Employee Spotlight: Chief Technology Officer Mike Selberis
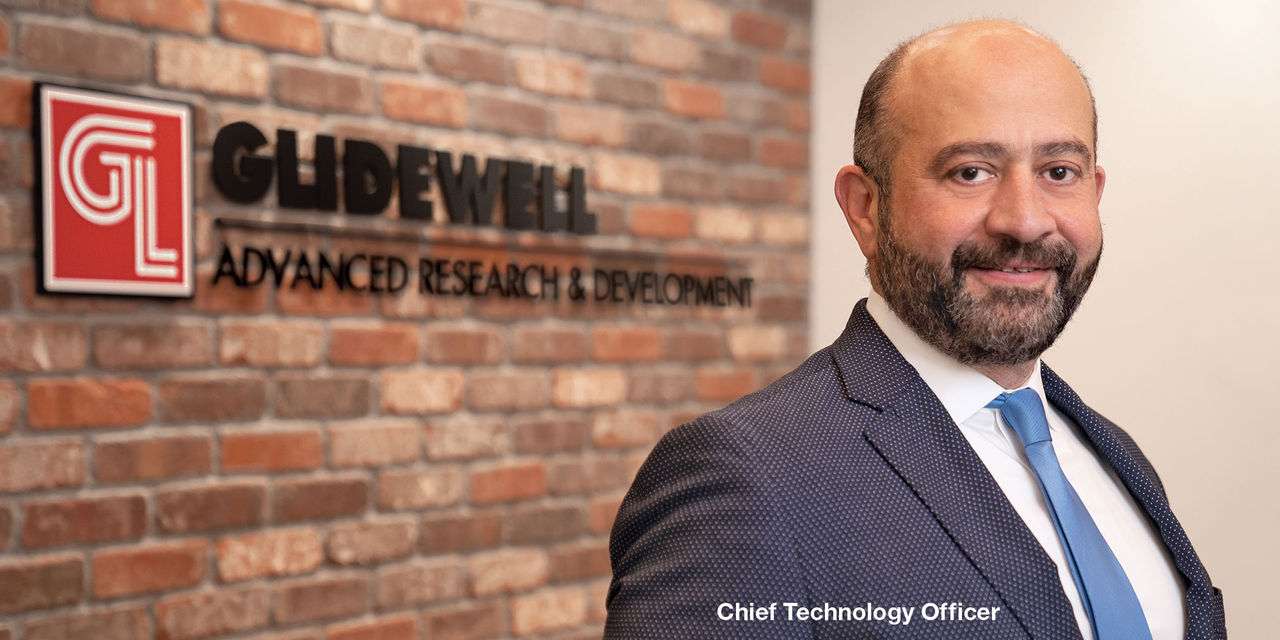
Mike Selberis has spent more than 20 years spearheading major technological advancements in several industries. He started his career as an electrical engineer working on missile programs and the International Space Station. After nine years in the aerospace industry, Mike transitioned to several software companies as well as a medical laboratory, where he was responsible for overseeing the company’s information technology systems. Mike was then contacted by Glidewell Dental about coming onboard to launch new technology that would enable dentists to digitally submit cases with maximum accuracy and efficiency.
Since successfully supporting Glidewell with that first digital initiative 10 years ago, Mike has continued to play a key role in helping Glidewell become a leading innovator in dental technology. As chief technology officer, he oversees information technology, hardware engineering, CAD/CAM software development and materials R&D teams. Throughout his tenure, his teams have introduced several innovative products and services — all with one goal: to help practicing dentists deliver quality restorations and enhance efficiency within their practice.
CHAIRSIDE® MAGAZINE: How have you and your team been able to consistently develop cutting-edge products and services for clinicians?
MIKE SELBERIS: Creating new technology for doctors is a collective effort. Even though I oversee the development process, my teams wouldn’t be able to execute our ideas without the knowledge we receive from our in-house dentists and skilled technicians. And of course, much of our inspiration comes from the doctors we serve, who are constantly adopting new technologies to enhance clinical outcomes. As innovation is at the heart of what we do, we’re constantly looking for ways to build new products and services that will help dentists better serve their patients.
CM: One product that you worked with your teams to recently launch is the glidewell.io™ In-Office Solution. How is this innovative technology advancing dentistry and helping doctors to improve the services they provide patients?
MS: glidewell.io is a chairside ecosystem that makes one-day restorative dentistry a reality. It gives clinicians the ability to mill a precise-fitting BruxZir® Solid Zirconia crown in less than 40 minutes. With glidewell.io, clinicians have access to all of the knowledge Glidewell Laboratories has accumulated from decades of working on millions of restorative cases. We have bundled all of that know-how into a compact unit that fits into a dentist’s office. It brings all of the same technology from a world-class dental laboratory — with all of its benefits — right to the doctor’s fingertips.
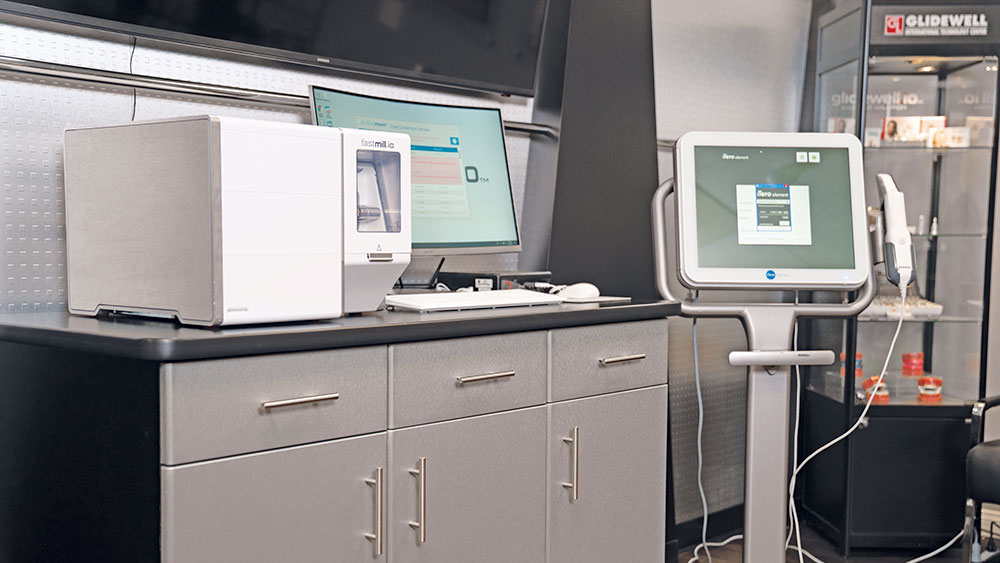
The glidewell.io In-Office Solution is one of the innovative systems that Mike Selberis’ teams have recently developed to provide a streamlined workflow for dentists.
CM: How does glidewell.io compare with other in-office milling systems on the market?
MS: For starters, glidewell.io is the only in-office system that can mill fully sintered zirconia. Doctors don’t have to put the restoration in an oven to sinter it, and it doesn’t need to be stained or glazed. Dentists can fabricate crowns from BruxZir NOW milling blocks and provide their patients with long-lasting restorations in one appointment. The glidewell.io In-Office Solution is also the only system that sends a support team to the clinician’s practice to provide onboard training and offer ongoing customer support directly from the manufacturer. The system has become very popular in dental offices across the U.S. because it gives doctors an easy-to-use system that’s affordably priced.
The technology behind fastdesign.io™ Software also makes glidewell.io unique. We worked with the University of California, Berkeley, to develop exclusive machine-learning algorithms, which use artificial intelligence to enhance the accuracy and design of restorations fabricated in-office. The latest developments to fastdesign.io don’t rely upon basic library teeth as templates to create restoration proposals. Instead, the software designs the restorations based on real-world data from Glidewell Laboratories, which has the largest, most diverse database of dental cases worldwide. The software is also constantly learning and improving as it goes, and that technology is a first for the industry.
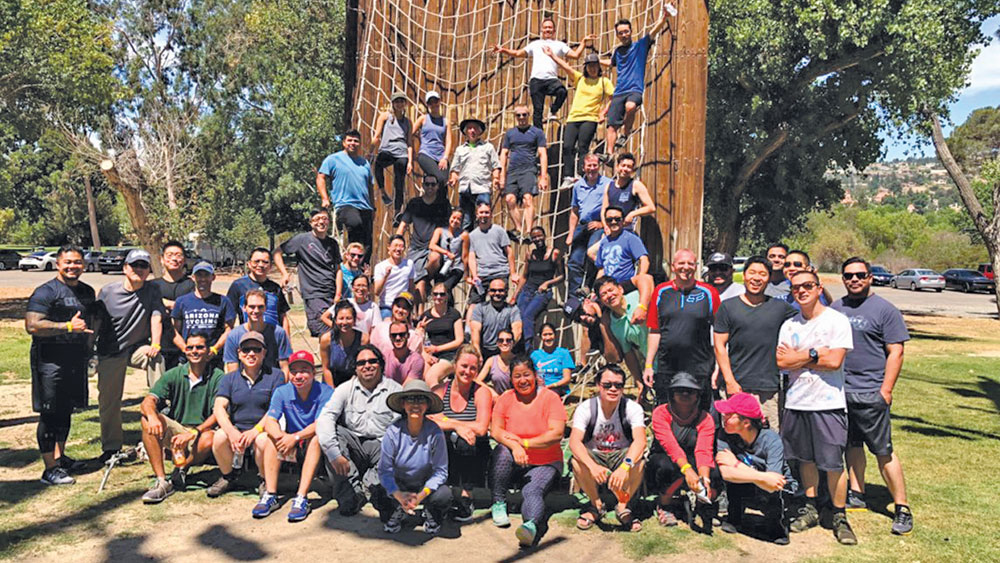
Mike and the Materials R&D department during a team-building exercise at the Orange County Ropes Course.
CM: Is there something about the culture at Glidewell that has been a key factor in helping you become an industry leader?
MS: Vertical integration certainly plays an important role. Most dental companies provide either materials, technology or lab services. But at Glidewell, we create everything in-house — from hardware, to software, to restorations and more. Since we have all aspects of the dental manufacturing process represented under one roof, we’re able to do things more rapidly. That is the vision of our founder, President and CEO, Jim Glidewell, CDT. He wants the company to be able to control production from start to finish so that we can constantly innovate and continuously deliver industry-leading services without external limitations. For example, when we created glidewell.io, our hardware team built the mill, our software team created the CAD/CAM operating system, and our Research and Development department created many of the dental materials. Each part of the process was designed to optimize another part. We believe that when a company creates everything in-house, it leads to a seamless and successful customer experience.
CM: Is that what you’re thinking about as you’re developing technology — what type of experience this product or service will create for the customer?
MS: My goal is to create products and services so they’re extremely user-friendly. I want doctors to be able to say: “Wow! That was really easy to use.” I believe that our customer is looking for “DDS” — “drop dead simple” — so we’re constantly looking for ways to streamline their workflow while still providing ample versatility.
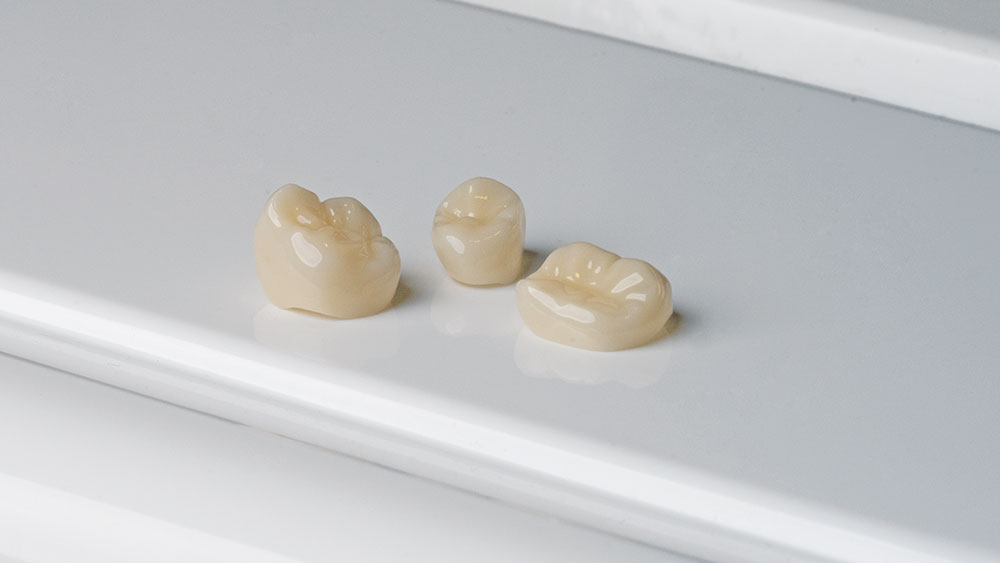
In collaboration with the University of California, Berkeley, Mike and his team were the first in any industry to use AI data to generate and manufacture 3D objects. Pictured above are some of the crowns they milled using this technology.
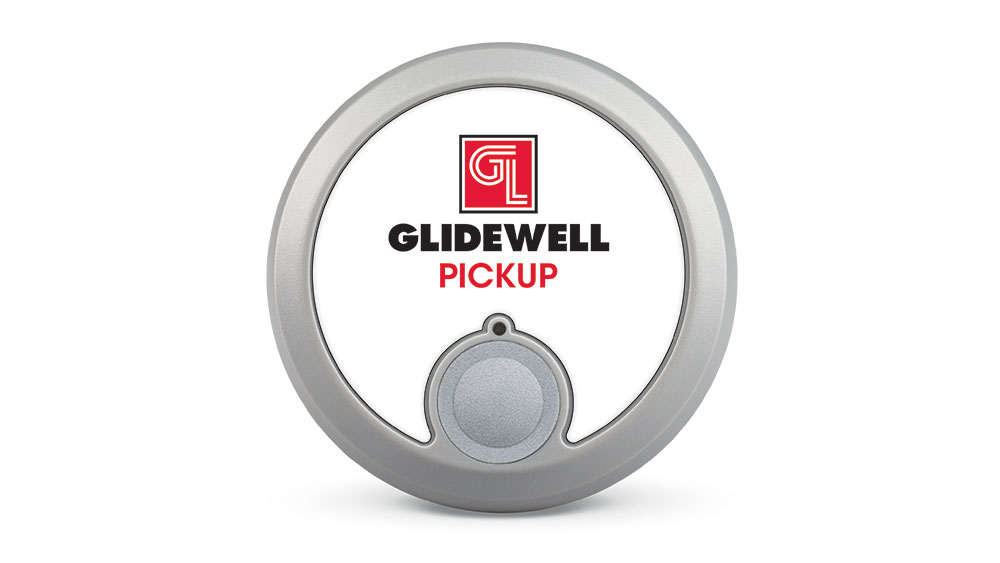
The Glidewell Pickup Button is one of the latest products Mike and his teams have developed to help improve the customer experience.
CM: Glidewell wants to create a great experience not only for customers who use their technology but also for the employees who create it. I know you have an ever-expanding team of more than 350 people. What has attracted so many tech professionals to work at Glidewell?
MS: We provide an opportunity for our team to work on some of the coolest, most advanced technologies in the industry. For example, a lot of companies talk about artificial intelligence, but we live it, generate it, discover it and create it. Jim Glidewell gives us the freedom to innovate, so we’re constantly providing employees with plenty of opportunities to learn, grow and develop. For example, we’re about to launch a tech gym, which is a creative “playground” where employees can go in their free time to experiment with their own ideas. It will have 3D printers, robots, specialized software and other technology for them to use. There’s only one rule: They can’t spend time on anything work-related. The tech gym is designed for them to have fun and cultivate their own interests because all employees are encouraged to innovate. Whether it’s a new cellphone case or a different gadget, we want them to have an environment where they can create it.
CM: You’ve developed so many products and services — do you have any favorites?
MS: One of my favorite concepts that we recently developed was the Glidewell Pickup Button, which is similar to the Amazon Dash Button. The Pickup Button offers an easy way for dentists to request a case pickup. The only thing doctors have to do is push the Pickup Button, and within a few hours a FedEx or UPS driver will arrive at the practice to pick up their cases and deliver them to Glidewell Laboratories. It’s a very easy service for our customers to use. They can still call our office if they want, but the Pickup Button saves them time. We always want to give our customers convenient options that save time and make it easy to work with us. So if dentists want to use this service, all they have to do is contact us and we will ship them a free Pickup Button.
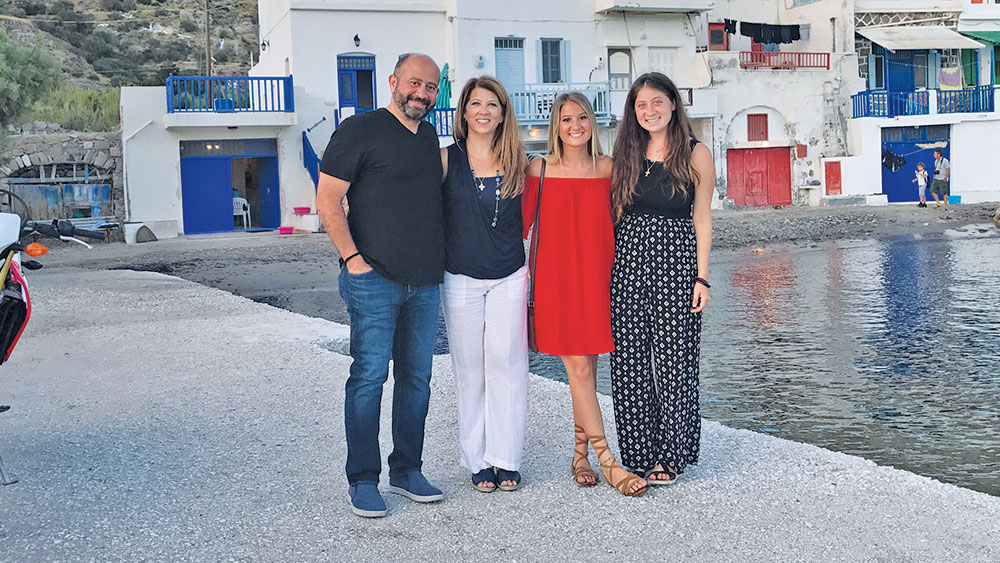
Mike on a family vacation in Milos, Greece.
CM: Considering innovation is at your core, I’m sure you constantly have something new in the works. What exciting projects can customers look forward to?
MS: We have a number of projects in the pipeline, including a new service called Click-to-Connect. Dentists will be able to log in to the My Account feature on glidewelldental.com, where they will find all of their current and former cases. For example, if the clinician has a question on a particular BioTemps® Provisionals case, the doctor will be able to simply click on that case and a technical advisor in the BioTemps call center will give them a call within a few seconds. The customer support representative will already have all of the case information ready to answer the dentist’s questions. The whole concept is that we want to connect the doctor to the right person for the right reason every time. We want to give them a smooth, hassle-free experience whenever they work with us. Of course, they will still be able to just pick up the phone and call us as well.
CM: How about glidewell.io? Are there any interesting updates in the near future?
MS: As I mentioned, glidewell.io is an ecosystem. We will continue to expand its capabilities by adding more products, services and apps. We’re now in the process of designing a 3D printer for glidewell.io, which means dentists will be able to not only mill crowns in-office, but print them along with a number of other dental prosthetics and appliances.
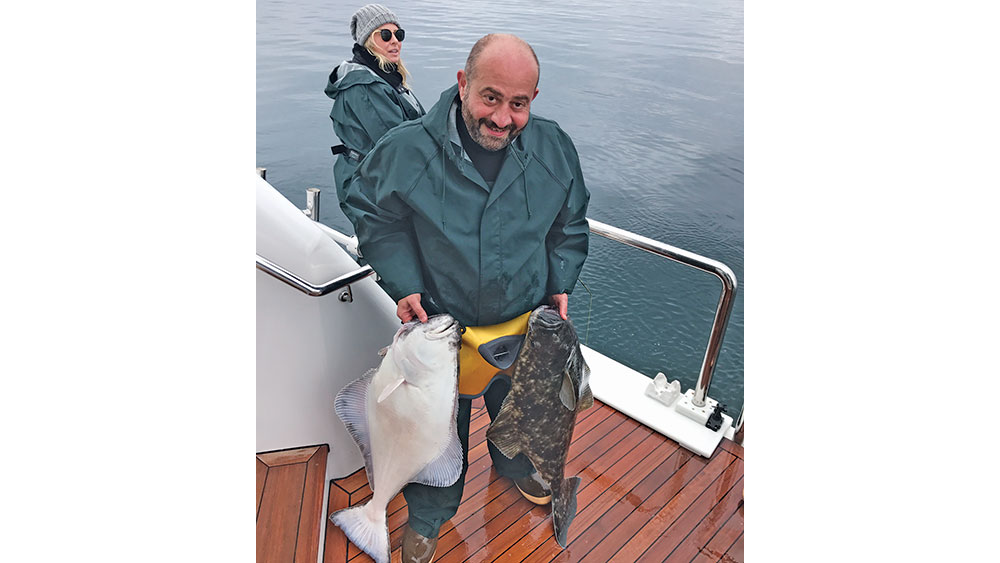
Mike enjoying leisure time on an Alaskan fishing trip.
CM: It’s obvious that you invest a lot of time into creating technology. What do you do when you’re not developing a new idea?
MS: I enjoy spending time with my wife and three adult daughters, who keep us busy. We especially love traveling to Greece, which is where my family is from. I love cooking Mediterranean food. Occasionally on Saturdays, when I have extra time, I’ll cook an entire gourmet meal from scratch. I also love hiking and deep-sea fishing.
CM: Thank you for sharing your Glidewell journey and giving us a behind-the-scenes glimpse at the world of technology. We’re excited to see what big innovations develop during the next chapter of your story.
MS: Thank you. It has been my pleasure.