Better-Fitting Partial Dentures
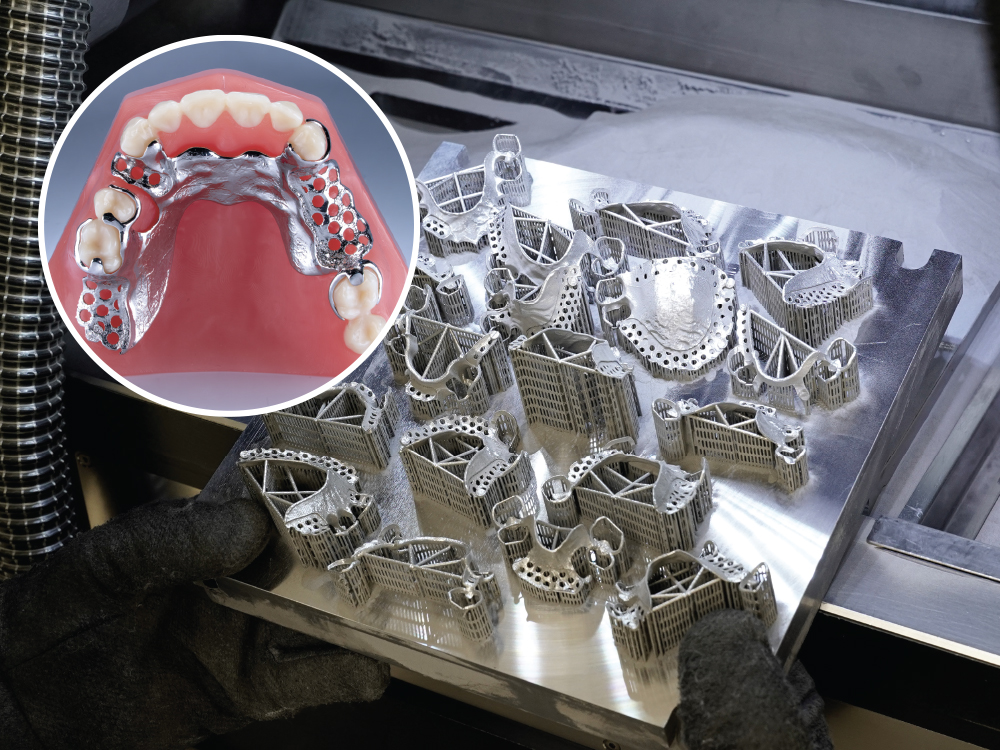
Producing partial dentures that fit comfortably in the patient’s mouth and spread occlusal forces in a physiologic manner is a well-known challenge for dentists and technicians alike. Fortunately, recent advances in laboratory technology have made the production of partial frameworks more accurate, leading to greater patient comfort, shortened seating time and, consequently, a much higher rate of patient acceptance. Key among these advancements is a process called “Selective Laser Melting” (SLM) that combines digital design and 3D printing for a level of predictability that was never before achievable.
THE TRADITIONAL METHOD
The traditional method of framework fabrication for partial dentures utilizes the lost wax casting technique, requiring a physical wax-up, production of a refractory model and high-temperature burnout followed by centrifugal casting. The centrifugal force on the alloy, consisting of metals with different melting temperatures, results in impurities such as burnt particles and gaseous inclusions which increase fragility. After casting, the metal frame is subject to further distortion from the forces required to deflask the framework and the extensive abrasives used in finishing.
WHAT IS THE SLM METHOD?
The SLM method eliminates the need for a manual wax-up and the creation of a refractory model. Instead, after the initial model is poured and scanned, the data is sent to a CAD designer who designs the framework using custom software.
This CAD process allows the creation of highly precise clasps and other delicate elements that often distort when fabricated with the lost wax technique.
The design is then sent to the SLM machine for manufacture. Much like a 3D printer, the SLM machine builds up the framework layer-by-layer, melting and fusing 40-micron-thick layers of metallic powder together to form the desired shape.
The result of this manufacturing technique is a chrome-cobalt alloy that is much denser than in the casting method, leading to a framework that is much easier to polish. In fact, the need for manual finishing is reduced by 30% using SLM, and the precise shape of the partial directly from the SLM unit further reduces the need for grinding and finishing.
The SLM partials emerge from the automatic polishing unit in an hour with a brilliant finish, eliminating the potential for distortion of the partial due to manual polishing pressure.
A MAJOR IMPROVEMENT
The SLM technique provides a better solution for manufacturing precision partial denture frameworks. The reduction of variables from manual processes combined with the automation of laser sintering creates an unprecedented level of precision. The SLM process reduces the amount of time it takes to produce partial frameworks and provides a much more precise, better-fitting partial denture.
Selective laser melting produces better-fitting partial frameworks and eliminates issues that are common with the traditional lost wax technique.