Obsidian® Fused to Metal: A 3-Year Retrospective
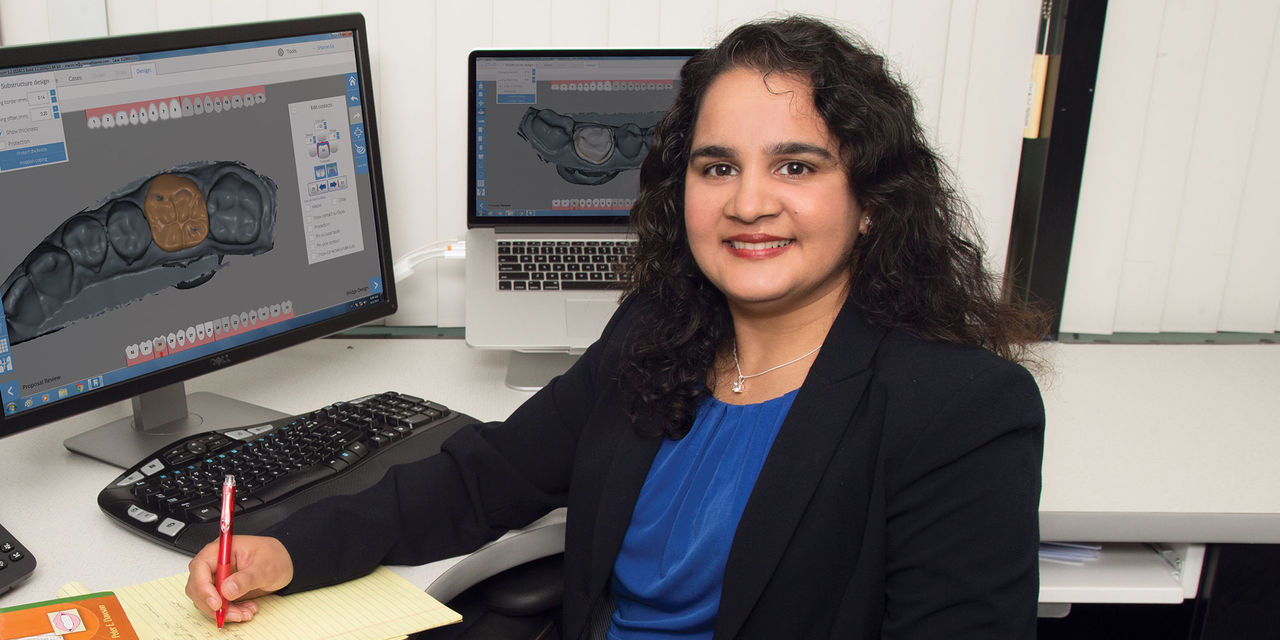
Obsidian® lithium silicate is a ceramic material developed by the Research & Development Team at Glidewell Dental to be strong and esthetic. Unlike other lithium silicate formulations, Obsidian ceramic can be fused to metal, creating a completely new generation of ceramo-metal restorations. After nearly a decade of research and engineering, Glidewell Dental released Obsidian Fused to Metal to clinicians across the United States.
Why would Glidewell Dental develop and release a ceramic fused to metal solution when monolithic materials such as BruxZir® Solid Zirconia are available to clinicians? While monolithic restorations work well, there are still situations for which they are not ideal, like cases with discolored or dark stump shades, restorations over titanium implant abutments, and bridge cases that lack the vertical dimension necessary for all-ceramic connectors.
The conventional PFM has been used to address those situations even though feldspathic porcelain is prone to chipping and fracturing. For this reason, Glidewell Dental aimed to develop a ceramic restorative material that would impart enhanced durability through chip resistance and strength while preserving the long-proven benefits of the PFM.
COMPARING OBSIDIAN FUSED TO METAL TO PFM
In a comparison of strength, Obsidian Fused to Metal performs over four times better than porcelain fused to metal in the trilayer biaxial-flexure test conducted according to ISO 6872, and two times better in the edge-chipping test described by Quinn et al. (Fig. 1).1,2 This increased strength and resistance to chipping and fracture adds longevity to the final restoration, making it an advantageous choice over conventional PFMs.
Obsidian Fused to Metal offers more than just enhanced strength. Using tools from today’s era of digital dentistry, the metal copings of these advanced bilayered restorations are produced by a method known as selective laser sintering, which is similar to 3D printing. This laser-sintering technique uses a computer-controlled laser to create metal understructures that have a comparable clinical fit to those created through the traditional lost-wax casting process at a thickness that is on average 30 microns less than conventional copings (Figs. 2a, 2b).3,4,5,6
Obsidian Fused to Metal crowns and bridges are fabricated via a digital workflow that enables clinicians to prescribe cases via traditional or digital impressions. Once the lab has a digitized model — either by receiving it digitally from the clinician or by scanning a stone model poured in-house — a bilayered crown design is created with dental CAD software. Then, the understructure portion of the design is sent to a metal printer and fabricated via laser sintering. The crown anatomy pattern is 3D printed in wax, conjoined to the metal coping, and encased in an investment material. The wax portion is then burned out to leave behind the shape of the crown anatomy so that Obsidian ceramic can be heat-pressed into the resultant cavity to form the restoration (Figs. 3a–3d). This computer-informed process increases the overall accuracy of the restoration, limiting the errors that are seen in all-manual workflows.
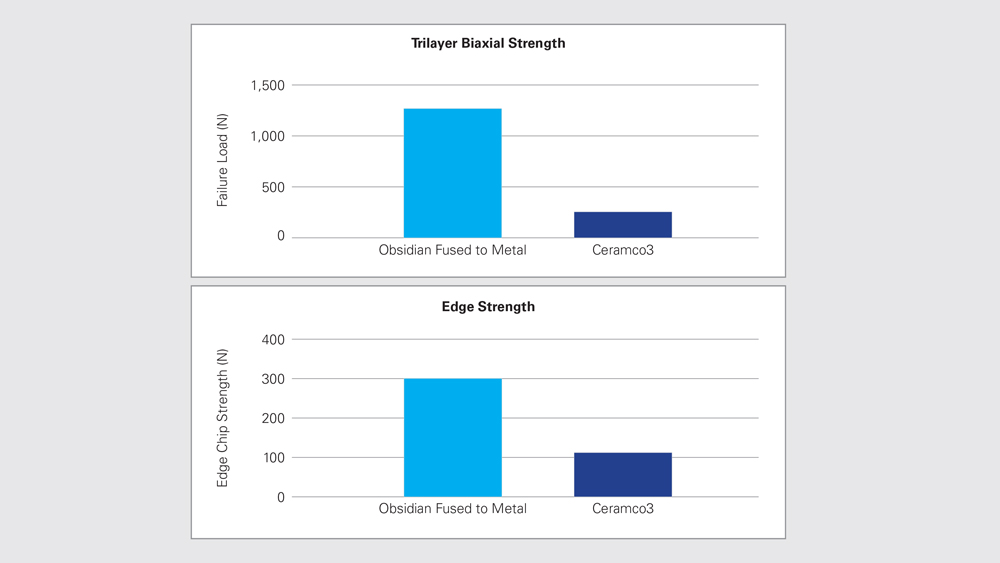
Figure 1: Graphs depicting the comparisons of trilayer biaxial strength and edge strength for Obsidian lithium silicate ceramic and Ceramco®3 porcelain (Dentsply Sirona Inc.; York, Pa.).
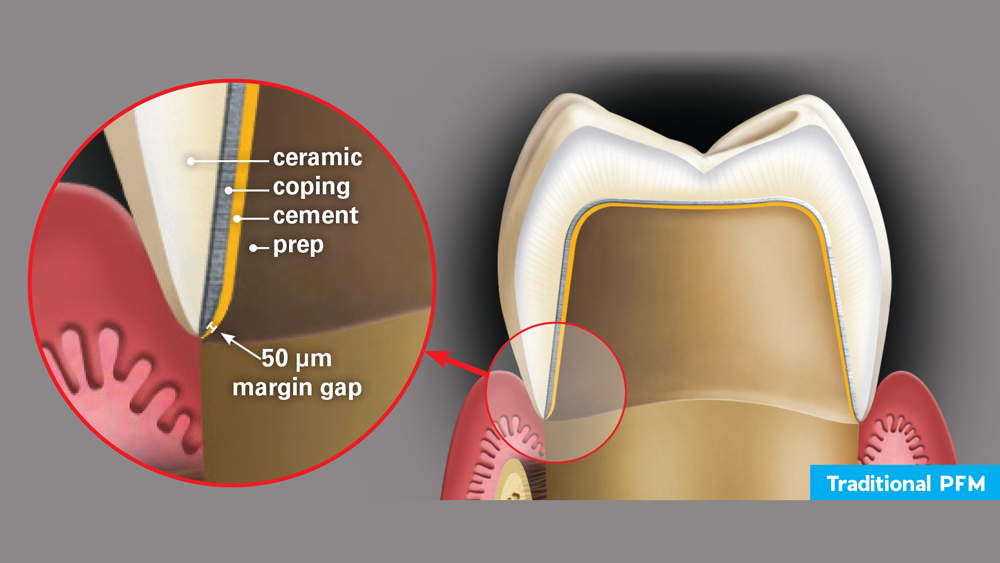

Figures 2a, 2b: The laser-sintering process used for Obsidian Fused to Metal restorations produces copings with superior accuracy and fit. Being fabricated by laser and designed digitally, the space between preparation and coping is reduced down to 20 microns on average, significantly less than the 50-micron standard achieved with traditional casting methods. This reduction helps reduce cement washout and may limit bacterial infiltration.
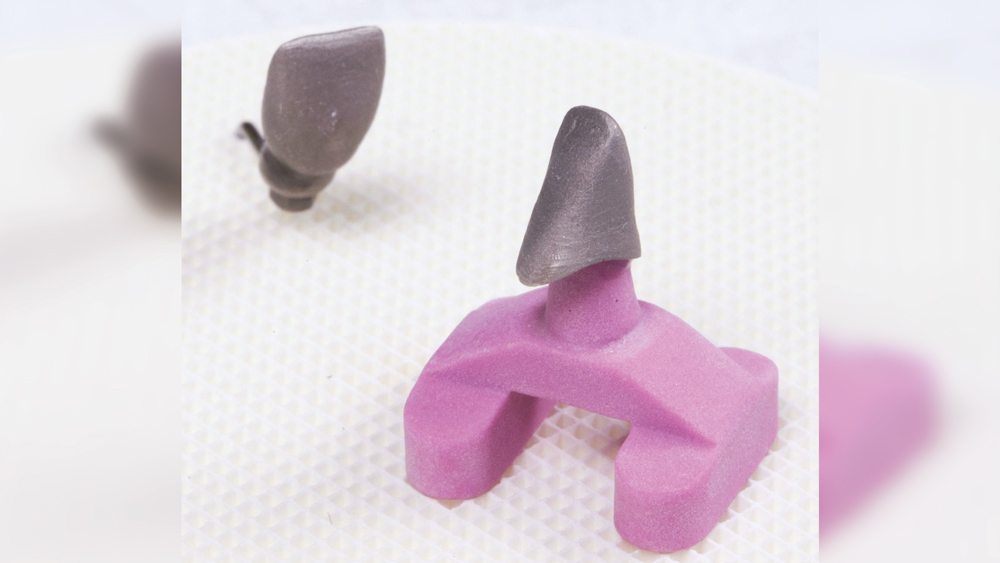
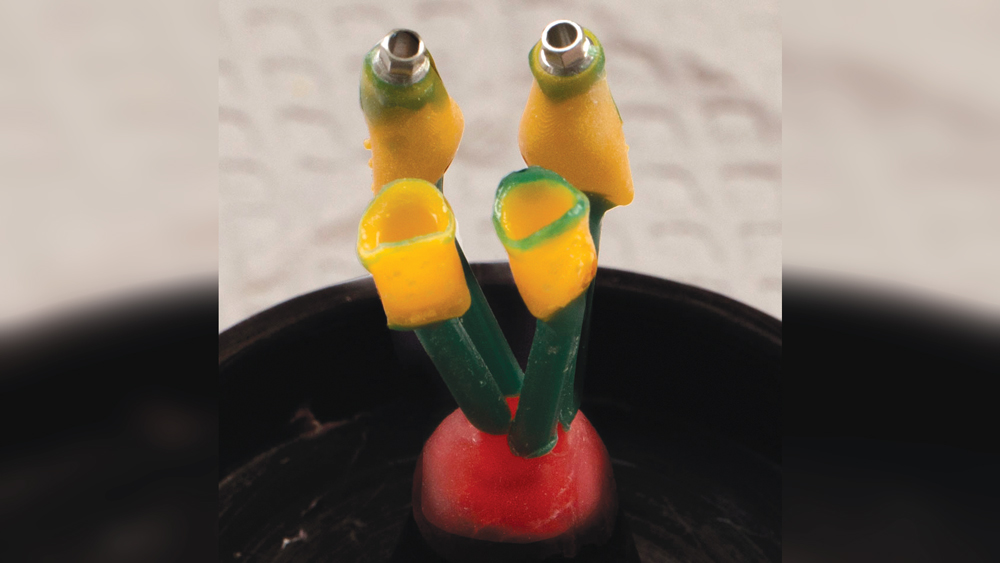
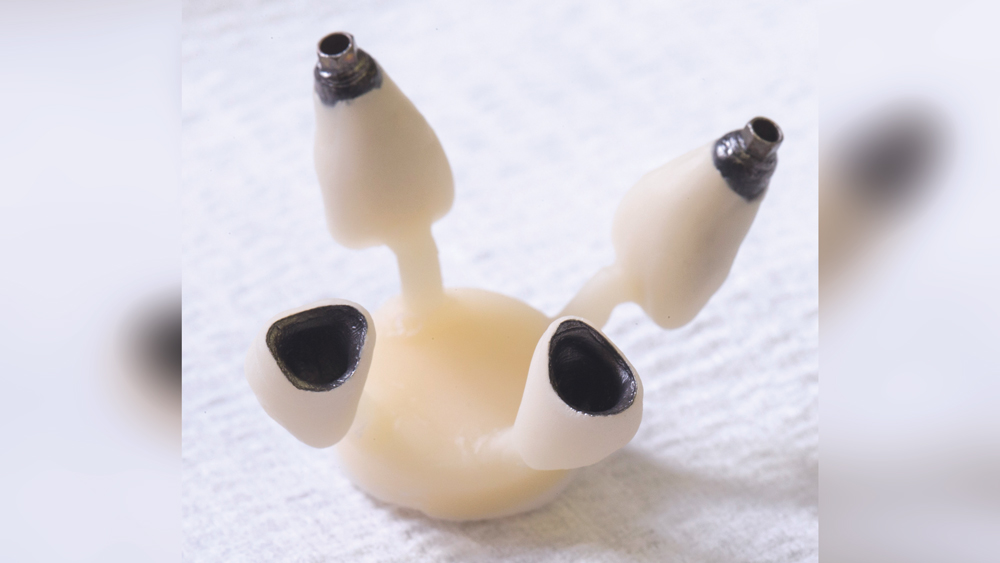
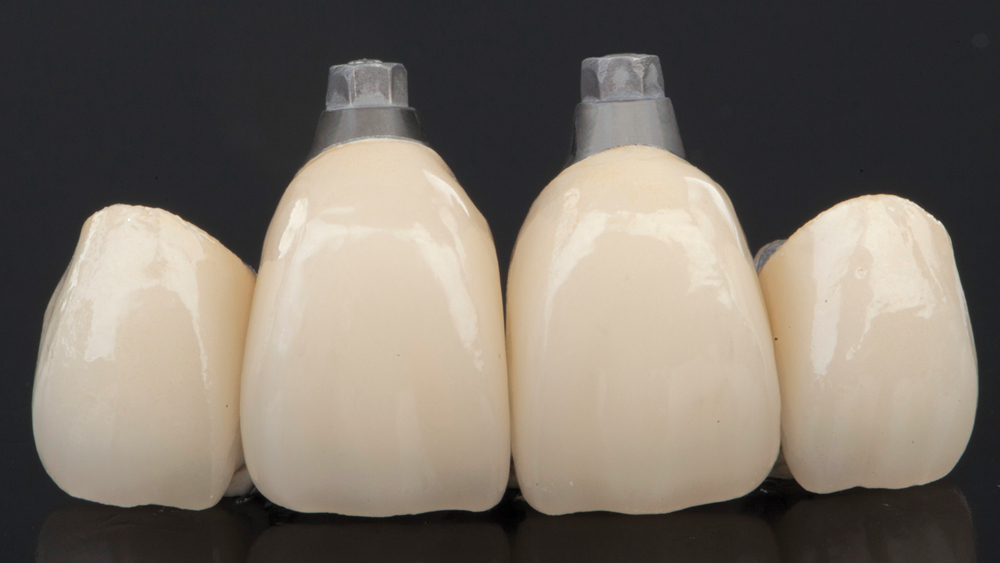
Figures 3a–3d: Obsidian Fused to Metal crowns are created by joining laser-sintered copings to 3D printed wax anatomy patterns. The waxed-up copings are sprued and invested prior to undergoing a lost-wax firing cycle, which creates a mold into which Obsidian ceramic can be heat-pressed.
CLINICAL PERFORMANCE OF OBSIDIAN FUSED TO METAL
Staff dentists at Glidewell Dental have been delivering Obsidian Fused to Metal restorations since 2014, testing the material, observing its suitability and validating its use in clinical dentistry (Fig. 4). In the Glidewell Dental operatories, Drs. Siamak Abai, Justin Chi and Anamaria Muresan placed 205 Obsidian Fused to Metal crown and bridge units in 66 patients from 2014 to June 2017 (Figs. 5a–6b), observing the performance of the restorations for a period of up to three years (Tables 1a–1f).
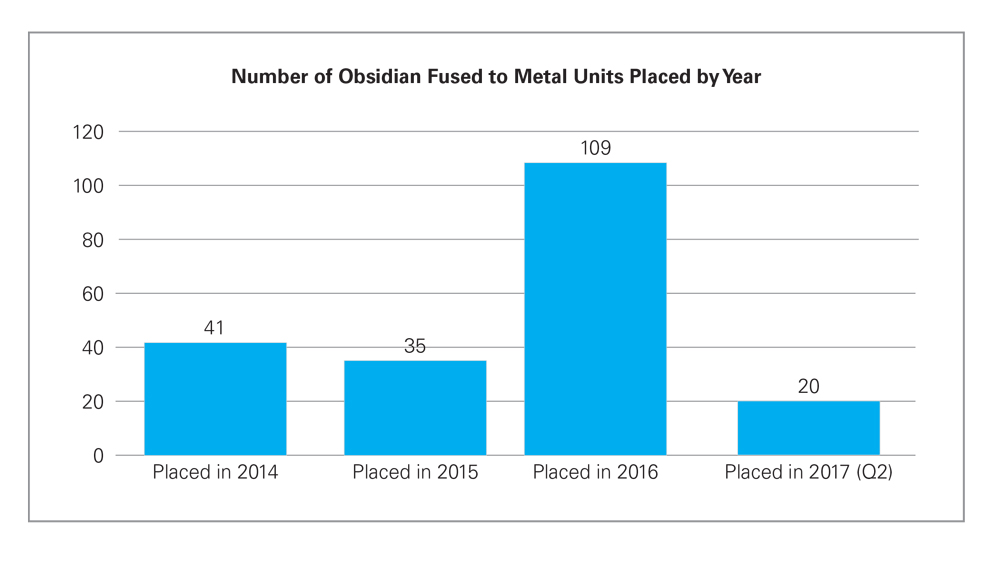
Figure 4: Obsidian Fused to Metal restorations have been tested by Glidewell Dental clinicians since 2014.
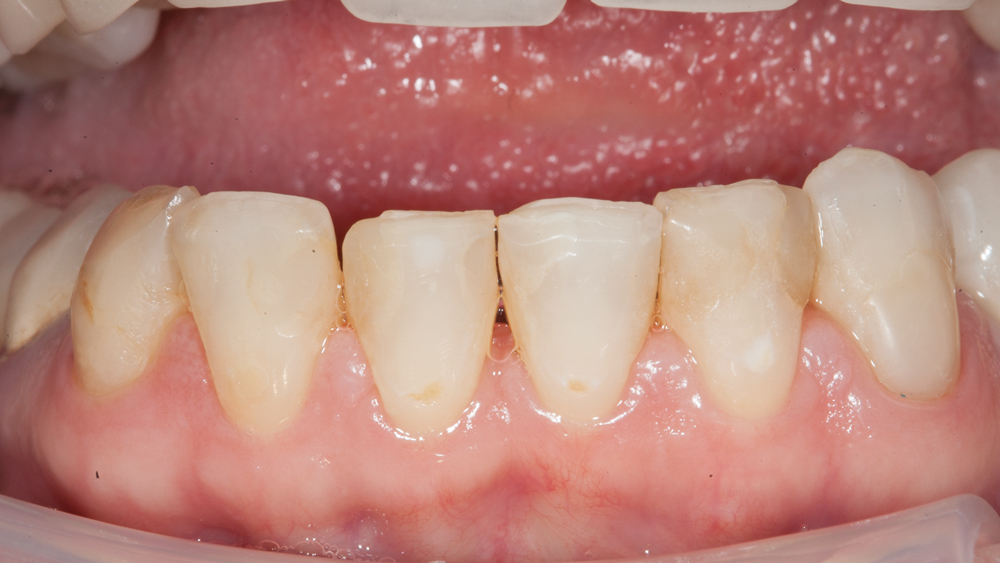
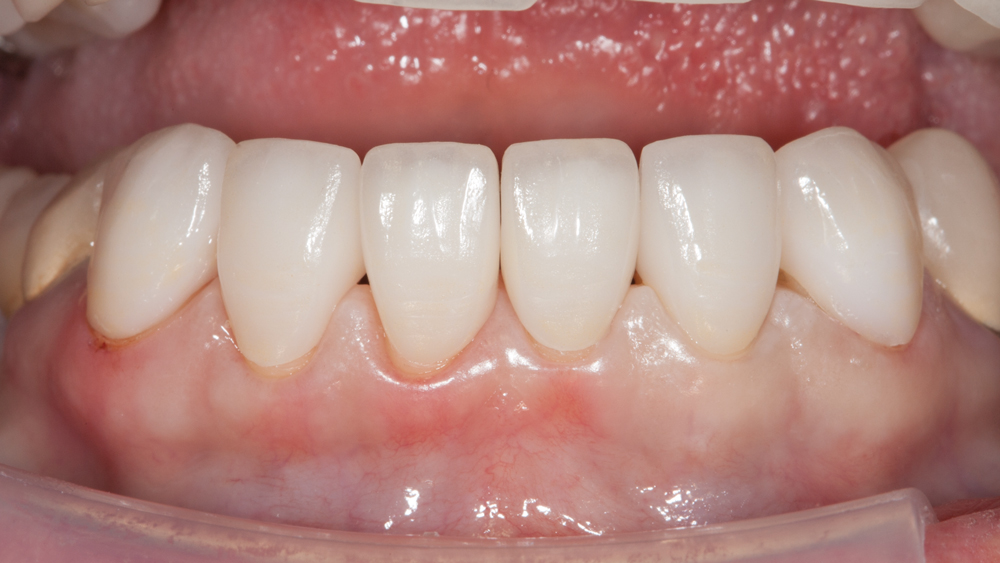
Figures 5a, 5b: Obsidian Fused to Metal crowns offer an exceptional solution for restoring strength and cosmetics in the esthetic zone.
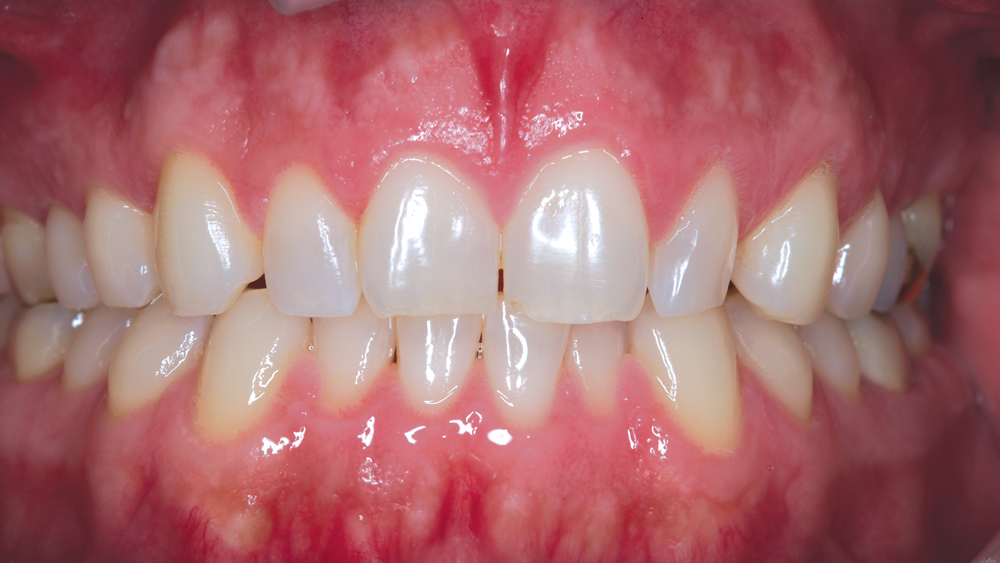
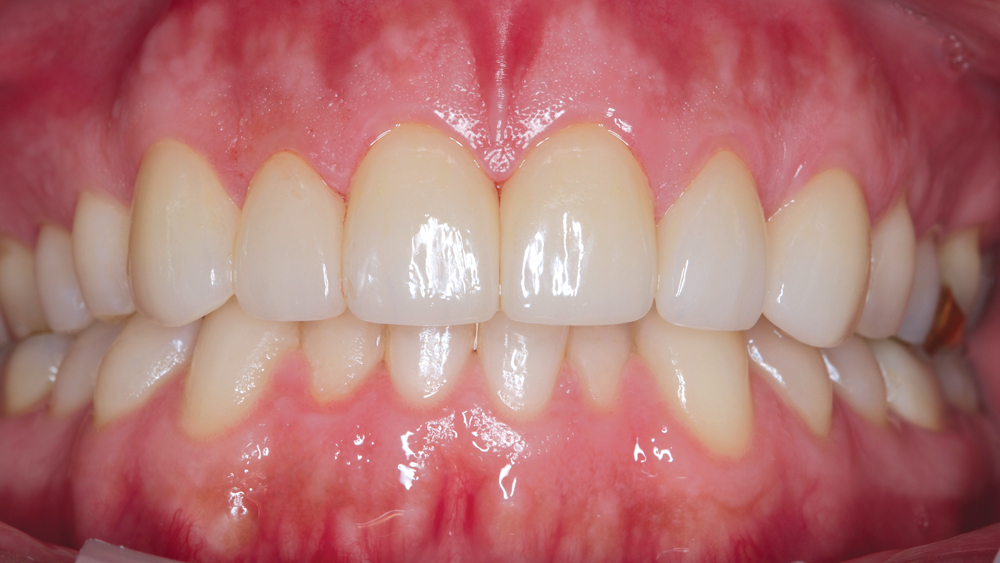
Figures 6a, 6b: The lifelike vitality of Obsidian ceramic makes it an ideal choice to create natural-looking maxillary centrals and laterals.
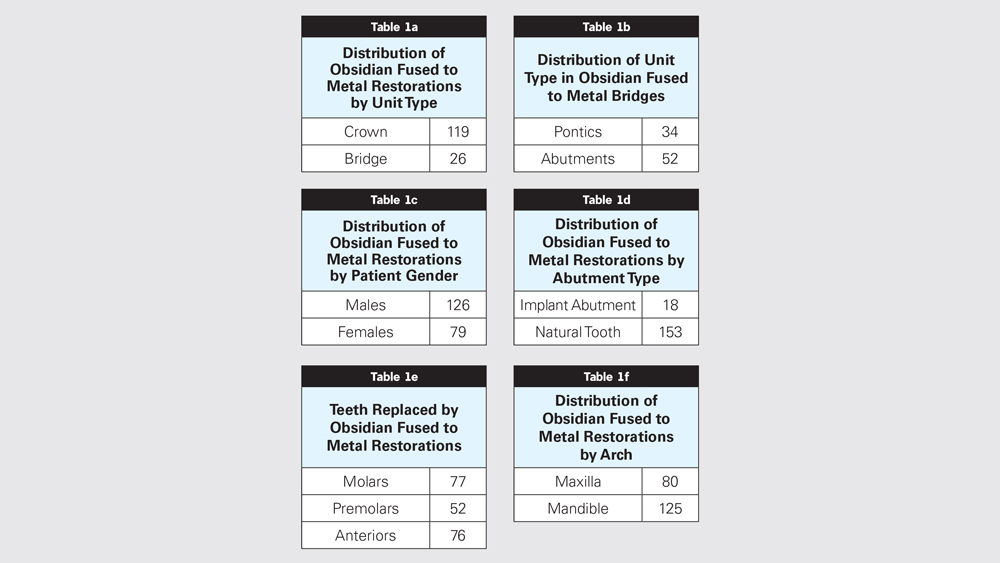
Tables 1a–1f: The distribution of the 205 Obsidian Fused to Metal units placed by Glidewell Dental clinicians. Crown & bridge restorations were used in a wide variety of case types, both implant and conventional, across all areas of the mouth.
None of the restorations placed so far have reported a failure due to fracture or chipping of the restoration, and none have reported any other complication requiring replacement. Thus far, none of the patients have reported sensitivity or any other issues with the restorations. The Obsidian Fused to Metal restorations placed at Glidewell Dental have a 100 percent success rate, further suggesting that Obsidian Fused to Metal offers a viable, strong, chip-resistant and beautiful solution for cases that would normally require conventional PFM restorations.
References
- ^Quinn JB, Sundar V, Parry EE, Quinn GD. Comparison of edge chipping resistance of PFM and veneered zirconia specimens. Dent Mater. 2010 Jan;26(1):13-20.
- ^Joshi G. Mechanical Behavior of Lithium Silicate Press-on-metal Restorative System [internet]. Los Angeles: 2016 AADR/CADR Annual Meeting [cited 2017 May 8]. Available from: https://aadr2016.zerista.com/event/member/237775.
- ^Örtorp A, Jönsson D, Mouhsen A, Vult von Steyern P. The fit of cobalt-chromium three-unit fixed dental prostheses with four different techniques: a comparative in vitro study. Dent Mater. 2011 Apr;27(4):356-63.
- ^Kim KB, Kim JH, Kim WC, Kim HY, Kim JH. Evaluation of the marginal and internal gap of metal-ceramic crown fabricated with a selective laser sintering technology: two- and three-dimensional replica techniques. J Adv Prosthodont. 2013 May;5(2):179-86.
- ^Abou Tara M, Eschbach S, Bohlsen F, Kern M. Clinical outcome of metal-ceramic crowns fabricated with laser-sintering technology. Int J Prosthodont. 2011 Jan-Feb;24(1):46-8.
- ^Ucar Y, Akova T, Akyil MS, Brantley WA. Internal fit evaluation of crowns prepared using a new dental crown fabrication technique: laser-sintered Co-Cr crowns. J Prosthet Dent. 2009 Oct;102(4):253-9.