3D-Printed Oral Appliances for the Win!
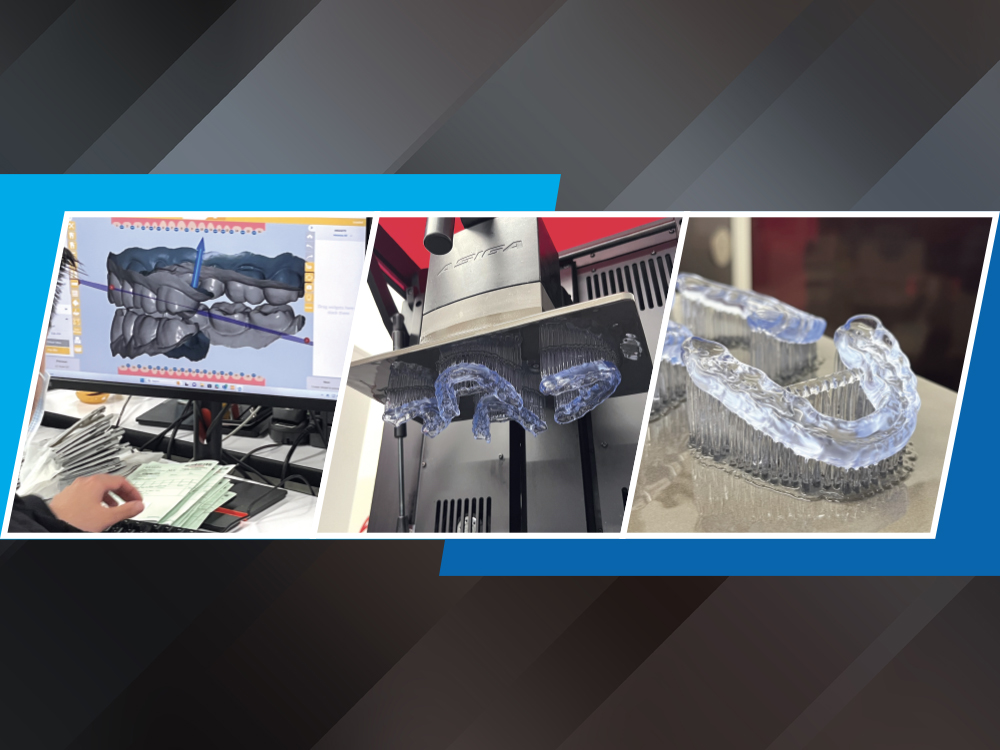
In 1998, I graduated dental school and purchased a practice limited to the diagnosis and treatment of TMJ disorders in my hometown of Boise, Idaho.
I’m sure you’re thinking, “Why would anyone in the world do such a thing? A TMD-specific practice located in Boise?” And that is a story you can ask me about in person someday.
But in that limited practice, we fabricated all of our own splints — mandibular day splints and maxillary nightguards — and a few years into practice, we started making sleep apnea appliances as well. We did it all using the “salt and pepper” technique with cold-cure acrylic and ball clasps for retention. Our office always smelled like a nail salon, but we became nose blind to it quickly. I’m not sure how many brain cells I lost working with acrylic like that every day, but I’m sure it was more than I have to spare.
Eventually, we started using “suck down” thermoforming machines, and this made the process faster and better. The discs were of uniform thickness, so we had more uniform appliances with a lot less work. We still had to add acrylic to build the occlusion and would use articulators to get the correct maxillomandibular relationship.
Then, we got the Erkoform machine, with the Occluform attachment (Glidewell Direct), that is still sold. This was a game changer! In the vast majority of cases, we were able to fabricate the splint or nightguard and build the occlusion into the thermoformed material without the need of an extra step of adding acrylic.
The best oral appliance is the one the patient will actually wear!
The only problem with this method is that sometimes we needed to use a fairly thick material so it would be tall enough to have occlusion. Otherwise, we’d have to build up the posterior with acrylic, defeating the purpose of having the Occluform attachment, or use a thicker material in order to have occlusion and then have to grind off all of the extra on the facial and lingual so that the appliance didn’t feel too thick to the patient.
Fast forward 25 years, and these techniques are still how the majority of splints and nightguards are made to this day.
Until now.
3D printing has been around for years, and we are no longer in the “bleeding edge” time of this relatively new technology. Several years ago, my practice partner and I were on that bleeding edge, and bleed we did, remaking almost all of the appliances that had been printed and giving the patient traditionally fabricated appliances after the printed appliances failed.
But a bunch of super smart engineers, material chemists and lab techs have put their heads together and made 3D printing not only predictable and reliable but, in many ways, superior to the “old school techniques.”
I believe that there is one main factor in determining the best oral appliance for our patient, and this belief applies to nightguards, sleep appliances, day-use splints and even sports mouthguards. The best oral appliance is the one the patient will actually wear!
Pretty simple.
Or is it?
In my experience, the art in the “art and science of treating patients with temporomandibular disorders, sleep apnea or protecting the patients’ teeth from nocturnal parafunctional activity” is determining what appliance the patient is most likely to use on a regular basis.
As such, comfort tends to be the most important factor to consider. The efficacy of the appliance will only matter if the patient will use it — so comfort is king.
After fitting literally tens of thousands of patients with oral appliances, and mentoring hundreds of dentists who are doing the same, I’ve found a few things that are critical when it comes to the patient finding the appliance comfortable. I’m sure you’ve noticed these attributes as well.
The thinner the nightguard or sleep appliance, the better.
1. THICKNESS OF THE APPLIANCE
As I often say to my patients, “If you had a hair in your shoe right now, you would never notice it. But if you had a hair in your mouth, you would for sure notice.”
Our mouths are incredibly sensitive to anything out of the ordinary intruding into the already limited space. The thinner the nightguard or sleep appliance, the better. I have yet to have someone ask if I can make the appliance a little bulkier. On the other hand, I’ve had innumerable patients who struggled to use the appliance at first but were able to wear it just fine after we shaved off what seemed to be an almost microscopic amount of acrylic.
The thickness of the appliance also impacts the patient’s ability to close their lips around it. When a patient can’t easily close their lips with the appliance in place, the odds of them using the appliance are nearly zero — unless they’re already a mouth breather, which we certainly don’t want to encourage.
3D-printed appliances are as thin as possible while keeping the appropriate strength and tend to be less brittle than a salt-and-pepper-fabricated, acrylic appliance of similar thickness. Thermoformed appliances tend to be a little thicker, and for a lot of patients, that 0.5 mm is the difference between wearing it and leaving it in their drawer.
2. NATURAL CONTOURS
In addition to the overall thickness, where the appliance is thick also makes a difference. Our tongue is accustomed to the contours of our teeth. When that contour is altered, many people will react in a seemingly disproportionate way. You’ve certainly experienced this with crowns and fillings. Your dental perception is that the restoration is exactly the same size as what was previously there, but the patient complains about how thick it is.
Thermoformed appliances will have thicker and thinner parts due to the nature of taking a homogenous thickness disc and then thermoforming it over the teeth. Technicians may attempt to contour the appliance, but getting it uniformly consistent is very difficult and time consuming.
A 3D-printed appliance, by contrast, can follow the natural contours of the teeth perfectly and be of a consistent thickness, which “alarms” the patient’s tongue much less.
3. FINISH
As you have also experienced, many patients are very sensitive to the slightest bit of roughness. If the restoration or appliance isn’t as smooth as their enamel, they’re likely to notice.
Traditionally made appliances are smoothed out using pumice wheels and finishing discs. The problem is that patients seem to notice the tiniest not-glass-smooth area, particularly on the lingual and occlusal. If a patient finds such a rough spot, they may find that “their tongue constantly plays with the spot,” which usually means they’ll stop wearing the appliance until the spot can be smoothed out.
3D-printed appliances still need to be finished, but the procedure is different from traditional methods. When we use 3D-printed appliances, we do our best not to adjust the external surface of the appliance if at all possible because we know that getting that spot or area back to the same level of smoothness will be difficult.
4. FIT
Most patients don’t know what a good-fitting appliance means; they just know if it hurts. This is another challenge with traditionally made oral appliances. Obviously, the line of draw and heights of contour are going to vary from patient to patient. The combination of line of draw and heights of contour are likely as personal to that patient as their fingerprints. Every appliance that is custom made is literally one-of-a-kind! The 3D-design method is able to take into account the unique line of draw and heights of contour in ways that are impossible with a thermoformed appliance.
Through a combination of AI and expert designers, the fit of full-arch appliances is now better than ever. And while this won’t tend to be the most important thing to the patient, it’s incredibly important to you as their dentist because you want to avoid any tooth movement that could be induced by a sloppy fit (think orthodontic aligners, but the movement isn’t on purpose). As long as you provide excellent scans, the fit of a 3D-designed-and-printed appliance will be as perfect as it can be, taking into account all of those unique lines of draw and heights of contour.
The fit of full-arch appliances is now better than ever.
5. HASSLES
This last point is mostly for us as the dentists, but it impacts the patient as well.
None of us like to have things remade. Glidewell has seen a significant decrease in remakes of their 3D-printed nightguards and sleep appliances compared to those made using traditional methods. The attention to detail is the same for all of the appliances fabricated, but for the reasons outlined above, patients are just more likely to complain about the feel of the non-3D-designed-and-printed appliances. The “send it back to the lab” solution is a common one. Of course, this results in unproductive chair time for you and an extra trip into your office for the patient. Heaven forbid that there is a similar issue the second or the third time. I think we’ve all been there. 3D printing of appliances doesn’t make all of those issues go away, but the internal data at Glidewell shows fewer remakes for the 3D-printed devices, which equals more productivity and fewer hassles for you.
I’m very excited about the implementation of 3D design and printing of oral appliances. Maybe someday we’ll be making some of these appliances in our office, but without the office smelling like a nail salon. Of course, when that time comes, we’ll need the design help from a talented technician at Glidewell and guidance with what printer and resin to use. But for now, I’m fine waiting the three days to get the appliance back from the lab and letting others do all the work.
ERKODENT is a registered trademark of ERKODENT Erich Kopp.