Product Spotlight: Inclusive® Prosthetic Components
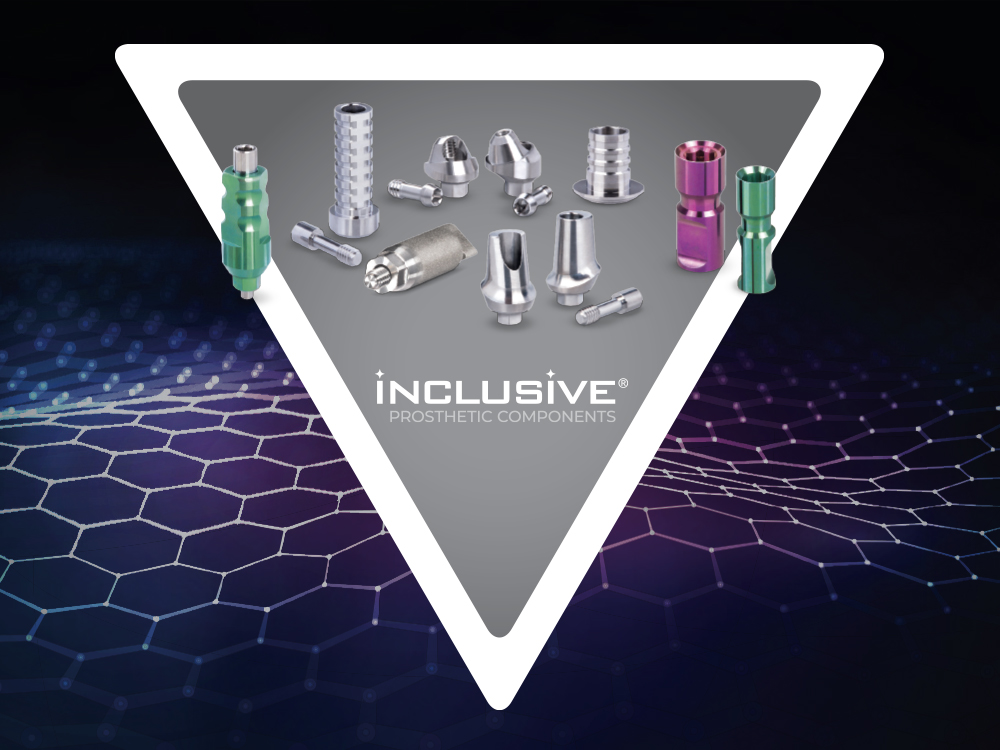
When Jim Glidewell founded his dental lab in 1970, the goal was to make premium dentistry as accessible as possible. Decades later, this was the driving force behind the Inclusive® line of prosthetic components, which features parts compatible with most implant systems on the market, all for more affordable prices than those of their original equipment manufacturers (OEMs).
In addition to helping dentists lower their costs on commonly used parts like titanium screws and the full range of abutments, Inclusive Prosthetic Components are essential to Glidewell’s ability to offer predictable, flat-rate lab fees for implant restorations — whereas other labs are beholden to the high prices that implant companies charge.
COMPATIBILITY IS KEY
The Inclusive Prosthetic Components line is constantly expanding to add parts compatible with the most popular implant systems. This is in addition to the 17 systems already supported by Inclusive Prosthetic Components, including NobelReplace®, Straumann® Bone Level, Zimmer Dental Screw-Vent® and Hiossen® HG System among others. In 2024, the Inclusive line has already grown to include BioHorizons®, MIS® C1 and Straumann® Bone Level SC, with many new line extensions coming soon.
The range of Inclusive Prosthetic Components is constantly expanding to offer components compatible with the most popular implant systems on the market.
ENGINEERED TO CONTROL COSTS
Inclusive Prosthetic Components are designed to offer the same functionality and durability as OEM parts, while remaining as affordable and accessible as possible. This guiding principle enables clinicians to control costs without cutting corners when it comes to the level of care they offer their patients.
INCLUSIVE PROSTHETIC COMPONENTS
Abutments
- Temporary
- Titanium
- Titanium Esthetic
- Healing
- Bite Verification Cylinders
- Scanning
- Analogs
- UCLA
- Multi-Unit
- Locator®
Transfer Copings
- Digital
- Conventional
Implant Analogs
Titanium Screws/ Guide Pins
The availability of lower priced components such as titanium scan bodies and transfer copings enable dentists to reduce costs without sacrificing quality for the full range of restorative procedures. Glidewell stands by the quality of each prosthetic component. If an Inclusive prosthetic component is used for an implant and that implant fails, Glidewell will replace it with a Glidewell HT™ Implant free of charge should the original implant manufacturer refuse to stand by their warranty.
PRECISION MEETS UNMATCHED SCALE
The precision manufacturing operations at Prismatik Dentalcraft, Inc. — the manufacturing arm of Glidewell — are what make the entire Inclusive line of implant products possible, drawing on over 50 years of clinical experience and expert craftsmanship. By utilizing the many advanced milling machines that Glidewell has invested in over the years, the scale of production is unmatched in the laboratory industry. This allows the lab to pass along the cost savings that come with in-house manufacturing and vertical integration to clinicians across the country.
At Prismatik Dentalcraft’s manufacturing facility in Irvine, California, technicians and computer numerical control (CNC) machines work in unison to produce each implant component on-site. They operate two shifts a day, five days a week, manufacturing a range of products from analogs to implants. The teams produce a new part roughly every nine seconds, totaling about two million components over the course of a year. To keep pace with production, a room full of Rhinobar® bar feeders (Lexair, Inc.; Lexington, Kentucky) steadily supply Citizen and Tornos® Deco machines with 12-foot titanium alloy rod stock, from which new implant parts can be milled every 80 seconds to five minutes, depending on the type of component being produced.
After milling each component, the team grit blasts pieces as required, while other parts proceed straight to the cleaning process. This is also where certain implant components, such as those belonging to the Inclusive Mini Implant System and Glidewell HT Implant System (formerly known as the Hahn™ Tapered Implant System), are anodized with colors corresponding to their size.
The team packages all Inclusive parts in an ISO 8 cleanroom to reduce and stabilize bioburden while maintaining a sterile environment. Each implant undergoes an additional sterilization process offsite before delivery.
Visit glidewelldirect.com to explore Glidewell’s growing assortment of Inclusive Prosthetic Components. For the full range of implant restorations available through Glidewell’s lab, visit glidewell.com/implant-solutions.
Inclusive is a registered trademark of Prismatik Dentalcraft, Inc. All third-party trademarks are property of their respective owners.