Obsidian®: A Restorative Solution Inspired by Stone-Age Technology
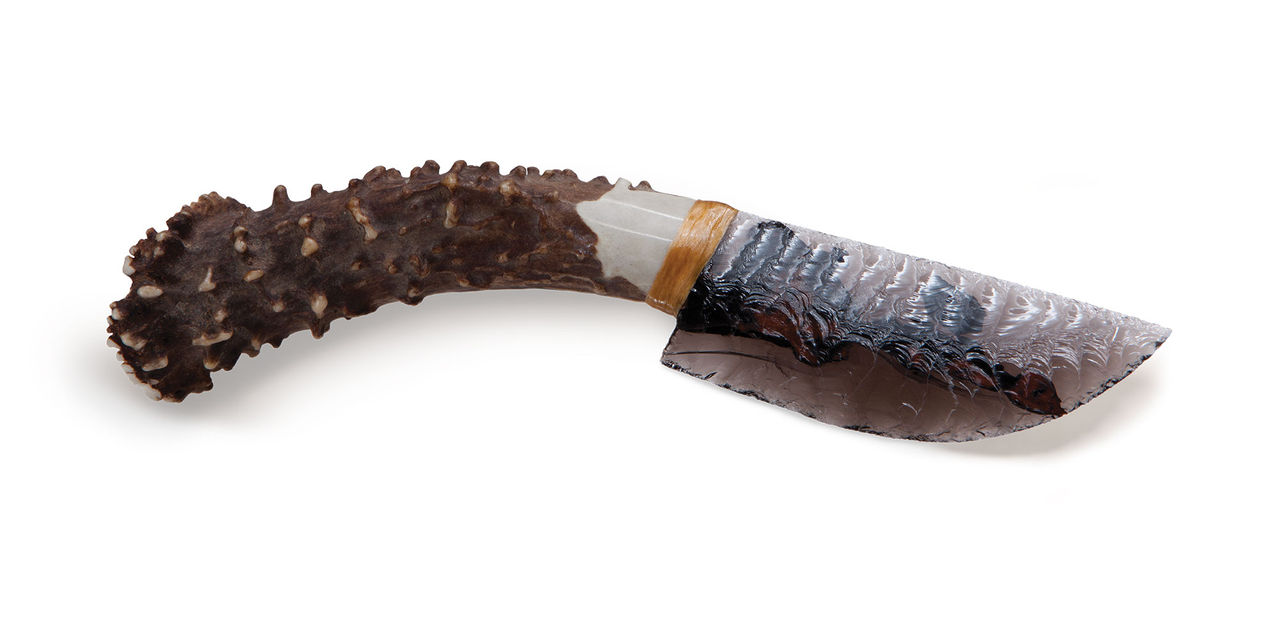
Clinicians across the United States have been intrigued about the release of Obsidian® Fused to Metal. Some have asked us at Glidewell Laboratories why we — the championing lab behind the monolithic revolution and BruxZir® Solid Zirconia — would take a seemingly backward step and tell them to start prescribing PFMs again. Though the data found by major research organizations and countless clinical successes have proven the benefits of monolithic zirconia,1, 2 there are still a limited number of indications for which zirconia is not the most ideal restorative material. Some of these indications include: bridge cases that lack the vertical dimension necessary for zirconia connectors; cases where the restoration must match PFMs located on the proximal teeth; and restoring endontically treated teeth that have crown or root staining that would bleed dark shadows through all-ceramic restorations.
Enter Obsidian lithium silicate ceramic, a natural-looking, state-of-the-art ceramic material that can be pressed to a metal coping to create the strongest and most esthetic PFM. With an average flexural strength five times that of conventional ceramics,3 Obsidian is a reimagining of proven restorative technology.
But why call it “Obsidian”? The restorative material takes more than just its name from the naturally occurring volcanic glass. In fact, both materials share a number of properties, including coloring, translucency, and chemical composition.
Clinicians who lack a familiarity with the geological sciences might perceive obsidian as being only a jet black color, and wonder how that might fit into a patient’s smile. In truth, the natural glass comes in a rainbow of colors as light refracts through the material at different thicknesses. Brown, blue, gray, green, purple, pink, red, yellow and white can be seen within the volcanic rock.4 These warm colors are created in natural obsidian through a process similar to how light shines through an oil-slick. Nanoparticles and microscopic bubbles within the glass shift the wavelength of light, resulting in myriad brilliant hues.4
Additionally, the chemical formulas of both materials are notably comparable. Part of the classification of naturally occurring obsidian is that it must consist of at least 70 percent SiO2 (silicon dioxide).5 Obsidian ceramic consists of 50–60 percent SiO2, meaning that both are mostly comprised of the exact same chemical compound. Their mainly homogenous natures enable an excellent level of translucency, which, for Obsidian ceramic, cements the material’s ability as a highly esthetic restorative solution.
Extending beyond the shared tangibles, the story of Obsidian lithium silicate ceramic mirrors the history of the volcanic material — that is, a history of longtime, proven use and modern repurposing.
Historical Obsidian
Archeologists suggest that volcanic obsidian was used by cultures around the world, with scholars finding evidence of use as far back as 700,000 B.C. in what is now modern-day Kenya.6 The first attested urban use occurred in the fifth millennium B.C. at a site called Tell Brak in Mesopotamia, which is reportedly one of the world’s first cities.7 There, researchers found caches of obsidian blades and discs, and even an ornately decorated chalice. In Africa, the Middle East, Eurasia and the Americas, ancient peoples used the material for tools, weapons and decoration, and in bartering, long before the advent of metallurgy.8, 9, 10
Obsidian is formed by the rapid cooling of silicate-rich lava. The nature of the lava, being both viscous and polymerized, prevents the diffusion of atoms during cooling, leaving behind a glass ceramic that’s unable to form a crystalline structure. The lack of crystal formation results in a material that is significantly isotropic and homogenous — qualities that generate benefits for which ancient peoples prized obsidian. Put simply, it’s brittle, and the pieces that flake off have a uniform, ultra-sharp edge.11
In Africa, the Middle East, Eurasia and the Americas, ancient peoples used the material for tools, weapons and decoration, and in bartering, long before the advent of metallurgy.
Its characteristic sharpness allowed its use in nearly every cutting instrument imaginable: axes, arrowheads, swords and knives. Cultures that didn’t have access to the cooled lava flows traded other valuables to secure obsidian for their own societies. Historians have discovered that obsidian was a highly traded commodity, and have been able to map out trade routes thanks to the material’s unique fingerprint. Essentially, each sample carries a specific mixture of trace elements that is unique to the volcanic activity in which it was formed. It is through this fact that historians are able to know that Mesoamerican tribes (the indigenous cultures occupying Mexico and Central America prior to the Spanish conquest) transported the material in great quantities across the length and width of the peninsula, and, in the South Pacific, some tools were transported distances of nearly 2,000 miles over land and sea.11 It’s evident from the vast distances that obsidian was moved that ancient cultures defined the glass as a precious commodity, with tools and weapons crafted from obsidian being extremely valuable assets.
Modern Tools from Volcanic Glass
As cultures learned to smelt copper, and later bronze, the value and use of obsidian decreased significantly. These metals were far easier to obtain, work and shape than obsidian,12 and they were used in tools that ushered the world out of the stone age and brought about more advanced society.13
Today, most people know obsidian as a material with ornamental value, or as a material that represents ancient times and weapons. However, in the 1960s and 1970s an inquisitive, stone-loving, college dropout named Don Crabtree rediscovered a method of making Mesoamerican obsidian blades (so-called prismatic blades) that he claimed were sharper and more precise than surgical steel.14 Research later confirmed that his obsidian blades were in fact not only sharper than surgical steel, but also, when used as surgical instruments, led to faster wound healing and decreased scarring.15 Don Crabtree’s discoveries and contributions to the science of flint-knapping (the manufacture of tools from stone), would define him as one of the foremost authorities in the field of lithic studies, for which he was awarded an honorary doctorate.14
Where surgical steel blades have a rough, sawlike cutting edge when viewed under a microscope, scalpels made from obsidian maintain their smoothness to a cutting edge that’s only about 3 nanometers thick.14 The precision of obsidian scalpels is obtained through the process in which they’re made. Rather than taking a piece of obsidian and flaking off a sharp sliver, obsidian blades intended for surgery are honed out of meticulously prepared obsidian cores. Taking a blade from the center, rather than the edge, of a sample is the same technique that ancient cultures utilized to produce ultra-sharp blades up to 12 inches in length. Even though there is no definitive evidence that these ancient peoples used these blades for soft-tissue surgical operations, it is possible that these tribes, which possessed obsidian blades, might have used them for ceremonial tissue cutting and human sacrificial acts.14
These stone-age scalpels approach the sharpness of diamond, and their low cost in comparison may eventually result in their becoming approved and adopted by a wider segment of medical professionals.
Where surgical steel blades have a rough, sawlike cutting edge when viewed under a microscope, scalpels made from obsidian maintain their smoothness to a cutting edge that’s only about 3 nanometers thick.
Repurposing Age-Old Dentistry
Just as these quality-seeking surgeons repurposed time-tested technologies, the research and development team at Glidewell Laboratories sought to create a restorative option that utilized the best aspects of traditional PFM crowns. It’s undeniable that the underlying metal coping provides a proven level of strength, and its ability to block out dark stump shades has been a benefit in the esthetic zone. However, restorations are only as strong as their weakest component. In traditional PFMs, that weakness is found in the feldspathic porcelain. Although the problem of failure is multifactorial, most frequently, bilayer restoration failures are related to cracks in the ceramic.16
The literature cites studies observing various causes of ceramo-metal failures. Failure rates range between 5 percent and 10 percent over 10 years.17 Strub et al. found failure rates of ceramo-metal restorations as high as 3 percent over five years.18 Hankinson and Cappetta19 and Kelsey et al.20 found a failure rate between 2 percent and 4 percent that occurred after two years. They also found that, due to a repetition of consistent occlusal contacts, after four to five years the failure rate rose to 20–25 percent.
In an effort that lasted more than seven years and cost upward of $7.5 million, the research team at Glidewell Laboratories devised a lithium silicate ceramic that looks promising as a porcelain replacement and would address the problem of ceramic failure. Named for the desirable characteristics found in the natural material, Obsidian lithium silicate ceramic exhibits twice the chip resistance and more than five times the strength of feldspathic porcelains, and can be pressed to metal to form a highly esthetic bilayered restoration. The release of Obsidian sets a new high-strength benchmark for the time-tested PFM.
Cutting-Edge Solutions Built on Proven Histories
The restorative material from Glidewell Laboratories shares a name with natural obsidian and mimics — on a much smaller chronological scale — the lava-formed material’s history. Keeping only the beneficial natural material’s innate characteristics of color and translucency while forgoing the brittleness and sharpness, Obsidian lithium silicate stands as a solution based on principles that have functioned excellently over a half-century of clinical use. Ideal for cases that aren’t suited for monolithic zirconia, such as esthetic zone cases that require the covering of dark preps or endodontic posts, Obsidian is a state-of-the-art PFM for today’s clinician.
Obsidian lithium silicate stands as a solution based on principles that have functioned excellently over a half-century of clinical use.
References
- ^Clinicians Report, TRAC Research, July 2014.
- ^2015 Dental Advisor Four-year Clinical Performance study. THE DENTAL ADVISOR, 3110 West Liberty, Ann Arbor, MI 48103, info@dentaladvisor.com.
- ^Data provided by the Glidewell Laboratories Research and Development Department, 18651 Von Karman Ave., Irvine, CA 92612.
- ^Nadin E. The secret lives of minerals. Engineering & Science. 2007. 1:10-20.
- ^Ma C, Rossman GR, Miller JA. The original of color in “fire” obsidian. The Canadian Mineralogist. 2007. 45:551-7.
- ^Merrick HV, Brown FH, Nash WP. Society, Culture, and Technology in Africa, Volume 11, 1994 (Masca Research Papers in Science and Archaeology Supplement). University of Pennsylvania Museum of Archaeology.
- ^Ur JA. Early Mesopotamian urbanism: a new view from the North. Antiquity. 2007;81(313):585-600.
- ^Moorey PRS. Ancient Mesopotamian materials and industries: The archaeological evidence. Winona Lake (IN): Eisenbrauns; 1999.
- ^Bunny S. American trade routes for obsidian. New Scientist (1985-04-18).
- ^Schmandt-Besserat D. Early technologies (invited lectures on the Middle East at the University of Texas Series: volume 3). Malibu (CA): Undena Publications; 1979.
- ^Cotterell B, Kamminga J. Mechanics of pre-industrial technology: an introduction to the mechanics of ancient and traditional material culture. Cambridge (UK): Cambridge University Press; 1992. p. 127.
- ^Tylecote RF. A history of metallurgy. 2nd ed. London: Maney Publishing for the Institute of Materials; 1992.
- ^Fagan BM. The seventy great inventions of the ancient world. London: Thames & Hudson; 2004.
- ^Buck BA. Ancient Technology in Contemporary Surgery. Western Journal of Medicine. 1982 Mar;136(3):265-9.
- ^Disa JJ, Vossoughi J, Goldberg NH. A comparison of obsidian and surgical steel scalpel wound healing in rats. Plast Reconstr Surg. 1993 Oct;92(5):884-7.
- ^Özcan M. Fracture reasons in ceramic-fused-to-metal restorations. J Oral Rehab. 2003;30(3):265-9.
- ^Coornaert J, Adriaens P, De Boever J. Long-term clinical study of porcelain-fused-to-gold restorations. J Prosthet Dent. 1984 Mar;51(3):338-42.
- ^Strub JR, Stiffler S, Schärer P. Causes of failure following oral rehabilitation: biological versus technical factors. Quintessence Int. 1988 Mar;19(3):215-22.
- ^Hankinson JA, Cappetta EG. Five years’ clinical experience with a leucite-reinforced porcelain crown system. Int J Periodontics Restorative Dent. 1994 Apr;14(2):138-53.
- ^Kelsey WP 3rd, Cavel T, Blankenau RJ, et al. 4-year clinical study of castable ceramic crowns. Am J Dent. 1995 Oct;8(5):259-62.