Interview with Justin Chi, DDS, CDT
Dr. Justin Chi is director of clinical technologies at Glidewell Dental, where he assesses, validates and provides clinical insight on the latest CAD/CAM technologies and materials created by the company’s Research & Development department. Prior to joining Glidewell Dental in 2015, he graduated from the Herman Ostrow School of Dentistry of USC, received a degree in dental laboratory technology from Louisiana State University Health Sciences Center School of Dentistry, and worked at E4D Technologies as both a dental technician and clinical educator. In this interview, Dr. Chi recaps how he made the transition from dental lab work to dentistry, describes some of the products he’s helped develop at Glidewell Dental, and provides insight on using CAD/CAM technology.
DR. NEIL PARK: Your path to becoming a dentist was not typical — you started out as a dental technician. Can you tell me a little bit about your experience studying dental laboratory technology at the LSU School of Dentistry? As I understand it, there are not many dental school-level programs in dental technology right now.
DR. JUSTIN CHI: No, there aren’t. As far as I’m aware of, there are only two, with the other one being in San Antonio. LSU at the time had a two- and three-year dental lab technology program. After two years, you could earn your associate degree, and if you stayed on for a third year, you could earn your bachelor’s. When I started, I had eight students in my class — and I was the only one who went on to the third year. But it was an excellent program. They taught us everything from basic morphology and waxing, to fixed prosthodontics, to removable prosthodontics, and even some orthodontic appliances as well.
NP: Did you get your CDT designation while you were in that program, or is that something you earned afterward?
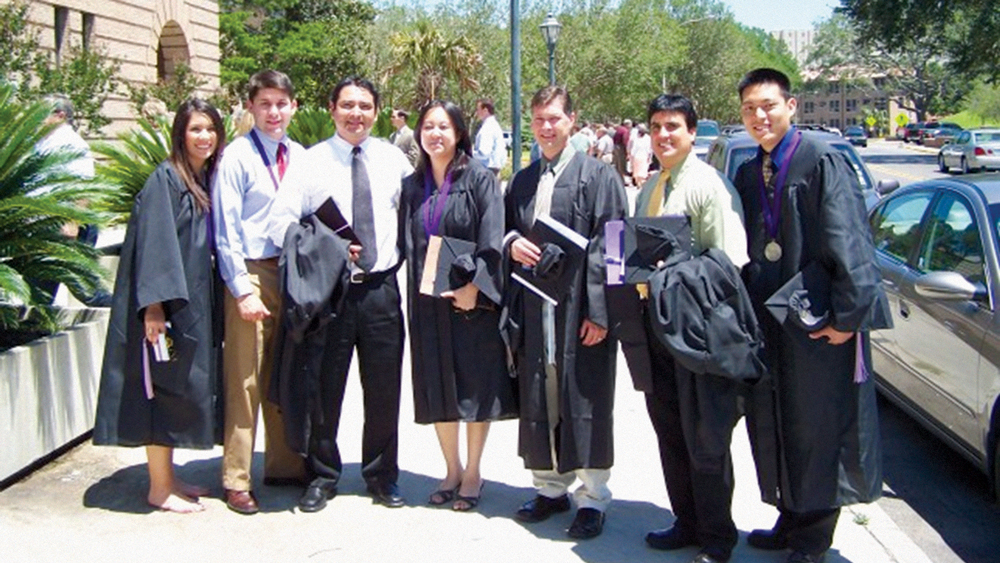
Dr. Justin Chi (far right) earned his Bachelor of Science in dental laboratory technology from Louisiana State University Health Sciences Center School of Dentistry.
JC: I took the CDT tests at the end of my third year. I earned my CDT in crown & bridge.
NP: So what does a young, highly trained dental technician do for a job when he gets out?
JC: I moved from Louisiana to Dallas, where I tried to open my own lab out of my two-bedroom apartment, with one of the bedrooms dedicated to the lab. I had it all set up mainly for fabricating PFMs and gold restorations. At the time, I didn’t know that much about milling machines, so I invested in everything required to create metal copings and fire feldspathic porcelain to create traditional restorations.
NP: And then you found your way into the very early dental CAD/CAM industry, did you not?
JC: I did. Finding clients while I was trying to get the lab business running was really challenging. So while I was establishing my lab, I started searching for supplemental work and came across E4D Technologies. At that time, E4D was trying to get off the ground and they were offering a training position. So I joined their team as a trainer at the end of 2007 and helped implement some of their training materials for new dentists.
With any new technology, there is a learning curve. So training and making sure the dentists start off on the right foot is very important.
NP: In your dental laboratory courses at LSU, did you receive any CAD/CAM training?
JC: At LSU, we did explore CAD/CAM a little bit, using the InLab® production unit (Dentsply Sirona Inc.; York, Pa.) for milling zirconia substructures, on which we would then stack porcelain. We also used Procera® alumina (Nobel Biocare; Yorba Linda, Calif.) to make copings. So we used a little bit of CAD/CAM, but we focused mostly on the fabrication of substructures. When I moved to Dallas and learned more about CAD/CAM and in-office milling machines, I was a bit disappointed because I had essentially just spent so much time learning how to create these restorations by hand, only to then find out that there are technologies available that accomplish the same thing. However, after I began to understand the benefits for both the patient and the practice, I thought it’d be cool to get involved with CAD/CAM.
NP: So you were involved in helping dentists who had purchased the E4D scan and mill system to get it up and running in their practices, right?
JC: That’s right. With any new technology, there is a learning curve. So training and making sure the dentists start off on the right foot is very important.
NP: And not easy.
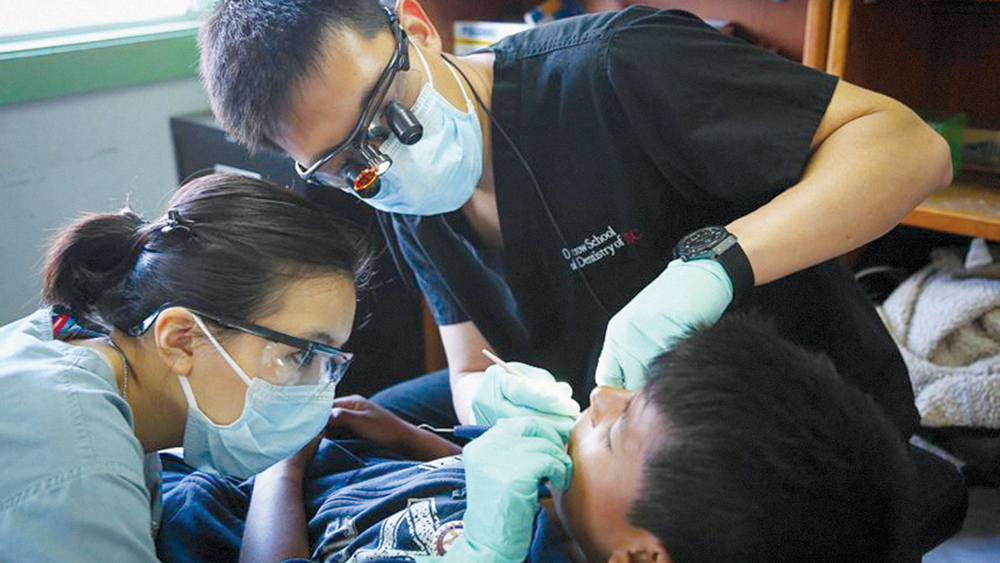
Before joining Glidewell Dental in 2015, Dr. Chi graduated from the Herman Ostrow School of Dentistry of USC.
JC: Not at all. At that time, if a dentist purchased the E4D system, two days of dentist training in Dallas were included, along with a third day of training in the dentist’s office with live patients. We’d usually have two or three patients, and we made sure the dentist was comfortable with the process and able to get started successfully.
NP: What were the biggest hurdles you saw dentists face in getting the system up and running?
JC: Initially, the biggest hurdle was changing the way they prep and having the dentist come to terms with the fact that he or she may not have been taking impressions the ideal way. Essentially, it’s all about proper tooth preparation — creating enough reduction and rounding internal angles. Tissue management is also huge — it’s crucial to relay why it’s so important to create that gingival separation from the tooth. I think oftentimes dentists who just send impressions off to the lab may take the labs for granted and not worry about finding or identifying the margins themselves. But with this technology, either the dentist or the assistant is now searching for the margins, and they run into the same issues dental technicians face every day when they’re trying to trim dies and identify the margins.
NP: Aren’t CAD/CAM technologies disruptive to the practice, to some extent? If you’re a dentist and you prep teeth, create impressions and send them out, make provisionals, and bring the patient back in two weeks and seat the crown, adopting CAD/CAM workflows is a tremendous disruption to how you do things. Was that an issue for a lot of doctors who were trying to put this system into place?
JC: Definitely. Along with learning the technology, they have to learn how to implement it into their schedule. Dentists, in addition to providing care, have a business to run, and most offices are very fast-paced. They’ve likely spent years working to identify and implement an effective workflow based around the traditional two-appointment schedule required for restorative dentistry. And one of the greatest benefits of in-office CAD/CAM is the ability to try in and deliver restorations in the same appointment, which I believe is best for the patient’s health. If you can help the patient in the same day, it benefits everyone. But when it comes to getting to the point where the doctor is comfortable providing quality same-day restorations, every office has to create their own unique solution because they’re distinct in terms of the number of rooms that they have and the way that they’re staffed.
One of the greatest benefits of in-office CAD/CAM is the ability to try in and deliver restorations in the same appointment, which I believe is best for the patient’s health.
NP: One of the workflow issues is that, with single-day dentistry, now you have these wonderful patients hanging around for two or three hours. Neither you nor the patients are used to that, and you’ve got work to do.
JC: That’s right. Initially the appointments can certainly be a little bit longer, so we would always recommend seeing patients right before lunch so you have a little bit of a time cushion afterward, or at the end of the day. Usually after 10 or 15 restorations, most dental practices do get more comfortable. However, with this new technology, it’s all about setting the expectations from the start that this is a shift in terms of not just taking impressions, but also in creating that final restoration. So the disruption is there, but I really commend those dentists who stick with it and can now provide that service for their patients.
NP: The technology certainly has come a long way since those early days. So you were a trainer for E4D helping dentists to incorporate this new technology — and then you decided to go to dental school. What persuaded you to make that leap?
JC: I spent about three years training dentists on CAD/CAM tools across the U.S. and even in Europe. Time and time again, watching interactions between dentists and patients, I saw how amazed patients were by this technology. These were patients who, in the past, would have had to go through the whole ordeal of getting re-anesthetized if they received crowns, so to see the excitement on their faces when they found out they could actually get the restoration in a single appointment really inspired me. And each time I saw these interactions, I really wanted to be a part of the clinical side.
NP: So then you were accepted to the University of Southern California. Did you work with CAD/CAM technology during your time there?
JC: Yes. In those four years at USC, I actually continued to provide CAD/CAM training and I even taught some of the faculty. They did have E4D, among several other CAD/CAM systems, so it was fun interacting with them and even helping with some of their personal cases.
NP: Were most of the students at USC exposed to these systems?
JC: Yes, in our second year. In pre-clinic, we ran through some cases using the CEREC® system (Dentsply Sirona Inc.) and we were able to fabricate a couple of onlays. Once we got to the clinic floor, we had onlays created for us, but we mostly just observed the faculty doing the scans and then someone would design and mill them out for us. Although we were not performing the functions ourselves, we at least were actually seeing how a CAD/CAM restoration was being performed. So it was a little bit of exposure, although we didn’t see the process from start to finish.
NP: That’s still more exposure than students at most dental schools get.
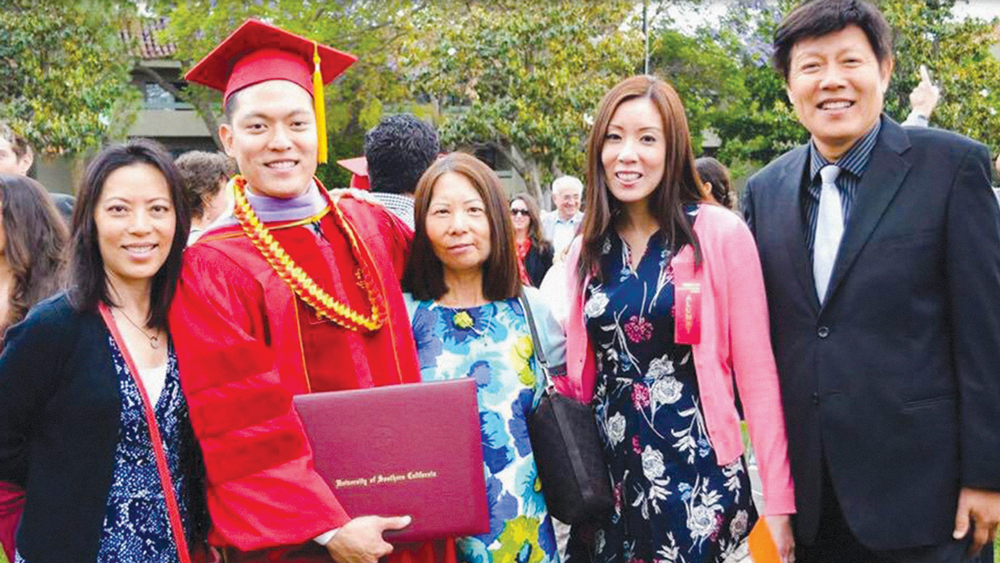
Dr. Chi with his family, after receiving his DDS degree from USC.
JC: Definitely. More and more schools today are adopting the technology and seeing the value in it. When I was at E4D, we trained students at Baylor University, and we even trained faculty at Midwestern University and the University of Missouri-Kansas City. So it was a great experience to see the dental schools getting into this newer technology.
NP: Now you’re director of clinical technologies at Glidewell Dental. How did that happen?
JC: I first met Jim Glidewell a couple of years ago through our mutual friend Dr. Dave Wilhelm, a prominent dentist based in Newport Beach, California. I met Dr. Wilhelm when I provided training to his office during my third year of dental school. We stayed in touch, and he shared my background with Mr. Glidewell, who invited us over for a tour of his company. After I graduated, I got the opportunity to help out with the development of CAD/CAM technology at Glidewell Dental.
NP: We’re really glad you ended up here — you’re an important part of the team. So tell us a little bit about what you do here.
JC: Sure. It’s always exciting — there’s always something different going on. We work very closely with the Research & Development department, testing new materials and doing research on long-term studies. There’s some very exciting stuff coming down the line.
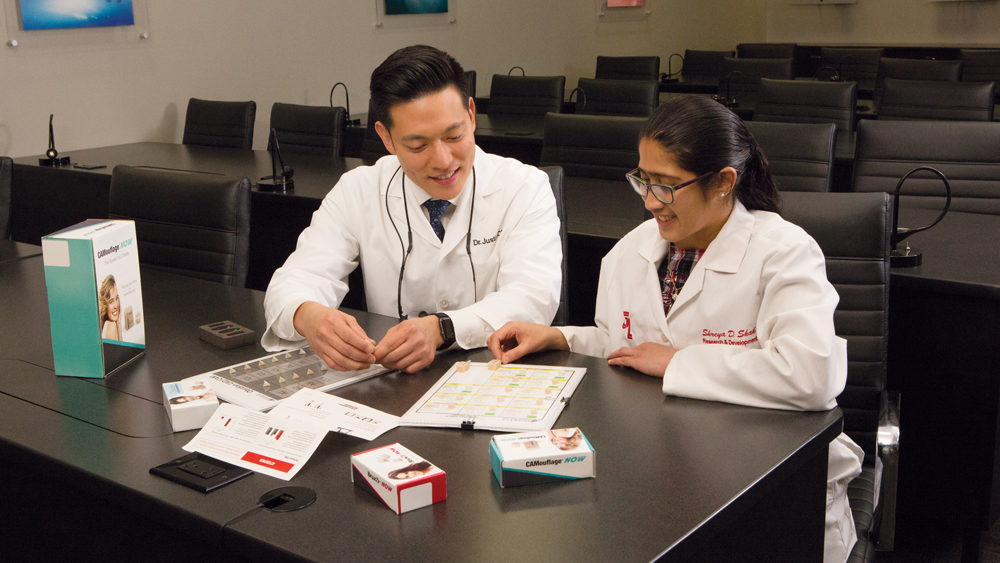
Dr. Chi is director of clinical technologies at Glidewell Dental, where he works with the latest CAD/CAM processes and materials engineered by the company’s Research & Development department.
We work very closely with the Research & Development department. ... There’s some very exciting stuff coming down the line.
NP: So you’re treating patients with these new materials and products that our R&D department’s coming up with. And you’re also involved in the development itself.
JC: Yes. I’ll give feedback to the engineers and scientists from the clinical perspective, and we can exchange some of our ideas. I think it’s important for researchers to see the actual operatory environment and witness how challenging it is.
NP: Let’s talk about some of the products that have come out that you’ve had a hand in developing.
JC: Sure. One of those is BruxZir® NOW zirconia, which brings authentic BruxZir Solid Zirconia right into the office.
NP: This is something unique and different — other companies that sell millable chairside zirconia require the dentist to sinter the restoration after milling.
JC: That’s right. With BruxZir NOW, there’s no sintering needed. With other products, several hours in the oven are typically required to fuse that material together and get it to a final high strength. But we were able to create a sintered material. All of that oven time was done here, which greatly reduces creation time. It is still a hard, strong material, so it takes about 30–45 minutes to mill. However, to be able to offer that extremely strong restoration directly in the office is hugely beneficial.
NP: And you’ve also been involved in the development of Obsidian® Fused to Metal (Glidewell Laboratories; Newport Beach, Calif.).
JC: Correct. Obsidian Fused to Metal is a great bilayered restoration. One of the challenges with PFMs that I’m sure many dentists see is the fracturing of feldspathic porcelain. PFMs have been around for so many years — since the 1950s — and they addressed the issue of esthetics and strength. So they did and still do work well. But the weak link was the feldspathic porcelain. Obsidian ceramic is a lithium silicate material with about 385 megapascals (MPa) of flexural strength, and it’s very resilient and strong on its own as a monolithic material. But when it’s pressed onto a metal substructure, it gets even stronger and provides about 428 MPa of flexural strength. Obsidian Fused to Metal represents a significantly improved solution in terms of esthetics and strength for restorations such as long-span bridges.
NP: So that would actually differentiate Obsidian ceramic from some of the other lithium silicate products on the market, right? That it’s pressable to a metal substructure?
JC: Exactly. One of the key properties of Obsidian ceramic is the coefficient of thermal expansion. When a multilayer restoration gets fired, everything heats and expands. Obsidian ceramic is special in that the ceramic closely matches the expansion and contraction rate of the metal substructure, thus minimizing the risk of any possible fractures or stresses between those two different materials.
NP: That’s intriguing. So let’s talk about the recently launched suite of technologies that you’ve worked so hard on: the glidewell.io™ In-Office Solution. Tell us a little bit about this system.
JC: The glidewell.io Solution is the in-office CAD/CAM system Glidewell Dental has created that incorporates the user-friendly iTero Element® Intraoral Scanner (Align Technology, Inc.; San Jose, Calif.). The process of getting your digital impression with the iTero Element is what I like to call the “digital triple tray”: upper, lower and bite. It takes just 3–5 minutes to get your scans in using the iTero, and from there it transfers the impression data to the fastdesign.io™ Software. The highlight of the software is that it uses machine-learning algorithms to quickly propose an ideal restoration for you to accept or refine. So you don’t have to spend a lot of time functioning as a technician.
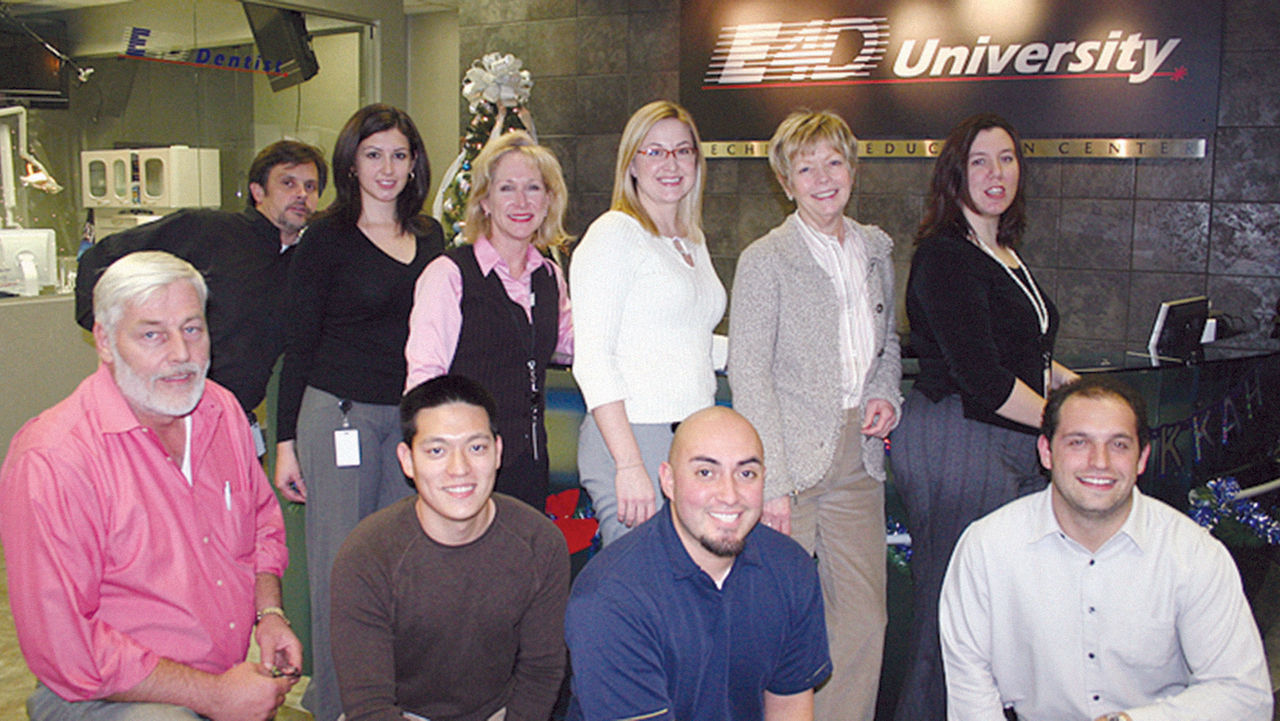
From 2007 to 2011, Dr. Chi worked at E4D Technologies as a dental technician and clinical educator.
NP: That’s great.
JC: You can do single-unit, full-coverage or partial-coverage restorations, and then send them to the fastmill.io™ In-Office Unit. The fastmill.io unit is an electric mill that spins up to a speed of about 100,000 rpm, and it’s very quiet. So it can be positioned anywhere in the office. And the footprint is very small. I’m impressed with the quality of the restorations that this mill is able to produce.
NP: So this is interesting. I think of in-office restorations as a three-step process: You have to capture the image, and for that we’ve incorporated the iTero Element scanner; then we have our own software for the design of the restoration; and then there’s the quality mill and materials to actually fabricate the restoration.
JC: That’s right.
NP: It sounds like a nice package. However, one of the things that’s kept a lot of dentists out of this arena is the cost. Where are we in terms of price? Have we managed to bring the price down, per the usual Glidewell way of doing things?
JC: Most definitely — with the Glidewell name, our focus is always on making dentistry more affordable. The entry point into this CAD/CAM system is much lower compared to some of the other systems, yet there is absolutely no compromise in material or restoration quality. As a technician, I would not trust the CAD/CAM system if it produced a restoration inferior to one made the traditional way.
As a technician, I would not trust the CAD/CAM system if it produced a restoration inferior to one made the traditional way.
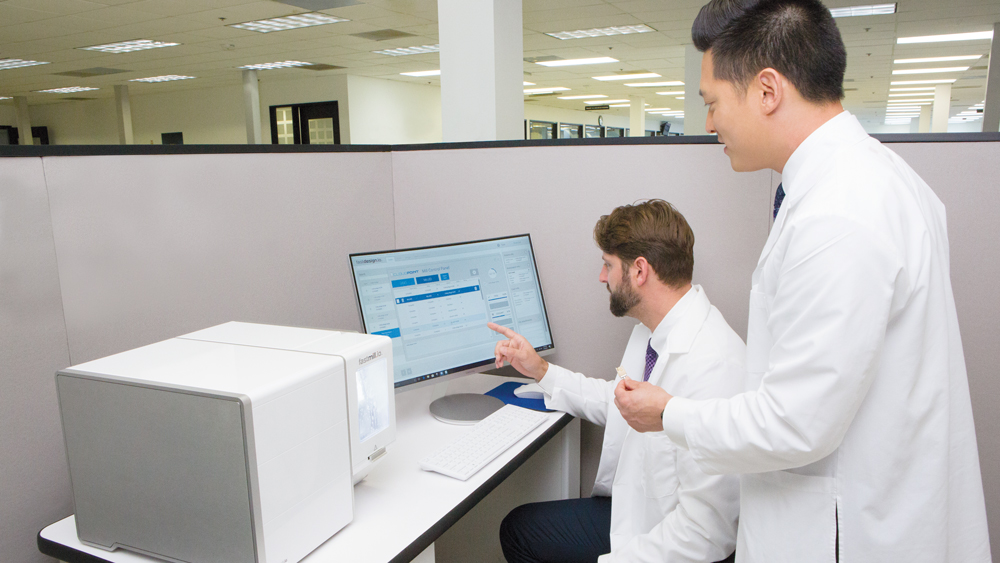
Dr. Chi has been involved in the development of the glidewell.io In-Office Solution, a comprehensive suite of technologies that streamlines the process of prescribing and delivering dental restorations.
We have four unique materials. Obviously there’s BruxZir fully sintered zirconia, which stands out and I think many people will enjoy using. Then we have Obsidian ceramic, the monolithic lithium silicate material, which is our esthetic, all-around material — you can use it for full- or partial-coverage cases. Obsidian ceramic would be my material of choice for the anterior region because you can characterize it and allow it to blend in with the surrounding dentition really well. The third material is CAMouflage® NOW, which is a resin-ceramic hybrid material. I love using it for inlays and onlays, and it mills extremely fast — in less than 10 minutes. I just finish that down and bond it in. And lastly, we’re soon going to release BioTemps® NOW, which is a temporary material.
NP: Well, that’s great. I’ve seen a lot of the inlays and onlays you’ve done. They look beautiful and the material is versatile. Maybe in-office milling could bring back the indirect inlay and onlay.
JC: It could. I think a lot of dentists want to get into CAD/CAM because it allows them control over the type of restoration that they deliver to their patient, and they can decide what’s best.
NP: And it allows for a more conservative prep than a full crown.
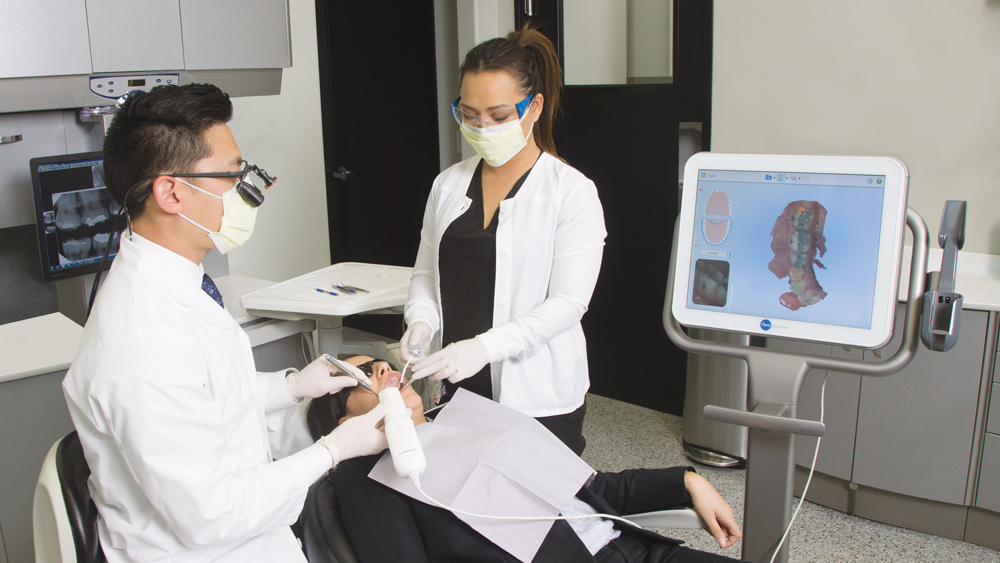
Dr. Chi using the iTero Element Intraoral Scanner, which is a component of the glidewell.io In-Office Solution.
JC: Definitely.
NP: But of course, the full crown is available as well.
JC: It is. And another unique aspect of the glidewell.io In-Office Solution is that it includes a safety net. So if anything were to go wrong — let’s say you’re working on a more challenging case — there’s a “Send to Glidewell” button, so you have the support of Glidewell right behind you. If at any point in the process you decide you need to have the lab mill the case, or if the patient doesn’t have the time, you can instantly submit the case and then have the restoration delivered back to you.
NP: That’s really interesting. So the glidewell.io In-Office Solution is the only CAD/CAM system that’s affiliated with a dental laboratory. And at any point during the process, you can decide to send the case to the lab. That’s a nice option to have.
JC: Absolutely.
NP: When I talk about CAD/CAM with a lot of doctors, the issue of deciding what to send to the laboratory and what to mill in-office comes up. Any tips for how to make that decision?
JC: I think most of what general practitioners do are single-unit posterior restorations — first and second molars, typically. That’s a great place to start with CAD/CAM. That’s where you’ll do your full-coverage BruxZir or Obsidian restorations. I find that, with most dentists, when you start to get into the esthetic zone and maybe a little more characterization is required, it gets a little bit tricky and requires the help of a dental technician or ceramist.
NP: Because unlike you, most dentists are not technicians.
JC: That’s right. I work with these materials to learn about them and help our R&D team enhance their esthetics, with the hope that we can make that process easier for general practitioners. With this glidewell.io system, I can confidently restore virtually any tooth in the mouth — any single-unit restoration — in one appointment. I think that’s something virtually everyone can get behind.
NP: Thanks for spending time with us today. I know you’ve been doing some exciting work and I appreciate you sharing some of it with us. I’ll see you back at the office?
JC: Sounds good. Thank you.