CAD/CAM Porcelain Fused to Captek™
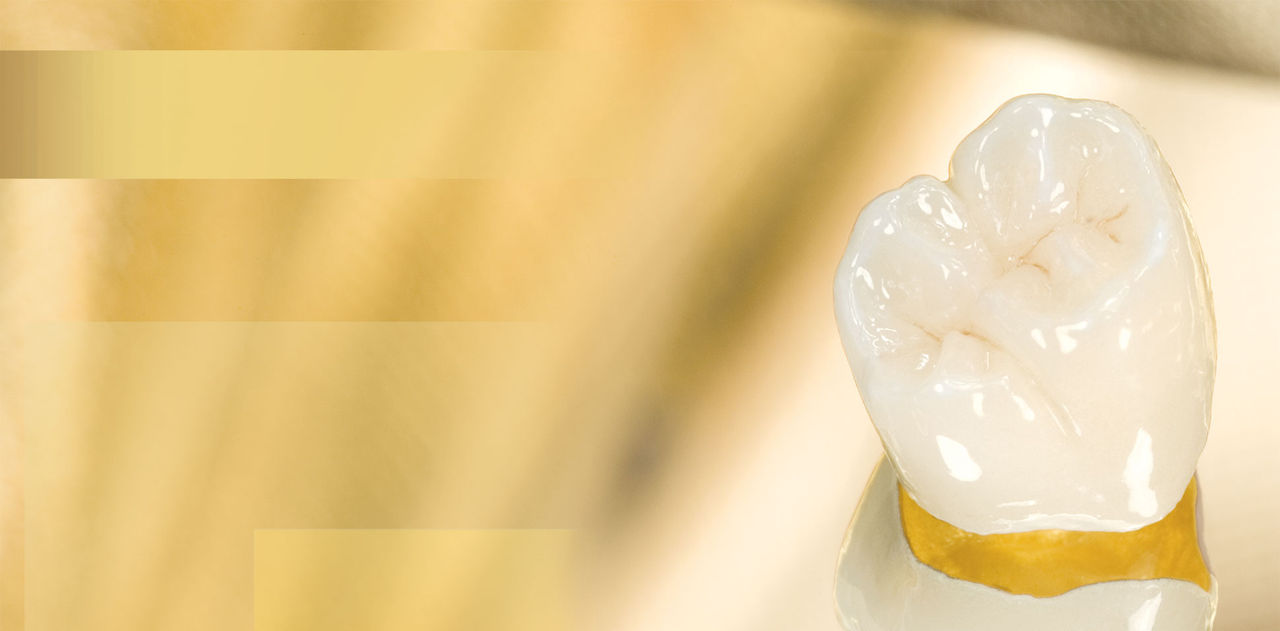
For years I have wondered why some seat appointments go so smoothly while so many others take so long. I never could figure out if blame fell on the patient, the lab or me. One thing I never considered was the material. The truth is, the limitations of the materials and techniques that labs are forced to use in traditional PFM fabrication can sometimes lead to these inconsistencies. Fortunately, we live in an era of great innovations. One of those innovations is pressed-to-metal merged with the accuracy of CAD/CAM.
This combination is making patient visits easier. That’s because margins fit better, esthetics are more consistent, and adjustments and seat times are greatly reduced. Plus, we get these advantages while using our standard protocol and cements because it’s still a PFM.
One of the most precise phases of full-crown fabrication is the waxing stage. That is because wax is more controllable and easier to manipulate than porcelain. As a result, it is easier to perfect the contours, the occlusion and the contacts. CAD/CAM technology goes well beyond just waxing. The full-contour wax pattern is actually computer-generated (digitally designed) to create a perfect tooth form over a Captek™ coping (Argen; San Diego, Calif.).
The traditional layering and baking of porcelain can be quite challenging. Porcelain condenses and shrinks up to 10% with each application and bake. These stresses can sometimes cause a natural deflection of the thin buccal margins of traditional PFMs. This is why at times we find our PFMs will fit too snug and possibly fall short of the margin. As hard as we all try, these natural inconsistencies only add to the time spent on chairside corrections.
The Beauty of CAD/CAM
Traditional PFM porcelain is applied in layers that are formed from a mix of ceramic powders and liquid. The resulting paste of each layer is then separately baked, each bake with a potential for internal stresses. It is a laborious process that results in a different shape with each bake. The porcelains that are used are shades of pink, white and gray. Although the technician works very hard on our behalf to meet our expectations, the limitations of the technique can lead to the occasional inconsistent shading for a traditional crown. Contours, contacts and occlusion can also be affected.
CAD/CAM’s ability to digitally design the pressing process means there is no need for powders or multiple bakes. Instead, it begins by scanning all dimensions important to the final restoration. The next step is the computer-generated full-contour waxing that is applied directly over the high-noble Captek coping. The result is a full-contour wax pattern with very accurate contours, contacts and occlusion. The fully waxed pattern and coping is then invested and made ready for the actual porcelain pressing.
In this next step, a highly esthetic ceramic ingot matching the prescribed shade is heated to a liquified state and then injected, or pressed, into the mold created by the burned-out wax pattern. At this point, the restoration can be finished with any customization desired.
The advantages of combining pressed ceramic with CAD/CAM have become very clear. Because there is no dimensional change to the ceramic, seat appointments require a lot less time. Additionally, as with any PFM, we can use any margin of our choice, even a porcelain butt margin, and expect an excellent fit.
But this is not the end of the story. If there was no metal under the porcelain, we would lose many of the advantages offered by CAD/CAM-designed PFMs. On the other hand, if that metal was cast we would have the challenges posed by oxidation and corrosion.
Captek, Redefining the PFM
There has been confusion on exactly how to define Captek. Some have called it a foil, pure gold or electroplated. Actually, it is none of these. Captek has been referred to as a composite metal because its component particles — pure Pt, Pd and Au, with a trace of Ag — are arranged similarly to the components of resin composite. Unlike cast metals, a cross section of Captek would reveal an interconnected reinforcing matrix of pure Pt and Pd particles surrounded in a sea of gold. The strong Pt-Pd internal reinforcing structure is thermally stable and rigid. It is these characteristics that neutralize the forces that can lead to distortion. While eliminating distortion helps Captek achieve, according to Dr. Dan Nathanson of Boston University, margin gaps of 15 microns, there are other reasons that Captek is a better choice.
Research conducted at Forsyth Dental Center and Boston University (funded by the NIH) has shown that Captek reduces bacterial plaque by at least 71% when compared to nonrestored teeth in the same mouth. Many of us have actually seen tissue heal and become healthier subsequent to placing a Captek restoration. This is because the nature of the pure particles creates an environment that inhibits bacterial colonization.
Captek doesn’t require oxidation to bond to porcelain. Instead, the porcelain bonds to a unique material called UCP that is applied to the surface of the coping. The UCP particles extend from the surface like thousands of microvilli, allowing for a true mechanical porcelain bond. According to research at Boston University, this combination increases the porcelain shear bond strength and shock absorption qualities well beyond most all other materials.
Although these are all important advantages, the most obvious advantage would be esthetics. There simply is no way to compare traditional cast PFMs to Captek when considering esthetics. The elimination of the oxidation layer means that there will never be black lines at the margin, black gums or darkened roots. Surprisingly, patients can tell the difference.
This was confirmed during a Harvard-Boston Universities study. Their presentation to the American Association of Dental Research in 2005 illustrated that even when compared to all-ceramics and cast PFMs with porcelain butt margins, Captek with metal to the edge provided the most natural esthetics near the normally difficult crown margins.
As we all know, there is nothing more predictable or easier to use than a PFM. And the same would also be true for Captek. And just like any other PFM, there are guidelines we need to follow that will help us to realize its full potential.
Porcelain requires adequate thickness in order to maintain its strength. I suggest that 2 mm of occlusal clearance be gained at preparation, and no less than 1.5 mm of total occlusal thickness of the crown at cementation. For axial reduction, 1 mm is minimal. Additionally, according to research published by Dr. Charles Goodacre of Loma Linda University in 2001, all PFMs should have preparation of 10–20 degrees.
Margin design for Captek is no different than any other PFM, and the same could be said for cementation, with one exception. In those instances in which crown retention is compromised, it is recommended that Captek crowns be air abraded with 50-micron aluminum oxide at 40 lbs of pressure. The air abrasion will remove the internal 22-micron surface of high gold, and leave a more retentive surface for your cement of choice.
Like other PFMs, Captek can be used anywhere: single crowns (posterior and anterior) and bridges (up to 15 mm pontic span); and they are fantastic over implants.
CAD/CAM and Captek
Like many of us, I have used PFMs with success for decades. Sure, they have their shortcomings, and the all-ceramics have done a pretty decent job of addressing these challenges. But PFMs have proven long-term predictability, and can be easier to manage than all-ceramics.
Now, old PFM technology has been updated with new technology. But this time, instead of having to learn an entirely new paradigm, instead of having limitations and new guidelines thrust upon us, we have the ability to continue using familiar techniques and principles that have been proven over time.
CAD/CAM-designed porcelain pressed-to-Captek provides incredible predictability in esthetics, fit, form and function. Moreover, when compared to the past, the increased density of the ceramic provides for greater strength and a better fit.