R&D Corner: I Wish They All Could be California Mills
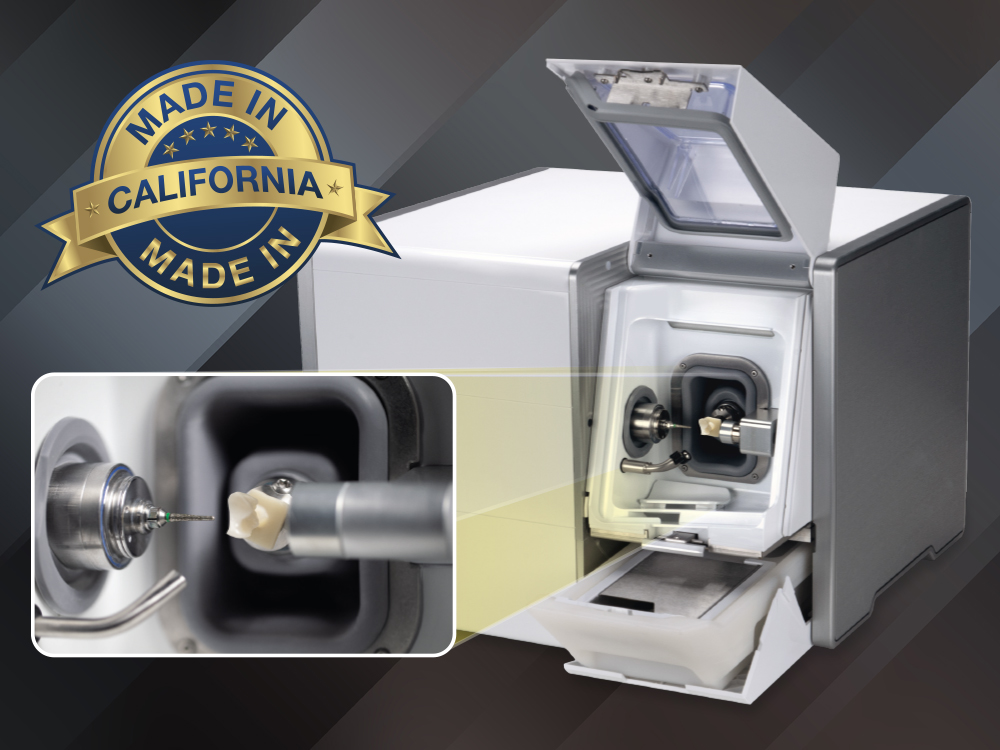
A highlight of any Glidewell Symposium is a tour of our campus. And as attendees are sure to notice while walking through our 800,000-square-foot campus, we do a lot of manufacturing on site — a reflection of our core tenet of vertical integration. A testament to the success of this principle is the production of the fastmill.io™ In-Office Mill. Here, we explore the story behind the mill, and the team that makes it possible.
WHY MANUFACTURE IN CALIFORNIA?
It’s no secret that many companies in the dental industry outsource their manufacturing to other companies, or to overseas facilities. Whether that decision stems from the benefit of reduced material and labor costs found overseas, or to avoid the complex logistics of in-house manufacturing, the fact remains that outsourcing is typically cheaper. While walking through the aisles of our bustling production facility, many tour guests have asked us: Why manufacture on some of the most expensive real estate in the country?
“Our decision to manufacture in-house boils down to quality control and communication,” said Jishan Mansuri, mechanical assembly supervisor at Glidewell, who oversees the manufacturing of the mill. “We designed and engineered the fastmill.io ourselves. To produce a chairside mill that continuously performs at the caliber our doctors expect, we also had to manufacture it ourselves.”
The mill is not just the sum of its material parts. With sophisticated software and continuous optimization testing, it is a perpetual work in progress, with its success depending on the efforts of many departments, not just engineering. One recent example of this collaboration is in the successful reduction of production time by 25%. “If we outsourced, we would lose the streamlined communication between our departments,” Jishan added. “Our machine shop, customer technical support team, R&D department, engineers, and software developers are all here at the Glidewell campus. If there’s ever a problem in our workflow, the departments can come in and keep the process flowing.”
MAKING THE MILL
At the fastmill.io assembly facility, Jishan leads a team of 20 mechanical assemblers who meticulously hand-assemble each component of the mill. “The craftsmanship of the mill is incredibly unique,” he noted. “There are some mechanical tools involved, but everything is hand touched and hand assembled. That’s the level of detail that this piece of equipment demands.”
The process begins in the machine shop, where the legs, plates, and baseplate are fabricated in-house from high-grade aluminum billet. This frame is then used to house 14 separate assemblies, which together constitute a completed mill. These subassemblies are made at a designated station on the production floor, and a technician is tasked with completing the build of that subassembly.
Once these steps are completed, the fastmill.io mill is hand assembled. Jishan explained that “We believe in traceability. If there’s ever an issue, we want to identify precisely how to correct it — and we have systems in place to be able to do that. That’s how we’re able to have such strict quality control.”
Once the mill is assembled, it undergoes rigorous testing through five dedicated stations and a 348-point inspection process, which includes software and material testing. “If we detect any point of failure, we can trace it to the source to find out exactly what part needs to be replaced. Then, we start the testing process all over again. That type of detail can only be assured by doing it ourselves,” Jishan added, underscoring their commitment to quality and precision.
Our decision to manufacture in-house boils down to quality control and communication.
MASTERING THE ASSEMBLY PROCESS
The training process to become a mill assembler varies, but typically takes several months. As Jishan explained, “There isn’t a defined timeline for training. The answer is however long it takes for the individual to master the process.” New hires start at one of the simpler assembly stations and gradually progress to more complex assemblies as they develop proficiency. This method ensures that everyone becomes fluent in all steps of the assembly process, understanding exactly what parts go where and how the entire mill fits together.
Jishan emphasizes the rigor of their process, stating, “Overseas production would mean relying on employees in a different country. This is how we ensure we can meet demand without delay.”
The fastmill.io story is about unwavering commitment to quality, precision and communication.
The fastmill.io story is about unwavering commitment to quality, precision and communication. That’s why Glidewell invites event guests on a tour, so they can see in person how Jishan and his team are fulfilling the promise of empowering doctors and their everyday restorative routines. “One of my favorite parts of this job is when doctors stop by and meet the people who make the mill,” he admitted. “It adds a personal touch to what we do, and inspires us to never stop improving.”