By the Numbers: Glidewell Implant Manufacturing
With on-site vertical integration at the core of manufacturing processes at Glidewell, the lab can standardize restorative procedures and reduce costs for dentists while also ensuring that every component meets the highest standards for quality and precision. Specifically, the implant manufacturing team at Glidewell researches and develops new products, makes improvements to existing products and obtains FDA 510(k) clearances.1 At a glance, here are just some of the numbers related to our implant manufacturing process.2
180,000
Average number of individual parts that the Glidewell implant manufacturing team produces per month.
978
Unique Implant Component Parts Made at Glidewell
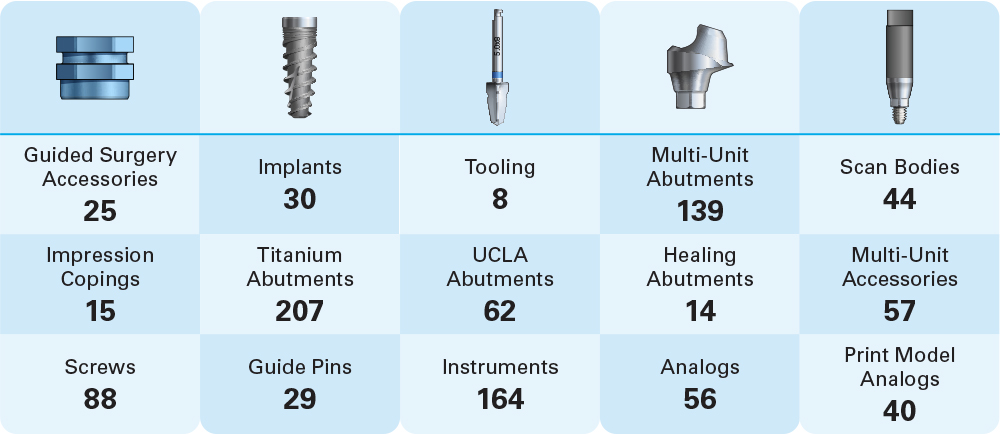
19
Implant Systems
Our components are compatible with 19 different implant systems and over 80 connections.3 In the next six months, we are expanding compatibility to an additional 15 systems pending FDA 510(k) clearances.
100%
In-house Production
All of our implant components are produced in our Irvine, California, ISO-certified manufacturing facility.
60
Employees that comprise the implant manufacturing team at Glidewell.

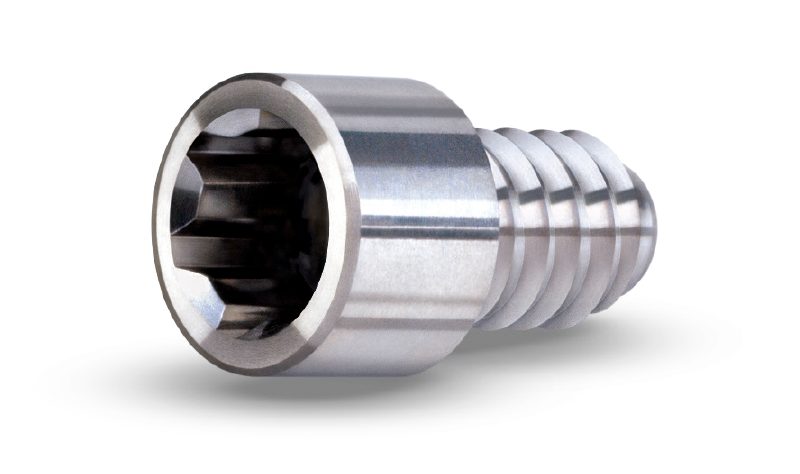
3.5 mm
Smallest Part Manufactured
Length of the Inclusive® Multi-Unit Prosthetic Screw, the smallest part made by the Glidewell implant manufacturing team.
18.93 mm
Largest Part Manufactured
Length of the Inclusive Titanium Abutment Blank, the biggest part made by the Glidewell implant manufacturing team.
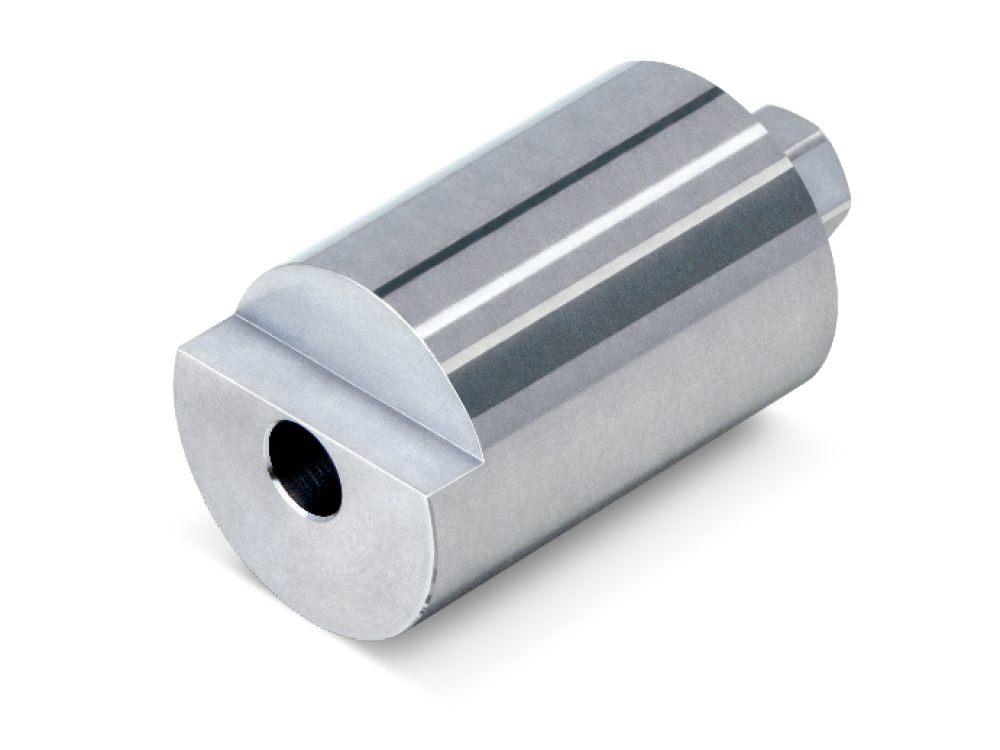
834%
Increase of screw-retained crowns produced by Glidewell from 2014 to 2022, with most of the restorations produced using titanium bases manufactured at Glidewell.
75,000+
Number of custom abutments fabricated using Prismatik blanks by Glidewell in 2022.