Why I Prefer the glidewell.io™ In-Office Solution over Other Milling Systems
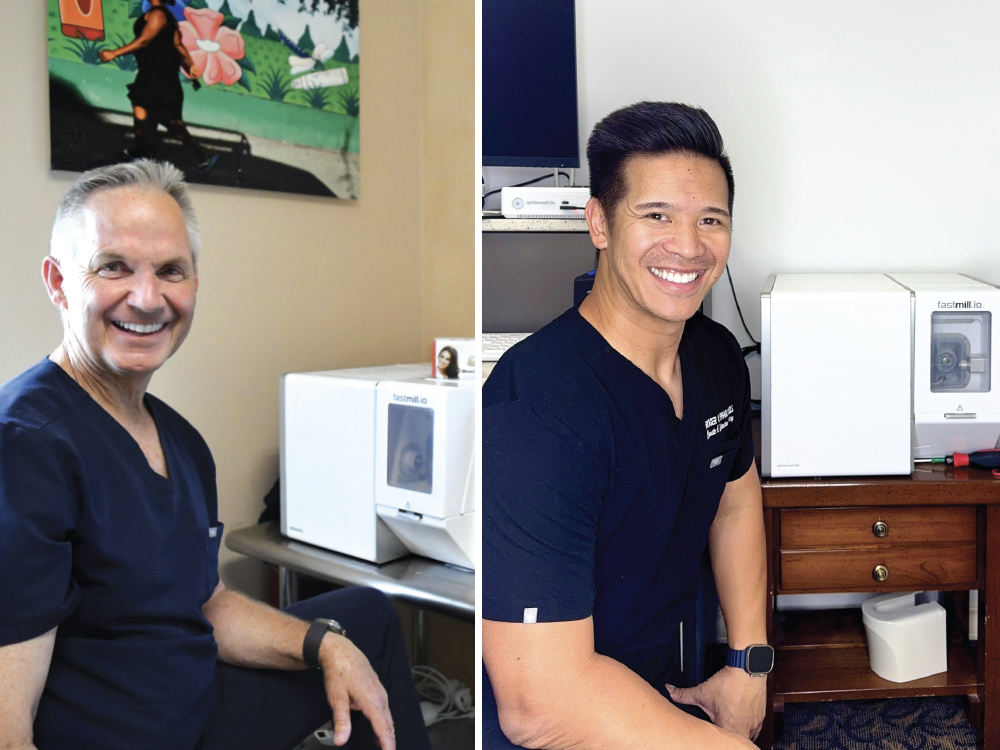
Cary LaCouture, DDS
Burning Tree Family Dentistry
Franktown, Colorado
In March 2018 after having some experience with a CEREC® milling unit, I had my first fastmill.io™ In-Office Mill installed. As part of the installation process, a team of experts from Glidewell in Orange County, California, came to my one-stoplight town of Franktown, Colorado, to ensure everything went smoothly. In fact, they stayed for several days, testing connections, training staff and providing technical support as we produced our first crowns.
This was far better than the support I received with my previous mill, which I purchased from one of the major dental distributors. In fact, with my previous mill, even knowing whom to contact for support was a challenge.
Everyone in my office was trained at the same time. We began milling on the second day of training and have not stopped in the six years since.
The glidewell.io team may have left Franktown after our introductory session, but the quality of support and training we continue to receive remains as thorough today as it was on Day 1. Glidewell continuously ensures we are properly trained on any software or hardware updates.
Dentists want a digital CAD/CAM system that grows with them. The glidewell.io™ system does exactly that for my practice. We have taken advantage of product updates and the many webinars Glidewell offers so we can stay as knowledgeable and as current with our mill as possible.
The benefits to patients have become so clear that I now get referrals specifically asking for in-office restorations. Whether your practice is in a bustling metropolis or a town with a single traffic light, Glidewell’s training and continued support made adding a mill an easy and rewarding decision.
Roger Pham, DDS
Auburn Dental Center
Bakersfield, California
Every minute I save thanks to the fastmill.io™ In-Office Mill’s intuitive software enables me to spend more productive time with my patients. And the minutes add up. I have found it easy to come up with design proposals that require little-to-no adjustment. With CEREC, I would be fussing with the design for 5-to-10 minutes. With glidewell.io software, the anatomy is on-point and I sometimes touch up the contacts a bit. From there, I go straight to milling.
The fastdesign.io™ Software and Design Station uses CrownAI™ and MarginAI™ technology to generate ready-to-use designs. Glidewell’s digital restoration database, which utilizes data from millions of crowns designed at Glidewell, provides the data for the artificial intelligence. The process takes just seconds and, in my experience, comes up with better proposals than other design software.
The reliability I have seen from the fastdesign.io software provides me with the confidence to focus on other responsibilities. Usually, I have my assistant start the design process and call me when they have the margins marked. If the margins are good, I will let them take over while I do something else, like a hygiene check. Because they’ve attended the Glidewell training, they know how to design. I’ll make a final check, then they are ready to send to the mill.
The software’s not complex, but it is still new to me. If I can’t figure something out, I can call Glidewell and get support quickly. Then, we’re up and milling in no time. The mill is as user-friendly as the software and contributes to the time savings. In particular, the chairside workflow for producing restorations from fully sintered zirconia blocks has fewer steps than milling with pre-sintered zirconia. I save five minutes on design, then I save more time not having to sinter the crown. With CEREC, I would tell patients we’ll be done in about an hour-and-15 minutes. But when using the fastmill, I’m confident when I tell patients the process will take 45 minutes.
A half-hour is a considerable time savings, especially adding up that saved time over multiple cases. That is what dentists want: to be efficient with our time. And no patient wants to be in the chair any longer than necessary.
CEREC is a registered trademark of Dentsply Sirona.