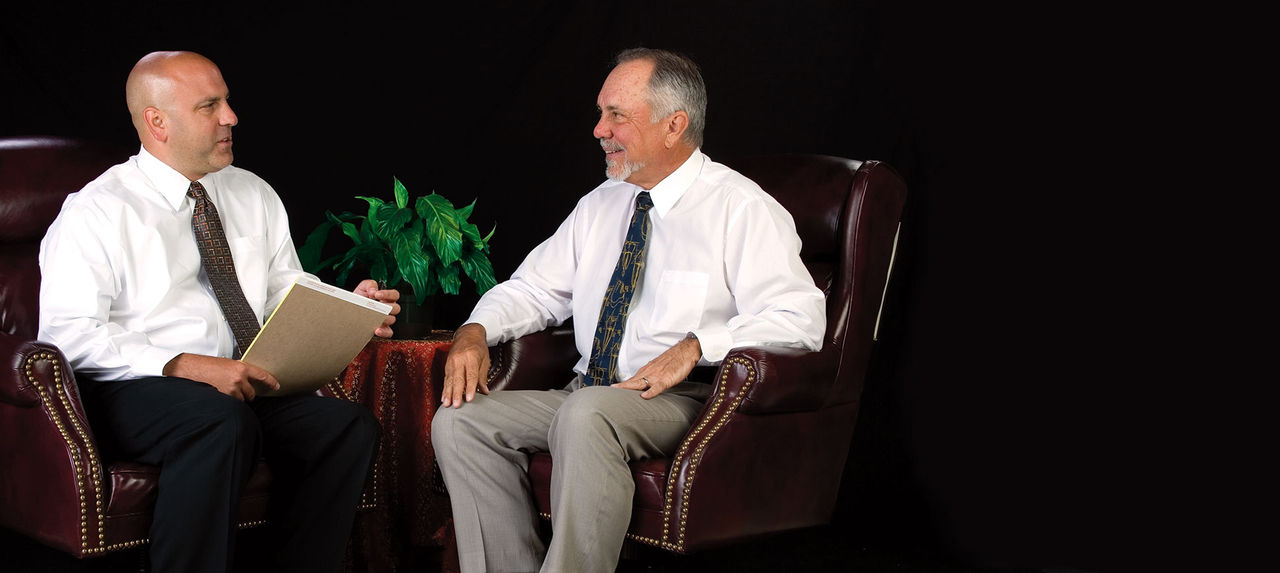
Dr. Michael DiTolla recently had the chance to sit down with Jim Glidewell, CEO of Glidewell Laboratories. Jim shares his thoughts on the evolution of CAD/CAM technology and the effect of this evolution on restorative and cosmetic dentistry. Later in the interview, Jim provides an historical analysis of CAD/CAM production at Glidewell and his vision for how it will impact laboratory case fabrication in the future.
Dr. Michael DiTolla: Good afternoon, Jim. I wanted to ask you first about CAD/CAM. What was your first exposure to it in the dental industry, and what were your first thoughts on it at that time?
Jim Glidewell: The first thing I encountered were crowns that were manufactured by Francois Duret back in the middle ’70s when he and Jack Preston were at USC. It was in the mid-’70s that they were exposing people to this technology. The technology at that time, I think, had been around about 15–20 years. I think at that point in time there were just too many problems involved with scanning. The manufacturing of the part wasn’t as difficult as getting the data into the computer to manufacture the part. So my first experience was between 1975–1978.
MD: When you saw the technology, did it seem like something that you thought would one day fit into the dental business?
JG: No, I absolutely felt the opposite. I felt that there was no way you were ever going to be able to duplicate what we do as technicians with a machine and have it be cost-effective. Back then, I just didn’t see far enough ahead to see that it would ever be cost-effective. Today, I feel completely different about it. We don’t have to have the massive computers that were required 30 years ago. Today, we have everything at a low cost, from software to hardware. All of it seems to be very, very inexpensive.
MD: I don’t think in the early days that they thought those types of CAD/CAM systems could mass-produce restorations, necessarily. The rise of the PC from something that took up an entire room to today’s desktop PC that can do what that computer used to do in half the time really changed things.
JG: I think it is probably the number-crunching ability of computers that has changed and the money attached to that ability. In those days, a mini-computer like a Burroughs was probably a $200,000–300,000 investment to run a machine. Then there was software to be written, which was very pricey in those days. Today, there’s an affordable computer for every household. In those days, there was not.
MD: I believe Procera® (Nobel Biocare; Yorba Linda, Calif.) was the first milled restoration that you began doing here at the laboratory. Were you still skeptical at that point that these types of crowns would ever replace handmade restorations?
JG: I think Procera is probably the very first thing we ever outsourced. I didn’t look favorably upon outsourcing because we were losing control of the product. We found out that the outsourced quality was equal to ours, after just a few units were made. It made us very comfortable with outsourcing. Initially, the thought was that it wouldn’t be equal to what we do here, from a pride standpoint, probably. We thought nobody could do it as well as we do it here. In reality, the results were just as good or better than what we were producing with alumina at the time.
MD: Now your laboratory has many CAD/CAM machines, including multiple brands of CAD/CAM, one of which is your own. How do you feel about the state of CAD/CAM today as opposed to 20 years ago?
JG: I think we’re very, very close to CAD/CAM as a solution to the “human input” problem that we have. Dental technicians, invariably, put their subjective judgments into every crown, whereas a CAD/CAM system only interprets its information digitally and repeats it digitally every time. It has a perfect recall, if you will. The technicians produce good crowns one day, then maybe they didn’t feel good the second day — so each technician’s work can even look somewhat different from day to day. Then, across the spectrum of technicians that we have here, the up-and-down quality variations are much more noticeable. With a CAD/CAM system, it tends to reproduce the same quality again and again.
MD: And you see the words “ceramic artistry” used to represent what a ceramist can do. Some people appreciate that art, and some people look at it and can’t stand it. It does vary from time to time, but it sounds like you are saying that the computer will base it on the ideal anatomy for a certain tooth and the other parameters that influence the final three-dimensional form.
JG: My whole career has been based upon the theory that there really is no artistry in dental technology whatsoever. If we are to use our artistic ability to change the contours, where do we place them? How can we make it better than what is already in the mouth? All we can do is make it different, but we can’t make it better than what already exists, because that mouth has been honed by genetics for millions of years. In my background, I’ve also thought about teeth being a three-dimensional mathematic product. All of a sudden, CAD/CAM comes along and meets exactly where I’ve been trying to go my whole career. I wanted to find a way to take all the subjective judgment out of making a tooth, and create it strictly objectively or make it objectively with a machine to have it produced objectively every time. We could almost eliminate the Quality Control station if the machine will make that part — if the software is done right, if all the collective knowledge went into that software that designed the crown and it was done correctly, we should not have varying quality at all.
Varying quality is what drives most dentists away because they seem to get a different product from the laboratory they use every time, whether it’s a small lab or a large lab. We all fight for the same thing — consistency of product. Also, as we’ve found out from a digital standpoint, we can make the occlusal clearance tolerances and contact tolerances much, much closer than the human hand can. For me, that’s been the biggest single breakthrough I’ve seen — the ability to make the contacts perfect without having a plus contact on one side or a minus contact on the other side. Contact adjustments are the most difficult thing to do chairside. Occlusal adjustments are fairly easy, but contact adjustments are hard. With these CAD/CAM systems, we can make contacts with precise accuracy.
MD: As a dentist, it makes me feel confident that we somehow now are able to scientifically address the contact issue. Before, it was scraping the adjacent tooth just to make sure the contact wouldn’t be open. Dentists would use floss to check it, technicians would use articulating paper. We weren’t even using the same standard to check it. It’s a nice feeling to know that it’s getting more scientific, as opposed to all of these homespun techniques that have evolved over the years. One of the more frustrating things chairside is tight contacts. Yes, they can be adjusted, but it’s very easy to open a contact and that contact will not close itself. If you accidentally take a crown slightly out of occlusion, most dentists will cement that, knowing that supereruption will put it back into occlusion. But that open contact is immediately going back to the lab, and that is frustrating.
JG: I think that when the technicians adjust the contacts, they leave them tight. They’ve already scraped the adjacent teeth. When the dentist puts the crown in the mouth, he first adjusts the distal, then he adjusts the mesial, then he goes maybe back to the distal if he has the time, or the concentrated effort to be able to do that in a routine. Invariably, at some point he’s going to adjust the wrong contact at the very end and have an open contact. It’s just part of the system. So I can’t believe what a boon this is for cementations! All of a sudden, you’ll be able to pull a crown out of the box and walk out of the room knowing you’re mixing the cement.
MD: Of course that assumes that your assistant had proper contacts on the temporary, something many dentists seem to forget about. But I do think there is an ideal contact most dentists could agree on.
JG: Remember I mentioned one time that most dentists are looking for a tight fit and they check it with a piece of dental floss. The dental floss, probably, is 75–100 microns in thickness. So even a 15-micron open contact will give you a very solid click. You’ll consider that a closed contact at 15 microns of opening. And for all intents and purposes, it really is. So, if we can give you a contact that’s 15 microns open mesial and distal, the crown is going to fall in place and you’ve still got acceptable contacts.
MD: There is at least that much physiological movement of teeth on a daily basis. You’re right, that would be clinically acceptable.
JG: And we don’t have food particles that are smaller than 15 microns that would cause problems. So I really think that we are on the verge of a massive change of quality, more than anything else. I think that scanning and digital manufacturing are going to improve the quality.
MD: As far as I know, Glidewell is the only laboratory that has a digital manufacturing center. When did you start that, and what have you seen from it so far?
JG: We have started our digital manufacturing in earnest. In fact, we’ve been doing digital manufacturing in one form or another for five years. The involvement with Cercon® (DENTSPLY Ceramco; York, Pa.) and the Wol-Ceram® (Wolz Dental-Technik GmbH; Ludwigshafen, Germany) systems probably began about five years ago. Then, about 18 months ago, we hired an industry respected 3D specialist to help put the rest of our systems together — to marry the software, the hardware and the application into one workable system. So, with the addition of Mervyn Rudgley from 3D Systems, we started in earnest. We brought in a software engineer and gave the digital manufacturing team a really big research budget — probably up to $1 million in the first year. We decided we were going to spend it on all the equipment and systems needed. We have had breakthrough after breakthrough. We’ve been very, very fast because our specialist has not had to go to a committee looking for approval. We’re not a publicly owned corporation where we’re having to drain profits. It’s just that our commitment to doing this has distinguished us, and we’ve grown very, very rapidly.
MD: And, for the dentists who aren’t familiar or haven’t read any articles about digital manufacturing, can you explain what it means — for example, how the scanning takes place and how parts are printed?
JG: By and large, the process starts with a model supplied by the dentist, created exactly the way things have been created traditionally. We take that model, scan it and let the system calculate where the margins are, while creating a complete reproduction of prep area, the prepped tooth. We also have the ability to scan the opposing in an articulated acquired centric mode. From that point, we go to a CAD system, which is Computer-Aided Design, and the CAD system software allows us to design, manipulate with many tools and to fabricate a digital crown. We transfer that digital crown design from the software to another system, the CAM operation, which takes our information and reduces it to machine tool path instructions, and we can either machine a part from this software or we can go to a printer. It’s a process whereby we print with a wax-like material an exact replica of the restoration we designed using the CAD system. We can do that down to a 15-micron accuracy, which is about a quarter of the thickness of a human hair. With that printed part, we can cast it into metal or we can press ceramic material into it. Also, from the CAM, we are able to machine mill out of zirconia or metals a coping or a full-contour crown without even using the wax process. We can actually machine out a gold part if we want to as well.
MD: So this new system is totally unlike the Procera system where you would scan the die, then the coping is made for you off-site and then returned to you to stack the porcelain on it by hand. With the CAD/CAM system you’re describing now, the coping is manufactured digitally from the scan of the master die, and then the actual contours — the shell, if you will — is also digitally manufactured and then the two parts are assembled.
JG: That’s correct.
MD: To me as a dentist, the shell part, the outer contours of the crown, are more important to me than the other part — than the coping. My issue with restorations over the years has been with the anatomy and esthetics — not necessarily with the fit itself. That is why I think digital manufacturing is such a big step forward.
JG: Throughout the industry, that’s why making the coping was a very safe thing to do. It doesn’t have contacts, it doesn’t have occlusion, it doesn’t have morphology, it doesn’t have shape. Most all the people involved in the CAD/CAM industry looked to designing the coping only. Procera is a coping, Cercon is a coping, Lava™ (3M™ ESPE™; St. Paul, Minn.) and Prismatik Clinical Zirconia™, those are all just copings. The dentist shouldn’t get up and make a big deal out of these things. But what we’ve done here is, we’ve advanced on to the process of actually making the superstructure that goes on top of that — we’ve done that digitally also.
MD: And this one day will include anterior teeth as well?
JG: Yes, absolutely. We should be able to have a complete host of different shapes and mold sizes, much like you see in a denture mold chart. You would choose the anterior restorations you want, and we could absolutely duplicate that with this process we’re referring to. Also, the same thing with morphology. You choose one of your idols and we can take that type of a gnathological occlusal arrangement, print that out and have that cast into a ceramic part with absolute fidelity — like we say, within 15-micron tolerances throughout the whole mouth. It’s done very easily compared to the laborious way of stacking porcelain up or stacking up and carving it back, and having to deal with a 14% shrinkage of porcelain.
MD: Which is why full-mouth cases scare a lot of dentists because of having to deal with the occlusion. Imagine having a computer take care of all that for you. And imagine a patient being able to look at a book of teeth arrangements and smiles, rather than having a ceramist, by hand — trying to match that, you’d actually be able to print that pattern right in the computer.
JG: Yeah. I think that would not only save time and money, but you take the guesswork out. You get to decide with the patient and have the patient commit to the teeth that they want. Later on, they have exactly the smile they want. The patient isn’t going to get a huge shock.
MD: If you had to look 10 years into the future, what percent of crowns — PFM and All-Ceramic — do you think will be digitally manufactured?
JG: I think over a 10-year period of time we’ll see a phasing out of traditional porcelain-stacking technology into digital manufacturing. I would be surprised if in 10 years less than 90% of all crowns are fabricated through digital means. Only 10%, perhaps the “art” cases, or maybe veneering situations will not be fabricated by digital manufacturing.
I think over a 10-year period of time we’ll see a phasing out of traditional porcelain-stacking technology into digital manufacturing. I would be surprised if in 10 years less than 90% of all crowns are fabricated through digital means.
MD: How about single-unit anterior teeth, for example?
JG: Perhaps. Although with our technology we can scan it today and we can flip the crown over to mirror image the other side, the morphology becomes very accurate because we are able to use the anatomy of the adjacent tooth. I’ve always maintained that if you have the right morphology, the shade seems to match. If the morphology is off just a little bit, everybody thinks it’s the shade. If you just match the morphology, 90% of the job is done.
MD: If you had to look at the eight criteria that make a restoration match a natural tooth, shade would probably be No. 4 on the list of importance.
JG: I would say so.
MD: After contour, shape, size…
JG: At our company, we find that most of the adjustments we have to do, do not involve shade. They’re mostly poor fits, bad impressions or whatever. Shade is usually down the list.
MD: What do you think, nationwide, digital manufacturing is going to do to the average price a dentist pays for a crown? Do you think these crowns, being superior, are they going to be more expensive, less expensive?
JG: It has the potential to decrease laboratory prices. I think anything that gets mechanized and gets away from human labor tends to become a commodity, much like computer chips have. You’re going to see a dramatic drop in the laboratory cost over the next 5–10 years.
MD: How long do you think it will be before the other labs in the country, starting with the large ones, get involved with this type of technology?
JG: I think the information age is upon us, and they’re already seeing the light and they know they’ve got three to four years before they’re going to be left out in the cold. They’ll all be buying systems. And the systems are going to be fairly inexpensive. For under $200,000, a laboratory can set up a 3D printing system and a zirconia design and milling system. I don’t see it as expensive. Lava is a little on the pricey side. There’s a lot of great research behind it. But at $230,000 to set up a lab system, that’s a little on the high side. There’s going to be a lot of people coming under that price.
MD: Do you see any connection — direct or indirect — between digital manufacturing and offshore laboratories?
JG: Offshore laboratories — I think the reason people go there is that they’re driven by low labor costs. When we look at the cost of manufacturing offshore versus the U.S., even though our labor is much, much higher here, the offshore labs lose a little in shipping costs. The time lapse is always about an extra week in turnaround time. Remember, we own two offshore laboratories, so we’re well aware of what these costs really are. I’ve always felt that if you had a free crown, an absolutely free crown, just to get the impression, pour the model, log it in, put it in a box and send it back out, you probably needed about $50 per crown just to accomplish that — if there was NO labor involved in the crown, if it was FREE. There’s a transaction cost of having a box, receiving it, handling it, sending it out. And then you’ve got your rent and overhead and all that. If you had free labor, you’d literally have to get $50 for a crown. People who sell it for underneath that, bless them! But I think they’re slowly going out of business.
MD: And dentists are familiar with that, too, because there’s a cost for having a patient come in and sit down, before you even do anything!
JG: Absolutely.
MD: Even if you did nothing, CRA estimates that cost at $12–18 just to seat the patient in the chair.
JG: Absolutely the same thing. That’s the transaction cost. There might be a $30 difference between an offshore crown and a domestic crown in terms of savings. You might be paying $30 less for an offshore crown. Of course, some labs are quite a bit higher than we are — it might be in the $150–200 range. The average laboratory charges maybe $100 for a crown, and I think that an offshore laboratory needs to get almost $60.
MD: But you’re willing to bet that given the choice between a $60 offshore crown that’s hit or miss every time the dentist gets it and the $90–100 digital manufactured crown that drops into place almost every time, that they’re going to be smart enough and like that consistency enough to be willing to pay for that.
JG: I think the dentist would pay more than the price of an offshore crown for crowns that fit perfectly every time that are machine-made and not handmade, regardless of where it’s made — whether overseas or here. But I also think that digital manufacturing may actually lower the cost to equal the cost of offshore laboratories. Eventually we might be able to see our way to offering crowns that are $60 that are actually digitally manufactured. It’s not here today but we may be looking at it in the next few years.
MD: That would be the best of both worlds, wouldn’t it?
JG: Yes, a crown that really, really fits, and it’s the same price as an offshore crown.
MD: And it’s built so intelligently that it’s able to be offered at the same price as the offshore labs offer.
JG: Exactly. And what if it gets lost in the mail somehow — we have the digital information to fire it up again. We don’t need a model or anything. We can work completely in the dark without any kind of a model.
MD: And you’re also working with a company that is building an intraoral scanner, so at one point, if the dentist was onboard with you, he could scan it in his office — not even take an impression — and send you a file and you’d be able to manufacture the crown simply from that.
JG: We would be able to manufacture a crown from a file without ever manufacturing a model. We have only a model that exists in the computer, and it only assists us in design work. There’s never a physical model.
MD: That’s amazing to think about that. And that saves the doctor even more money by not having to take that $10 impression.
JG: And it saves us $7 or $8 in shipping costs one way and a lower shipping amount the other way because we’re not shipping a pound and a half of plaster back. That is the future. The future is going to be intraoral scanning and digital manufacturing.